|
Post by 90GTVert on Jun 5, 2012 23:52:52 GMT -5
Condensed and better organized version of this thread can be seen in the Tech Library here : 49ccscoot.proboards.com/index.cgi?board=yamajog&action=display&thread=4300&page=1A while ago one of our forum members was selling a 49cc long case motor from a Vento Triton, missing a few bits and pieces. The major missing parts were the cylinder and piston. It was a good deal, so I picked it up with the hope of doing a "Project 49" someday. For those of you that have seen Project 90, basically that... but starting as a 49cc. 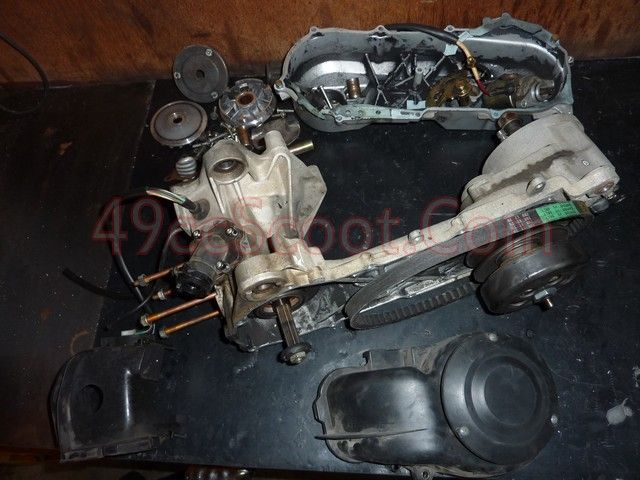 Unfortunately, I've come to the realization that a 49cc project similar to Project 90 is going to be out of the question for me anytime soon. For one, I just don't have much money to spend lately. Add on to that the very wide selection of parts out there for 49cc minarelli engines. I have quite a bit of 90-100cc parts, because 90-100cc 2Ts are what I like to have in my scoots. I have a very small collection of 50-70cc stuff. Just to get the most popular pipes and big bores and such for the 49cc would cost a small fortune. On top of all that there are parts that fail or wear and gas/oil and that sort of stuff that adds up as well. I'd love to do a big 49cc project someday, but it sure won't be today. What I have decided to try instead is a more casual project, I suppose you could say. I'm gonna get a stock engine together, mess around with it a bit, and see how much useful info I can put together in the Tech Library. Nothing fancy, but hopefully we'll end up with some info that proves useful for 49cc 1E40QMB riders and may even be interesting to watch. It's been so long since I've really rode and worked with a 49cc that it should be interesting for me anyway. I'm sorta not looking forward to putting my 300lbs on a 49cc. I think after years of riding 90+cc scoots it's gonna be a little tough to get used to the torque the larger engines have to get me moving quickly. I was close to the same weight when I got my first 49cc scoot and I liked it... but I had never rode a 90cc at that point. lol With all that said, let me get on to business here... I pulled the 49cc engine off the shelf this afternoon to start tearing it down a bit to be cleaned up. Here's some stuff that won't be going back on. Gotta have my pre-mix. 