|
Post by gsx600racer on Aug 21, 2017 1:21:53 GMT -5
On both of my Kymco's ZX50's, there is a hose that comes off the shroud. Its aimed down towards the oil injector pump/starter. The manual does not document or show this. Kymco parts sites do not show this as well. Anyways, I been tuning(cvt) one of them and after a test run I pull the CVT cover and everything is scorching hot to the touch. The CVT is designed to be completely closed.(some what air tight) There are many people that have opened them up by adding holes, cutouts, ect. Unfortunately I like the idea of it being sealed and keeping dirt out, but the heat got to be shorting the life of the CVT drivetrain. I made this up awhile back, but I still have a few issues I need to work out. 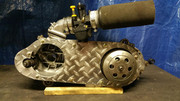 So I thought id bite the bullet and put a few holes in the stock cover. Tube off of engine shroud. 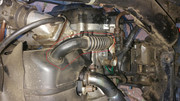 I though Id bump it over to this location over the CVT cover. 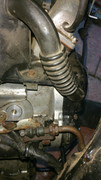 Then modify the cover and add a copper 45 elbow.(hot glued in place for reference) 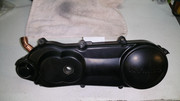 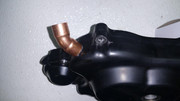 The drill a couple hole at the rear of the cover(side or bottom) 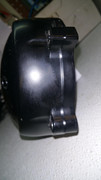 Now I know I will get some "heat" for this idea(taking slightly heated air from the cylinder and piping it into the CVT), but I did put a "K" thermocouple in the tube and connected my DMM that does temp and you will be surprised of the results. 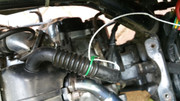 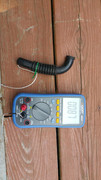 I did some riding with my DMM bungee-corded to the flloor board. It was about 80° out and ran wide open for a couple miles, engine temps were in the low 300's. The is what it measured when I pulled over for a pic. 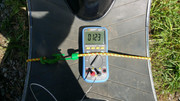 The highest I seen it go was in the low 130's. Depending on rpm's and the temps varied a little bit.(10-20°) Next I need to go on a run with a only a few screws holding on the CVT cover and use a Infrared Temp Gun to measure cover temp and remove it quickly and measure inside as well. I suspect the inside will be in the mid to high 200's.(seeing CHT temp are in the 300's) 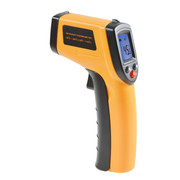 So is this mod worth doing or am I crazy to think it up ?
|
|
|
Post by ThaiGyro on Aug 21, 2017 1:53:51 GMT -5
Hey GSX, It is a good idea and not new. The Honda Gyro's, at least Asia models have some thing similar. The air box doubles to hold an external filter and inlet tube that goes into the side of the CVT cover. There is another tube running under the exhaust that goes directly into the fan shroud. The engineering idea here is to pull filtered air through the CVT case, reducing the heat. Thus, it is the opposite direction of airflow from your plan. My Yamaha Mio has a similar design. The Honda from '85, the Yamaha is 2014. Both take in air to the CVT from a high position to avoid water. I am more of a fan of using cooler air for the CVT, then routing to the cylinder shroud. I believe that you should route air from coolest to hottest source, to gain the most in temperature exchange. Not sure where your temperature is coming from, but 300 seems too hot for the cover from my thinking...but either way, you are right to want to vent the heat out. I will find some photos, if I can. It may take a few days, as we are out of town. I have parts diagrams, but you need too many to get the idea. I have the engine apart at home, so can easily show "bench" views. Here is a picture of the intake filter and tube, just under the frame, inside the rear tire.  Note that I used a better filter...the OEM one was flat and inside a funnel shaped inlet. It enters the case directly next to the top part of the belt.
|
|
|
Post by Raizer on Aug 21, 2017 5:29:51 GMT -5
Gyro:  Not great pics, but hopefully the idea is shown.
|
|
|
Post by oldgeek on Aug 21, 2017 5:45:21 GMT -5
None of the 4 Kymco SC10 motors I own have the tube coming off of the shroud like yours does.  Anything you can do to cool the CVT helps extend the life of its components. In the electronics world heat is the eventual killer of most components, and any excess heat significantly shortens the life of the device. The same is true regarding the CVT IMO.
|
|
|
Post by ThaiGyro on Aug 21, 2017 5:53:47 GMT -5
I wholly agree oldgeek...In fact, if you really look at failure mechanisms...is is the largest contributor. Even piping systems with corrosion/erosion issues are compounded by excessive heat. LIghting, switches, breakers, clutches...
|
|
|
Post by gsx600racer on Aug 21, 2017 13:48:17 GMT -5
Hey GSX, It is a good idea and not new. The Honda Gyro's, at least Asia models have some thing similar. The air box doubles to hold an external filter and inlet tube that goes into the side of the CVT cover. There is another tube running under the exhaust that goes directly into the fan shroud. The engineering idea here is to pull filtered air through the CVT case, reducing the heat. Thus, it is the opposite direction of airflow from your plan. My Yamaha Mio has a similar design. The Honda from '85, the Yamaha is 2014. Both take in air to the CVT from a high position to avoid water. I am more of a fan of using cooler air for the CVT, then routing to the cylinder shroud. I believe that you should route air from coolest to hottest source, to gain the most in temperature exchange. Not sure where your temperature is coming from, but 300 seems too hot for the cover from my thinking...but either way, you are right to want to vent the heat out. I will find some photos, if I can. It may take a few days, as we are out of town. I have parts diagrams, but you need too many to get the idea. I have the engine apart at home, so can easily show "bench" views. Here is a picture of the intake filter and tube, just under the frame, inside the rear tire.  Note that I used a better filter...the OEM one was flat and inside a funnel shaped inlet. It enters the case directly next to the top part of the belt. Thanks for the FYI. I was unaware of this with Honda's.
|
|
|
Post by gsx600racer on Aug 21, 2017 13:49:41 GMT -5
Gyro:  Not great pics, but hopefully the idea is shown. Thanks for sharing. I got a pretty good idea how they do it now.
|
|
|
Post by gsx600racer on Aug 21, 2017 13:50:53 GMT -5
None of the 4 Kymco SC10 motors I own have the tube coming off of the shroud like yours does.  Anything you can do to cool the CVT helps extend the life of its components. In the electronics world heat is the eventual killer of most components, and any excess heat significantly shortens the life of the device. The same is true regarding the CVT IMO. It could be a colder climate thing. Who knows 
|
|
|
Post by niz76 on Aug 21, 2017 21:21:08 GMT -5
Most Adly 2t scoots have this as a stock function also- the tube that takes air from the cooling shroud over to the CVT cover just as you've done...
|
|
|
Post by ThaiGyro on Aug 21, 2017 23:41:11 GMT -5
I would caution you to look at the actual location of the tubing connected to the cooling fan shroud, so you make make the right judgements. Mine is near the center, just below the air inlet, so it is drawing in air into the fan, (induced draft) from the CVT. If it were on the high pressure side of the fan blades, closer to the engine case it would be supplying air to the CVT.
For my thinking, the filter is the verifying feature. Not need to filter outgoing case air from the CVT, but you certainly want it filtered in. Mind you, it is not a high volume, as it is induced via a very minor vacuum that exists, as the main cooling air passes across the tubing port.
For anybody reading this: There was a thread a while back regarding the shroud itself. Many have had the idea of removing it or creating more fan air to gain cooling. I will defer to the original engineers design first. If I have cooling issues, as gsx600racer does, then it is time to look for alternatives. Figure out what the excess heat is caused by. Go from there. gsx600racer is doing his testing using measured data. Cooler CVT's always work better and more reliable, as oldgeek stated above.
CVT's come both vented and un-vented designs for various reasons. Off-road racing is super dirty, so cases tend to be sealed...Snowmobiles are both. My friends racing Polaris is not vented. I think in any sense...there must be an issue creating the heat. Worn belt, wrong belt, weak clutch, excessive slippage caused by many things, even output shaft bearing issues. The racing snow mobiles use both temperature and/or belt speed sensors, often measured in more than one location.
|
|