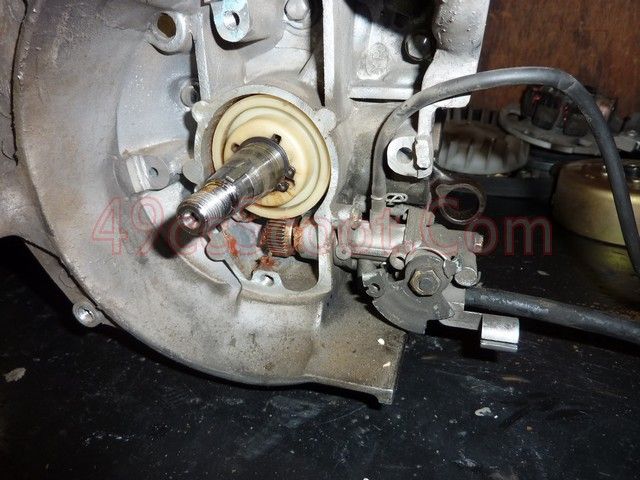  I checked the crank and bearings and such over some time ago to be sure the bottom end was sound. Double checked again today and that all looks good to go. One thing I noticed while looking the engine over was the poorly aligned and matched transfer and boost port areas. You can see in the pic below that the gasket/cylinder wasn't matching the case well at all (notice the brownish areas). 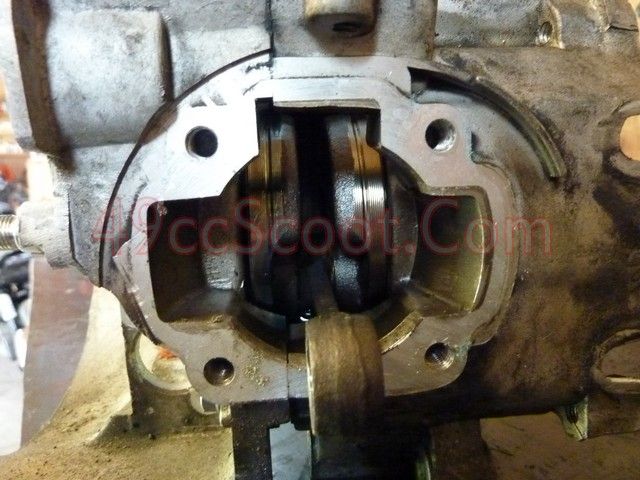 I dug out a stock 49cc gasket that I got from Vento years ago and used it to verify that this case is mismatched with a typical 49cc cylinder. 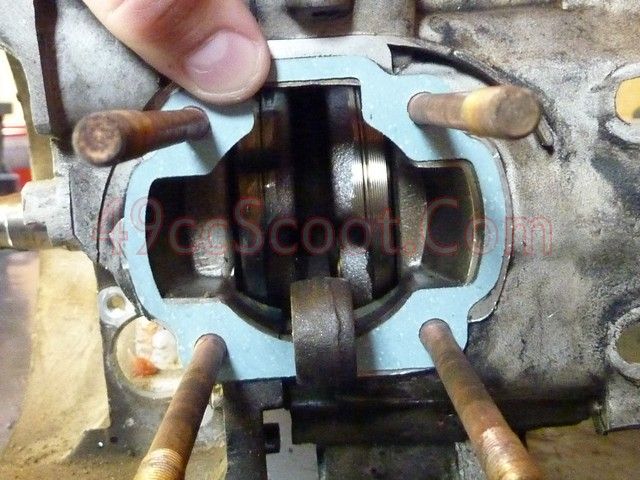 I suppose for a true stock test I should leave the case alone. However, looking at this just annoyed me and I'm sure some scoots come with cases machined propery. None of mine have, but there have to be some out there. lol I used a carbide burr and files to match the cases to the gasket. 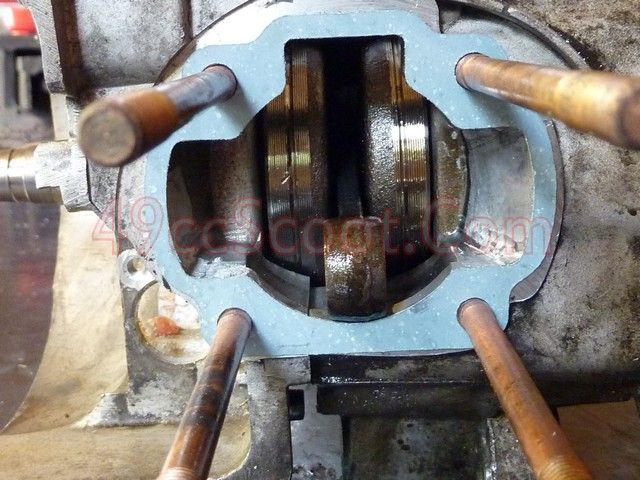 Once that was finished, I cleaned up the cases and CVT cover. 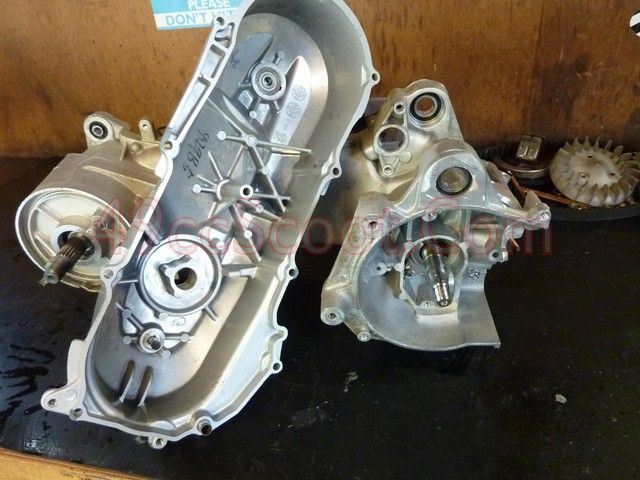 Next, I started trying to figure out what I wanted to do for the top end. I bought this stock replacement cylinder kit from Scrappy Dog Scooters shortly after I bought the engine, with the intention of it being used for Project 49.  I noticed the boost port seemed really small on the cylinder though. After some searching, I found the cylinder that came stock on my Keeway Venus and compared the two. As you can see, the stock Keeway cylinder has a much larger boost port. It matches up to a 49cc gasket and case well. 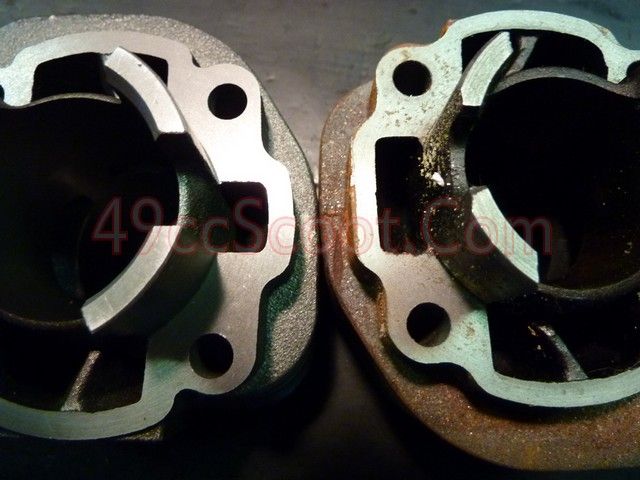 I started looking over the two cylinders a bit more and found other variances. In the photo below you can see the Scrappy cylinder has a very small circular exhaust port and a small flange. The stock cylinder has a half circle port, but it appears to be similar in size to the small full circle. The stock cylinder has a larger flange. You may also notice the stock cylinder is a little taller. 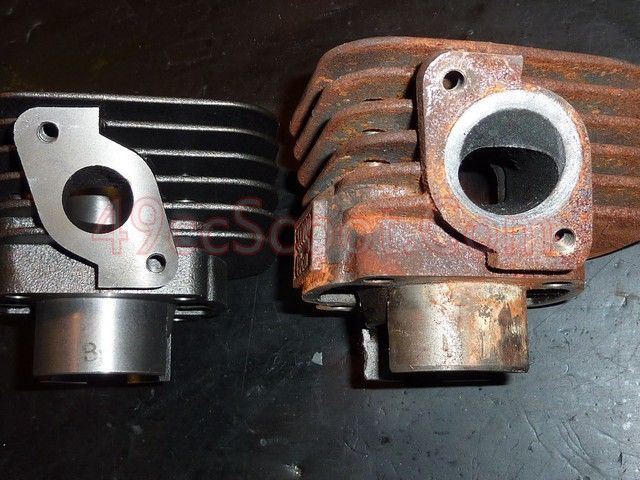 Inside the cylinders, the Scrappy kit has smaller ports than the stocker. You should be able to tell by their conditions, but the top is stock and the second pic is the Scrappy cylinder. 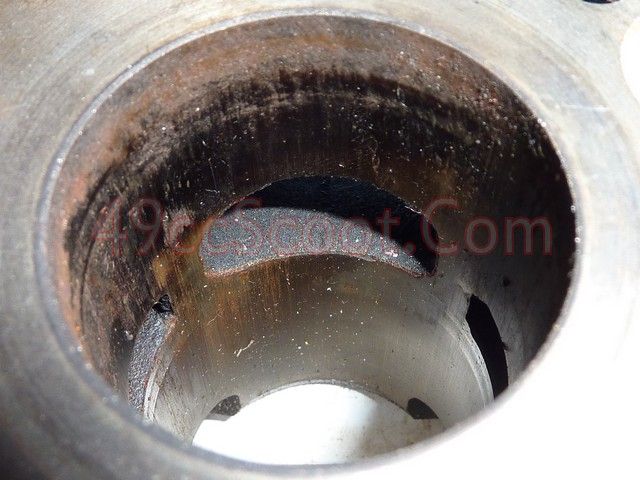  After looking at both cylinders, I decided to make a top end out of new and leftover parts. I'll be using the Keeway stock 49cc cylinder, the Scrappy Dog piston kit, a stock head, and of course stock gaskets.  I cleaned the stock head and then drilled and tapped it to accept a cylinder head temperature gauge sending unit. 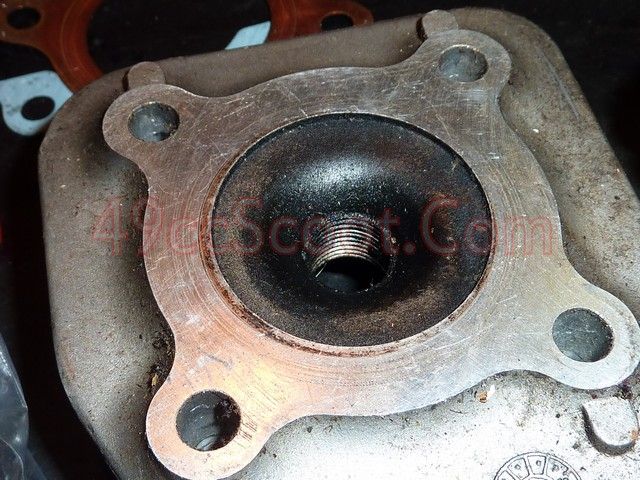 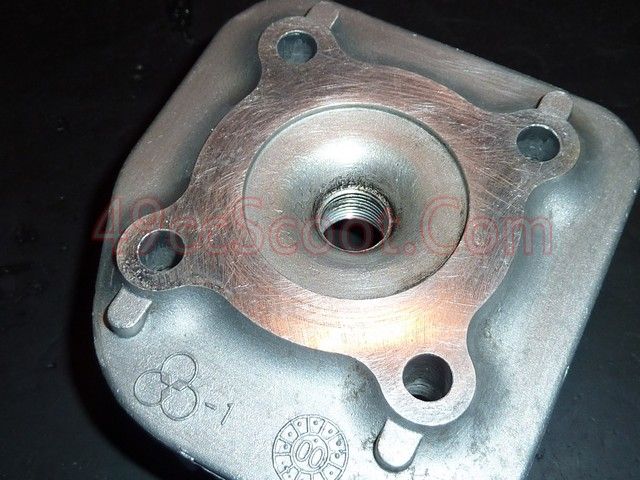 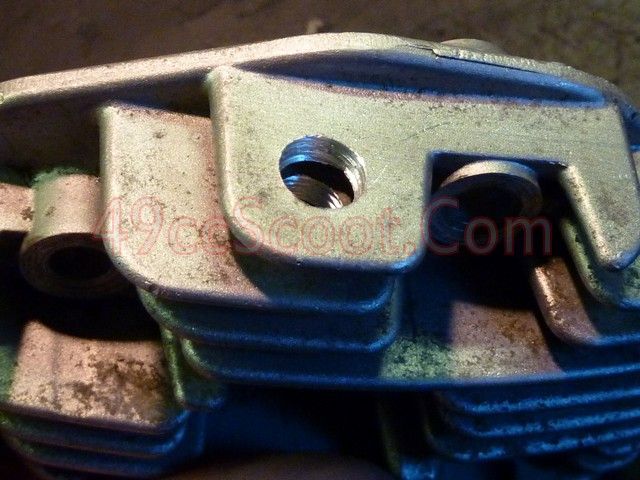 The stock cylinder had very low mileage so it's main problem was rust from sitting around so long. 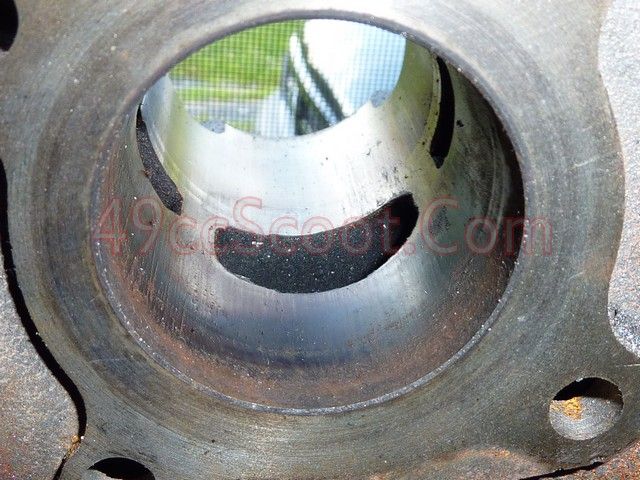 I cleaned, painted, and honed the cylinder and it was ready for use. 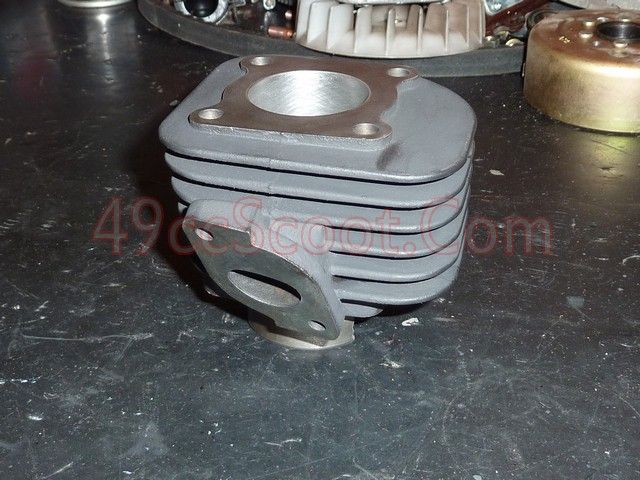  While I was waiting for the cylinder's paint to dry, I got the kickstart gear installed.  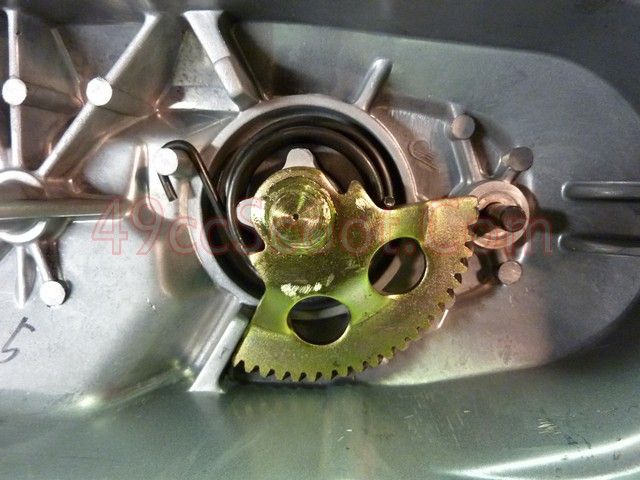 I moved on to engine assembly. When I mounted the piston to the connecting rod, I started thinking about 90ccs again and just had to compare the stock 40mm piston to a 54mm from a 90-100cc engine. 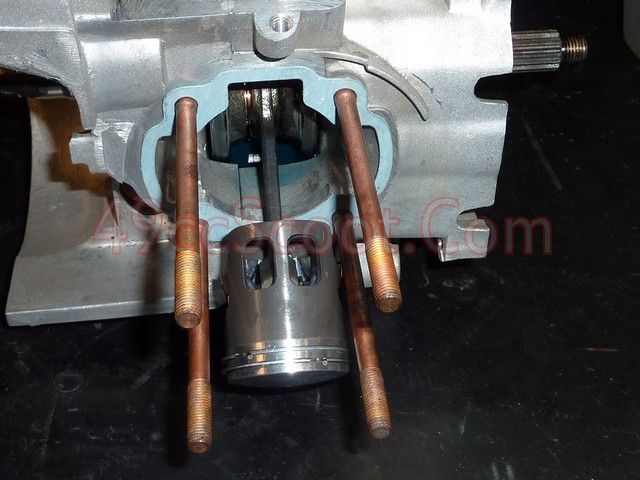 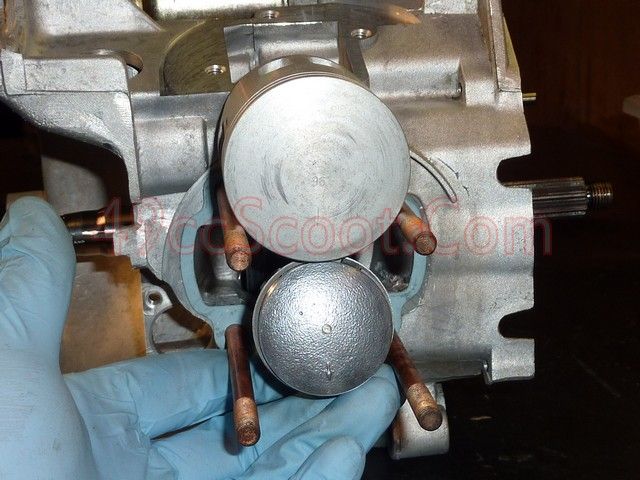  Once I finished daydreaming, I installed the cylinder. Not a bad deck height.  Even though the deck is pretty good, looking at the head and gasket it's obvious this engine's gonna have a lot of room between the piston crown and head. 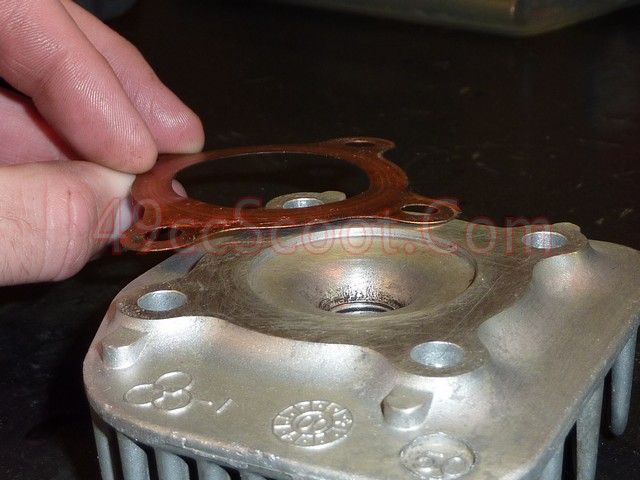 Sure enough, a check showed a minimum clearance of 1.85mm. That's a lot of clearance for a 49cc and I expect to see fairly low numbers when I get to a compression test. 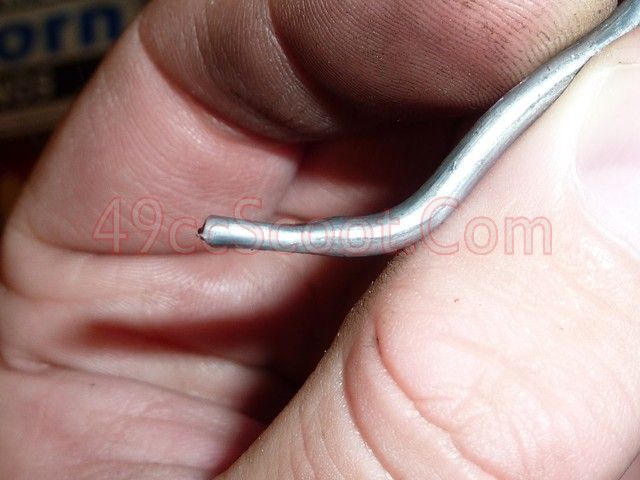 I installed the stock reeds and intake and then proceeded to do a pressure test. The intake/reeds are leaking at the gaskets. I'm not sure why I ever bother to try just gaskets for the reeds? Every time it leaks unless I use RTV. 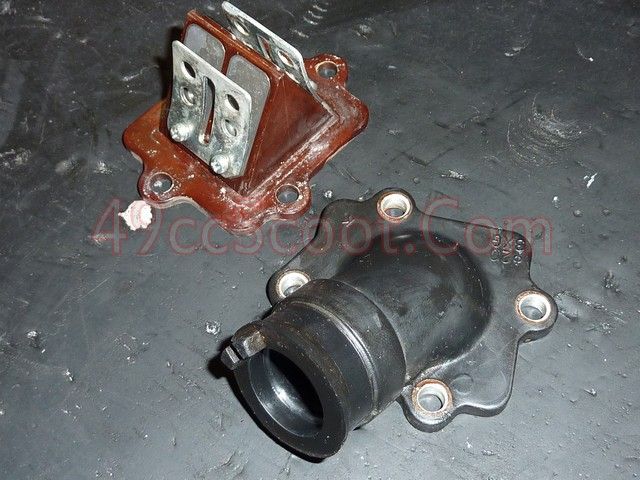 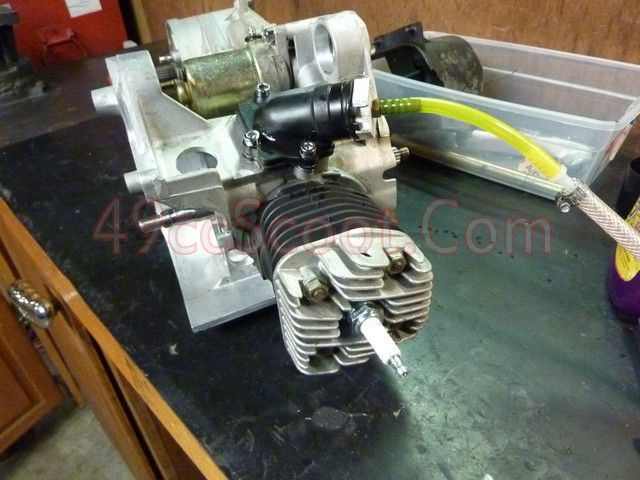 That's where I gave up for the night.
|
|
byte
Scoot Member

Posts: 51
|
Post by byte on Jun 18, 2012 17:39:37 GMT -5
I think clutch weight is the solution for your CVT .
|
|
|
Post by 90GTVert on Jun 19, 2012 15:00:53 GMT -5
lol I just got done putting together a fresh set of lights. That took me about 45 minutes. I'm so slow with small connections and solder. All soldered, glued, and installed and working now though. Fixed the CHT sender too. Forgot to mention the wire came out of there this morning as well. Ordered another caliper too. I have an old micrometer here that's my father's. I broke it already. It wasn't zeroed. I took the tiny little set screw out (meant to loosen and forgot how short it is) and immediately lost it. It's maybe 1.5x3mm and I cannot figure out where it went. 
|
|
|
Post by 90GTVert on Jun 19, 2012 15:57:18 GMT -5
I had been waiting to post till I decided if I was going to do any more mods as part of the tuning post I'll make at some point, which will be the second part of the organized thread in the Tech Library. I feel that anything else is more of a mod than tuning. I know I cut the CVT cover, which would be a mod, but that should be more about keeping it in tune with heat and longevity... and I just wanted to so  lol I rode about 40 miles last night. With the CVT in a better state of tune, cruise speeds have improved just slightly. Previously, cruising was mostly done from 37-40MPH. Now it's 38-41MPH most of the time with the RPM at 7300-7600 usually. Not a big difference there, but it helps a little. Gas mileage was lower last night at 55.44MPG. I was WOT pretty much all of the time. Even rode faster in town than normal. Gas mileage should be slightly decreased with a larger main jet when I'm WOT so much and revving higher, not sure if it should make 4MPG difference if I rode exactly the same. I did some 0-35MPH passes too, so here's a vid of one. Now, if you've seen that and are thinking... "Only .7 seconds quicker than stock?", let me explain what I've realized. I have realized, that I screwed up on the first run I put on video as the baseline. I have to assume the wind was at my back in that one. I had written down a bunch of times from when it was in stock or close to stock trim (carb tuning). The majority of the good times are 18.50 - 19.00 seconds and I don't think the carb tuning really changed times one way or the other, yet my first vid shows 17.78 seconds 0-35MPH. I think the best baseline I have on video would actually be the video from testing spacer vs no spacer in the variator when it did 18.58. If you use 18.5 as a base time, 17 seconds reflects the difference much better. It feels like it should be way faster than that, but I guess waiting to really move for 1.5 seconds extra just feels kinda slow motion when you have traffic waiting on you. lol I'd say pretty much all of the difference is from 0-20MPH or so. The rest I think just needs more horsepower to really wake up. Sorry for the mix up. Alexander Pope said, " To err is human; to forgive, devine." I'm just trying to give you all a shot at divinity. Yeah, that's it!
|
|
|
Post by 90GTVert on Jun 19, 2012 16:11:01 GMT -5
Almost forgot to mention, again I didn't really try for a max speed. It just doesn't pull much with me tucked down. I can go faster with a small wind gust while sitting up. I went 44MPH a few times with a tailwind. Max speed just seems pointless right now considering how easily the results are swayed by wind, inclines/declines, etc.... You can see above I'm, having a hard enough time keeping the easier bits accurate. lol
|
|
|
Post by 90GTVert on Jun 20, 2012 13:49:49 GMT -5
Now that the carb and trans are basically in tune, I wanted to do a couple of pretty much free mods. The thing that bugs me the most right now is the lack of power. Just doesn't seem like much there ATM. While I think there's room for improvement with a little port work, if I port it now I can't see how anything else works on a stock cylinder. I decided to start off by seeing if I could get more power via increasing compression. Before I proceed, let me remind you I broke my calipers and screwed up a micrometer, so I'm doing the best I can with measurements, some will be missing. I started out by removing the stock head gasket and using copper spray gasket on the cylinder head to help it seal. 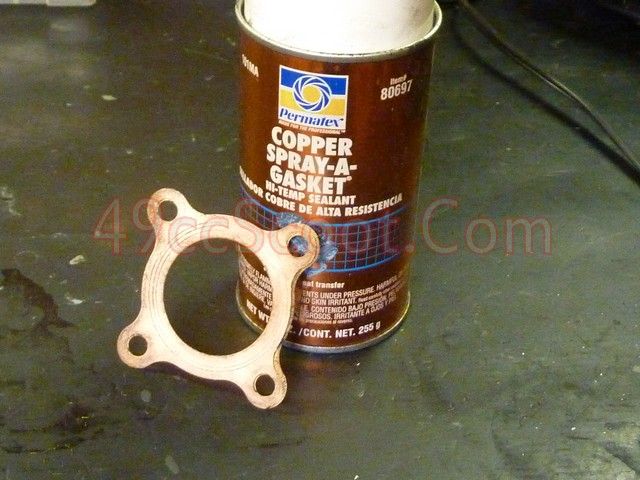 I use old caps or whatever I can find of an appropriate size to mask the combustion chamber and spray two coats within thirty seconds to a minute of each other. Let it sit for a minute to get tacky before installing. 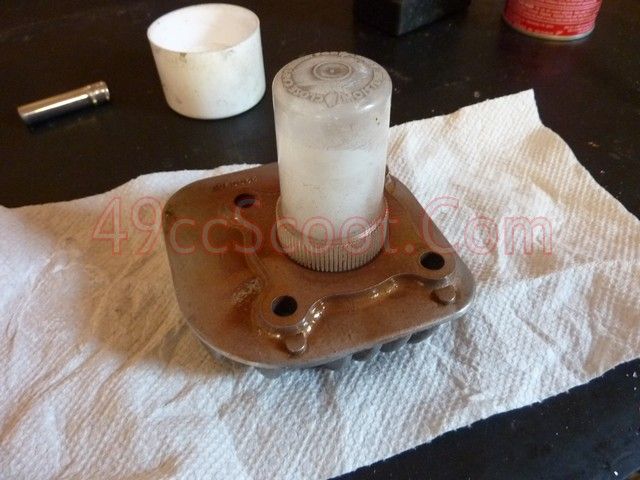 The best I can tell, the stock head gasket measured 0.3mm. That much change upped compression from 180 to 195psi. 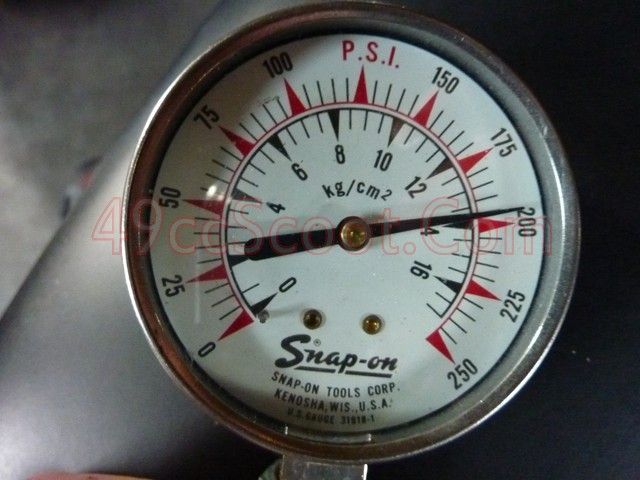 I took a ride last night and it revved slower and just seemed more sluggish. That seemed really odd to me. I've never increased compression and had it take off slower. I had taken the variator off at one point to check stuff over when I was doing the compression test. The kick start was slipping some. Turns out I was in a hurry and put one slider back in the wrong way. I put the slider the right way and rode again. The RPM was back. I rode about 5 miles and there just didn't seem like much, if any, improvement without the gasket. I took a longer ride later. It still didn't feel like much change. It seemed like there might have been a little more there as the clutch grabbed at lower revs. Otherwise it seemed sorta out of tune and was actually running slightly cooler than normal. I came to the conclusion that 90% humidity at that point was making it run too rich. The rides I had taken didn't give me all the feedback I would have preferred, but they were enough to tell me that temps with just 15psi more didn't change much as far as power or temperature. I also noticed that even under increased load from the sliders being out of whack, I heard no spark knock. Perhaps there's room for more compression? Today I dug around and found another 49cc head that I have. It has less of a lip on it's combustion chamber. My crude measurements showed somewhere around .4mm difference. Otherwise, the combustion chamber seems the same as the stock head I've been using.  I installed that and did another compression test. 225psi now. That's more than 40psi over where I started with the other head and a head gasket. 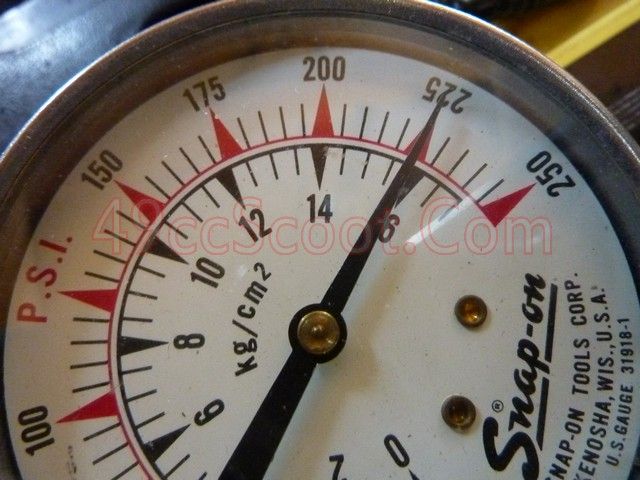 Normally you'd see me checking squish clearances here. It's hard to measure well ATM. I started out with 1.85mm though, and I should have removed somewhere around .6-.7mm. That leaves me with plenty of room to be safe. I took a brief ride a little while ago. Again the weather is being a pain. It's just under 100 degrees today, and it had been much cooler. If you recall, I had said the engine would take something like 6-8 miles in the past to hit peak temp of around 325F. It had maxed out my 340 degree CHT gauge within 2 miles today. I know that part of that has to be compression, but I assume part is also the extreme temp. The problem is, I don't know how much effect either is having for certain. I can't say I felt a big difference in power and again the engine just didn't seem to run right. My 2Ts never like really hot weather and/or really humid weather. One good thing was that even with the CHT maxed out on a very hot day, I still heard no spark knock. I plan to take a longer ride at some point when the weather changes. Not sure exactly when that will be. I would like to give this a fair evaluation, because I'd think 40+psi should make some difference and it's an easy gain assuming temps don't increase too much and I don't experience detonation. Granted, a lot of people don't have multiple heads sitting around, but you can even mill one with sandpaper and glass if you so desired.
|
|
|
Post by 90GTVert on Jun 20, 2012 17:25:57 GMT -5
It's such a small amount of power that every little variable affects it. If I were just modding for myself, wouldn't be as big of a deal. I don't wanna say something works great when it doesn't or doesn't do anything when it does though. The big motors just don't struggle with the wind, hills, or whatever variable in the same way. Doesn't hurt either that I have 4 90+cc engines, and this is the first 49cc I've ever modded. My first 49cc was stock, then went right to a big bore and more. I'm enjoying it when the weather isn't screwing with me though.
|
|
|
Post by 90GTVert on Jun 20, 2012 23:23:14 GMT -5
I went out tonight when the temp was around 85 and humidity was about 60% so I could see what the increased compression does without the elevated temps and humidity I had before. First off, CHT improved. The gauge didn't max out, but it was over 340F. Not sure exactly what it would be, but it's not all the way pegged at least. I rode a little over 30 miles and in all that time I never heard any spark knock. I'm still kind of surprised at that with 225psi cranking compression.
At lower revs I could feel an improvement. Definitely seemed like the engine was making more torque, as I expected it would. Not a night and day sort of difference, but it was unmistakably quicker off the line and at low speeds. Once the revs picked up, it appeared that the increase in power diminished. Eventually it seemed as if power output started to decrease vs lower compression. My previous peak output was at 7,500RPM. With the raised compression it seemed that pushing over 7,000RPM or so I was losing power. This was evident in cruise speeds. I could now only expect to cruise at 37-39MPH. It would push up to 40 on occasion, but not often. Max speed for the ride was 41MPH. Normally I'd see 43-44MPH at least, just from catching a bit of a tailwind or a slight hill. The engine just didn't want to rev out as easily as before.
I suspect that if I was able to retard ignition timing more above 6-7,000RPM, I may see more of a benefit from the compression. Perhaps a larger exhaust port would help? Maybe increased cooling ability? A different cylinder head design? I'm really not sure. What I am sure of is that this was not the cheap and easy power increase that I had hoped for.
This is a definite no, at least pushing up to and beyond 200psi, in my book. Not only do you get worse high RPM performance and increased heat, but it's going to be harder on engine internals.
I will probably be going back to using the head I started with and a head gasket to see around 180psi again.
This was sort of an odd experience for me. The times that I have ran the 90+cc engines with elevated compression, I've seen an improvement all around. My limitations with compression on those has always been heat and knock. I've experienced knock well before any sort of power loss. When I first built the engine in the Venus I had very high compression. It ran amazing... other than the fact that it had crazy spark knock and got so hot that it ran on when I turned the ignition off.
|
|
byte
Scoot Member

Posts: 51
|
Post by byte on Jun 21, 2012 4:34:50 GMT -5
Thanks for that good and informative result. So at 180psi is good. What best compression(psi) range can you suggest for optimum performance and reliability?
|
|
|
Post by 90GTVert on Jun 21, 2012 8:42:30 GMT -5
I know with the 90s I shoot for 180psi max. I haven't tried lower than 180 on the 49cc, since it was like that stock. It's so low on torque and it seems to pull fine to where it's peak should be with the mild porting it has, so that seems like a good number. With 195psi it seemed weaker up top. I thought it was just the effects of humidity on jetting, but after seeing what happened with even more compression I don't think that's all I was noticing. I haven't tried lower, but I'd think you'd want to stay within 150-180psi if you expect decent performance. Most seem to go off of effective compression for guidelines (using the volume above the exhaust port's roof instead of total cylinder volume). Unfortunately I don't have those numbers. Seems it would be kinda hard to get them when the engine is horizontal ATM, and I don't feel much like removing it right now. If the piston were flat I could just measure deck and calculate, but being domed I'd have to actually cc it. Whether it's technically an accurate way of deciding on a compression level or not, cranking compression has worked pretty well for me so far and it is a very easy method that I think the avg person is more inclined to do than trying to get an accurate measure of the combustion chamber. Doing a head is simple, but it's more of a pain to get the whole picture including the piston.
|
|
|
Post by 90GTVert on Jun 23, 2012 16:24:43 GMT -5
After some less than impressive results with high compression, I went back to the stock setup, right around 180psi. I got a few measurements, and at some later date I'm hoping to see what cc the piston crown displaces so I can put together some corrected and uncorrected figures along with the psi in case they are helpful. Next up, I wanted to play with the clutch a little. I had originally intended to just leave it as a sidenote with the clutch tuning that you could opt to drill the shoes. After forum member byte bringing up lightening the clutch to help it slip in and possibly see a better launch, I thought it was worth another look. I have lightened clutches in the past, but I've really only done it to get later engagement for high revving setups. I can't say I've noticed a real difference in engagement with what I've done in the past. I assumed you'd need to go much ligher, like an aftermarket clutch or perhaps so much material removed from the clutch that you may risk a failure. Even if it worked no better than springs, it would be an opportunity to save $10 on a set of springs. Worth a look. I already have a clutch around in good condition that I had lightened in the past. I used this to save me a little work and so I could keep the stock clutch, should I decide to use it later or need it for any reason. 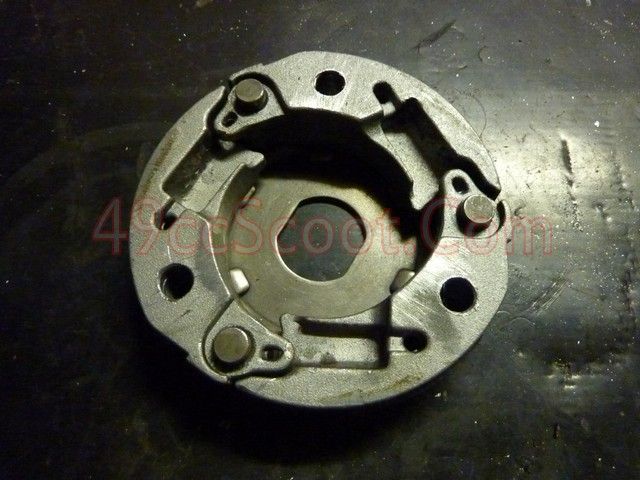 I started out by removing the shoes and weighing them. They were all 165-166 grams. I had drilled holes using the stock "JOG" markings to try and keep the weight removal in roughly the same spot on each shoe.  I wanted to remove a little more weight to see if I could get a little slip that I may notice. Removing weight farther from the pivot point (at the pin the shoe rides on) has a greater affect than removing weight closer to the pin. Always look at each side of a shoe before deciding where you want to modify it. You can see on the rear of the shoe there is a sort of groove on the far left of the pic below, marked with an arrow. That's where the shoe rides on a rubber bushing on the back plate of the clutch. I did not want to drill there. While it may be fine, I thought it could cause the clutch to hang up or damage the rubber bushing. I chose to drill where marked with a red circle in the image, so I had enough to reference that I could keep the weight removal in a similar spot on each shoe. The hole just to it's right is where one side of the clutch spring hooks in on the other side and the other hole is where I had lightened the shoe already.  All 3 shoes drilled. 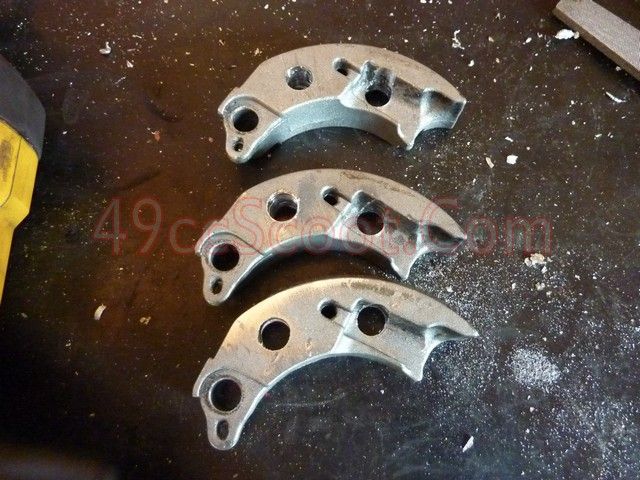 I weighed each shoe. The lightest was 159.5g. I drilled just a little more out of each hole in the other two shoes until they all weighed the same.  Once all of the shoes were the same weight, I reassembled the clutch using 1,000RPM springs and put the CVT back together. I was using 1,500RPM clutch springs in the stock clutch with no weight removal. I knew the weight would make engagement later, and that's why I started with the softer 1,000RPM springs. 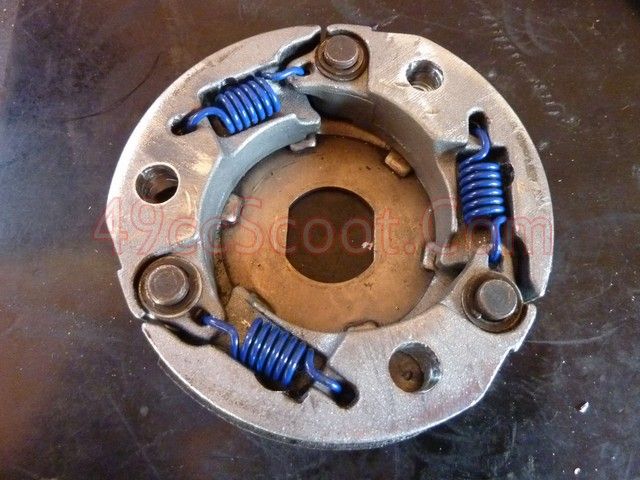 Even 1,000RPM springs were stiff enough that the belt was moving quite a bit before the clutch tried to engage on the stand. I did a few launches in the garage and once on the road. I'd say it was roughly comparable to the stock clutch with 2,000RPM springs. Not terrible, but I'd prefer to keep the belt from moving too much for the best takeoff. I went to stock springs. The belt moved just a little, but no more than with the 1,500RPM springs I chose for best acceleration in the bone stock clutch. Some launches in the garage and driveway seemed promising so I took it out on the road. The clutch was engaging at 5,300-5,400 RPM just like the stocker with 1,500RPM springs installed. It seemed to slip enough to see the upper 5,000s to 6,000RPM sooner though. Not a big difference, but at very least it seemed to do as well as the aftermarket springs. I was curious to see if I'd see a difference in time and also wondering if the weaker stock springs would fade much, so I took a 33 mile ride this morning for a good test. 16.75 seconds 0-35MPH is the fastest time I've seen so far in the project. It's close enough to the last best on video of 17.07 seconds that I can't call it a great improvement. With room for error, I'd say the difference is minor. The biggest difference that I saw was one I didn't expect. It seems that the stock clutch springs and lightened shoes actually don't fade as much as just aftermarket springs. In fact, even at 85 degrees in the morning sun and riding around town a bit, I never saw a difference in launch. I'd say if you are willing to take the extra time, this is a mod worth doing. It'll save you a little money, when done right. (Remember, if you mess up the stock clutch you'll spend a lot more than springs cost to replace it.) Improved performance, with seemingly no fade (also remember I have a vented CVT cover), for just time as long as you have a drill and bits and the tools to disassemble the CVT. You'd need the same tools other than the drill and bits to do clutch springs anyway.
|
|
|
Post by 90GTVert on Jun 23, 2012 17:37:34 GMT -5
On the way home on the clutch test, I had an odd "shift" 3-4 times. It would get up to about 30MPH, then drop out of power for a second, and then back to normal. Then it quit and never did it again. I took the whole CVT apart anyway to check it out and clean it.  My best guess is the worn area in the torque driver may be causing it to hang. It's been there since day 1 with this project, but it does look a little worse than it started. 
|
|
byte
Scoot Member

Posts: 51
|
Post by byte on Jun 24, 2012 4:41:08 GMT -5
Nice result and good info.
Do you use torsion controller or you just grind the spring edges ?
|
|
|
Post by 90GTVert on Jun 24, 2012 9:12:08 GMT -5
No TC and no grinding. I cleaned everything... even though it was still clean anyway... and replaced the torque driver with another I had here that looks just like it but new. Runs well again. 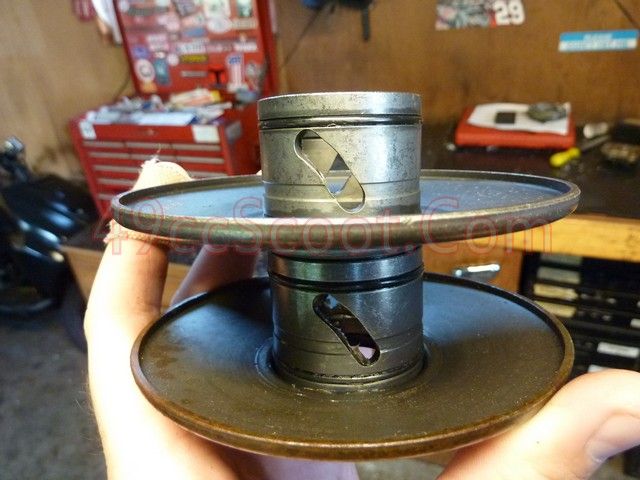
|
|
|
Post by 90GTVert on Jun 24, 2012 10:30:48 GMT -5
I decided to try a modified fixed drive face (variator fan) next. I have one around already done from past projects. As you can see in the photos below, I filed the face to a steady angle all the way across instead of having the recess and flat spot in the center.   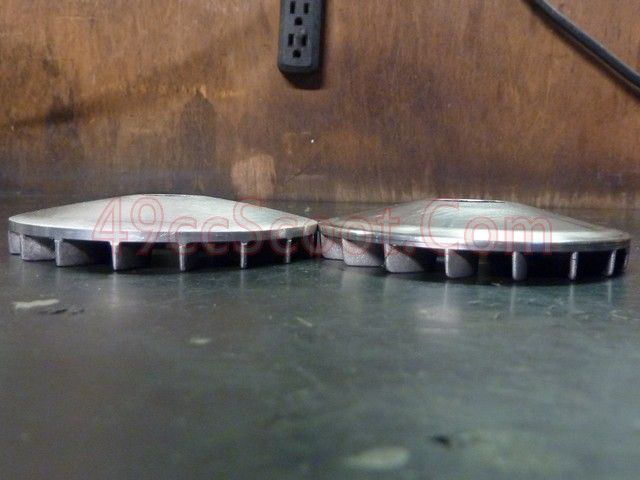 I moved the spacer to the outside of the variator, because the belt could rest all the way in the center of the front pulley without it for the best takeoff gear.  Even though I could get a better launch, I had to move from 5g to 4.5g sliders to keep cruising RPM where it needs to be. Even with 4.5g sliders, RPM was just a bit low at cruise speeds, but I don't have a way to make weights other than in .5g increments. 0-35MPH times were worse than with the stock drive face. It went well from 0-20 or 25MPH. Then it settled into a less aggressive gear ratio than before and struggled more to gain speed to max. I ran it up to 46MPH (on a decline) to take a look at belt travel for comparison to previous checks. At just over 5mm left on the drive face, it was right on par with the results I got when I removed the spacer and used the stock drive face. So this way I was getting both a better takeoff ratio and a better top speed ratio.  The problem with that better ratio for speed is that the stock engine has a hard time pulling it, at least with a heavy rider. I found it just slightly harder to maintain cruise speeds when faced with wind or inclines. It didn't help that I was a little short of cruise RPM as well, so I tried some spacers out to see if I could help it work a little better. I started out with the stock spacer. With that in place, cruise RPM was too high. I started out around 7,200RPM at 40MPH. With the spacer in place it was over 7,600RPM, and the stock engine does not like to go much beyond 7,500. I have some shims around that I use for tuning variators, so I decided to try one of those. The stock spacer is 1mm thick, and I had a shim 0.5mm thick.  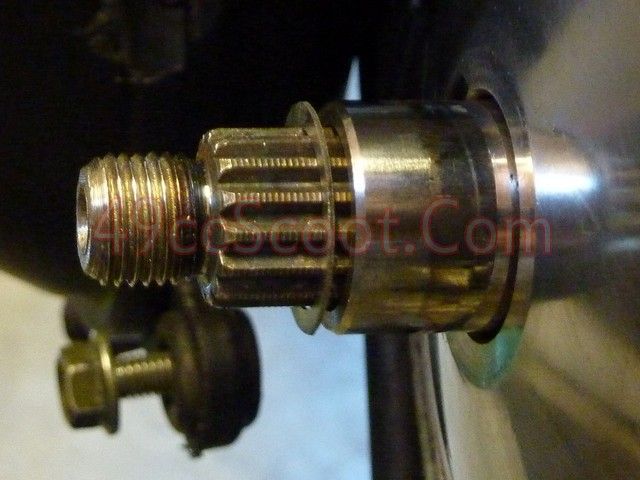 I used another .5mm spacer on the outside of the variator to keep the splines recessed in the kick start washer. 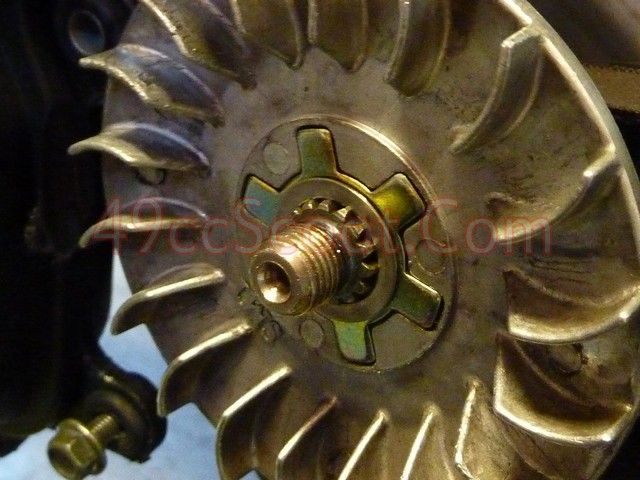 With the 0.5mm shim in place, cruise RPM was about right at 7,400RPM at 40MPH. It cruised about as well as before at that point. So then I had a little better launch up to 20-25MPH, worse till about 35MPH, and then about the same at cruise. I'll be going back to the stock drive face for now. With a lighter rider, more power, deeper final drive gearing/smaller rear tire it may work out better. If you have the ability to fine tune the drive face through machining, I think you could get a good result. It may take a lot of time and tinkering, and possibly a replacement variator. Small changes could make a big difference. I'm only working with a metal file and some sandpaper to do my drive faces, so it's difficult to change angles. Still, this mod has worked great for very well for me on my more powerful scoots to squeeze out good launches and more speed. With enough power, it'll pull through a lot easier if there's a bit of a dead spot. Unfortunately Stock 49cc + 300lb Rider ≠ Pulling Power. lol For reference, just in case anyone finds it useful, I tried to take a few measurements and figure out the angles of stock and what I had done. Stock has a rise of 8.05mm and a run of 33.25mm, making an angle of 13.61°. Modified has a rise of 7.55mm and a run of 38mm, making an angle of 12.79°. I tried using a protractor to check angles, but that was difficult to see. The measurements were a little tricky too, so I won't say they're dead on either. Since spacing out the variator an extra 0.5mm worked out best with the modded face, I'm thinking a rise of 8mm with the same 38mm run (essentially the whole drive face) to create an angle of 11.89° is what I'd try if I had the ability to do precise machining. At any rate I'd say leave it alone with a stock engine unless you really enjoy modding and tuning and are willing to risk making your scooter run worse if you get it wrong. EDIT : Almost forgot, I get the shims from McMaster-Carr. They are too large outside diameter to work without being a restrictor as they come, so you have to grind the outside down until they're the same size as the drive boss. I don't know anywhere that sells shims specifically for this task that require no work though. I believe Stage 6 or some manufacturer sells them for the small spline cranks. They carry a lot of stuff so there may be something in the catalog that works better, but for my large spline cranks I use : 98089A352 Metric 18-8 Stainless Steel Shim, 0.5mm Thick, 16mm Id, 22mm Od 98089A396 Metric 18-8 Stainless Steel Shim, 1.0mm Thick, 16mm Id, 22mm Od You can get them in spring steel as well, but they're only $1-2 more for a pack of 25 in stainless.
|
|