|
Post by 90GTVert on Mar 24, 2016 15:33:10 GMT -5
Amazon said these wouldn't arrive for another 5-7 days, so it was a nice surprise when they showed up. 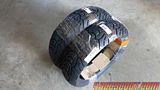 I mounted both tires and balanced them. The front only needed 0.18oz to be balanced. The rear took 1.25oz. I had to use little weights so they'd fit. Got it all back together and finished the CVT cover. I painted the aluminum that I had to leave for the dot in the cutout flat black. 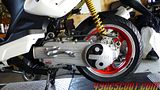 I took it for a ride andit never really felt like it was going to kill me, so that's good. There's still a lot to be desired with this scoot though. The brakes aren't good. The front brake kind of feels like 4 separate stages of braking, rather than being able to apply as needed and have stopping power delivered in a linear fashion. The suspension isn't good either. It seems to exaggerate bumps. I never changed the main jet when I put the K&N pod filter on, or any other settings for that matter. The plug was dark with the stock airbox, and it did use a 115 main jet in the past with this filter, so I thought it would be a decent starting point. It runs better and cleaner now, but I'm really hoping there's more power in it with further tuning. I managed to make it up to about 54MPH half tucked with a 10-15MPH tailwind at one point. Then I went out on the main road and got hit with a headwind and it didn't want to go much past the low 40s. I ended up pulling over and riding the rest of the way on the shoulder.  Got home and half the wheel weights were gone. They really don't seem to want to stick to the polished lip and I don't have any desire to rough it up. I'll probably get some Ride-On or maybe just pour Dyna Beads in there and take the weights off.
|
|
|
Post by 90GTVert on Mar 25, 2016 21:03:59 GMT -5
I went into town last night, just a ~5 mile ride. Normally I won't ride something much when it hasn't been tuned, but it seems well enough and the wind won't let up so I can tune. I got up to 58.8MPH half tucked with a 20MPH tailwind... but I was doing 35MPH at one point against it. The headlights sucked. Neither high or low beam put out a good beam that covered the road so I could see what was ahead of me very well. My first thought was maybe I could put H4s in place of the BA20Ds. I fiddled around a bit, but I didn't see any way to do it relatively easily in these housings. Aside from that, I had a 60W high in and a 35W low. Both had some signs of melting. I can't recall if I ever put anything brighter than 35W in the low side. Doesn't seem like a 35W should be melting much. 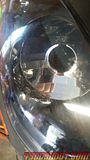 The 60W wasn't looking too good, and I know sometimes different bulbs have different patterns, so I decided to just swap both to 45Ws and see if that helped. 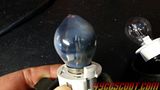 While I was in there, I drilled into the fake projector part of the headlight and installed an amber 194. I thought it may be an alternative turn signal, but it's way too dim and the 194 bulb barely fits. Not worth keeping and wiring as running lights because I'd rather have that power for headlights. 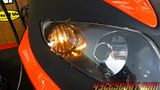 I went for another quick ride tonight to see how the 45W bulbs are. They are a definite improvement, but still not what I'd like to have. What I'd like to try is using dual high and low beams. The problem is that each socket only has one connection. 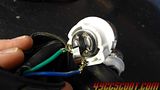 If anyone knows a source for this style of connector so I could add one to each socket, please share. Even a source for a whole socket with 2 connectors would work. Anything I've found is around $15-20 for a socket. Below is the best link I have ATM and that seller is away. The rest come on a slow boat from China. www.ebay.com/itm/HEADLIGHT-BULB-SOCKET-IGNITOR-WIRE-BA20D-GY6-CHINESE-SCOOTER-TAOTAO-VIP-PEACE-/121802042613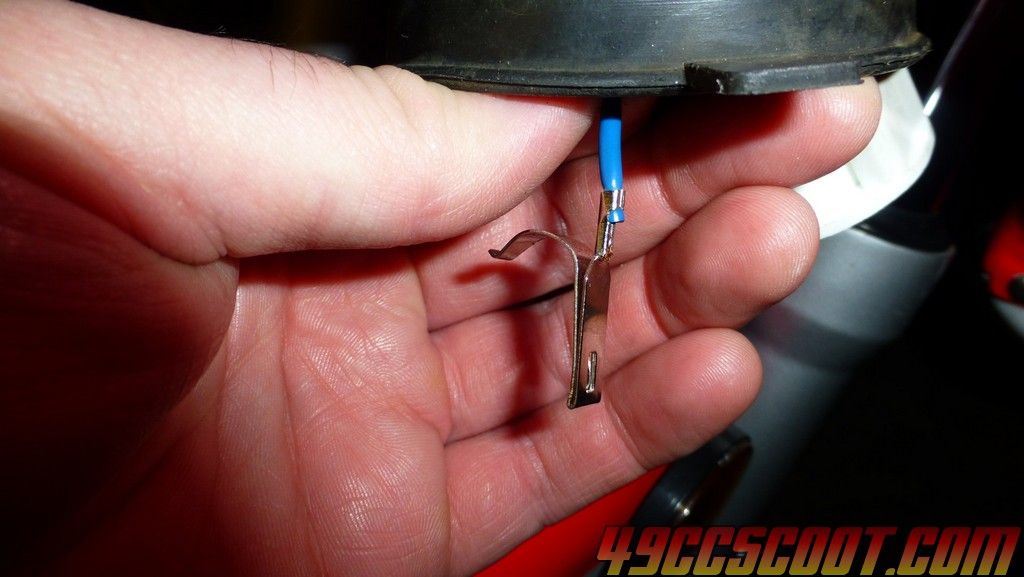 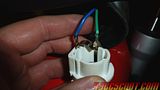
|
|
|
Post by spaz12 on Mar 25, 2016 21:33:24 GMT -5
Just a thought, with your skills and some spare metal laying around, couldn't you make two more of those tabs/pins? It looks like the slots are already there and waiting.
|
|
|
Post by 90GTVert on Mar 26, 2016 5:41:22 GMT -5
Just a thought, with your skills and some spare metal laying around, couldn't you make two more of those tabs/pins? It looks like the slots are already there and waiting. I thought about it, but I'm not sure how successful I'd be. Haven't checked, but I'm not sure if I have metal around that thin. It has to be thing enough to be doubled over and fit the receptacle. If not, the cost of a small sheet of steel would be similar to just buying a socket or connectors. Maybe a junk can or something could work. I can see it taking a bit of time to get just one done though. Then it's not gonna be a material intended to spring back either. I may get bored and try it if the wind doesn't let up today so I can see if the carb is in tune. I was hoping, though not expecting, someone would say they knew a source and they were $0.25 each.
|
|
|
Post by spaz12 on Mar 26, 2016 6:02:04 GMT -5
What are those pins even called? If nothing else, I'd like to know for future reference.
|
|
|
Post by spaz12 on Mar 26, 2016 6:24:01 GMT -5
|
|
|
Post by 90GTVert on Mar 26, 2016 6:28:47 GMT -5
Bulb socket terminals? Searching that brought up the closest things I've seen to them, but still nothing quite like them.
EDIT : I'm not sure if these are specific to these bulbs or if they may be used in other sockets. The Venus has a different style of stock headlight, so I may check it and see what it's got. Still wouldn't solve my problem if they are the same, because then I'll need them for the Venus again later anyway.
|
|
|
Post by 90GTVert on Mar 26, 2016 7:59:36 GMT -5
No luck. The Venus socket is nothing like it. I thought maybe a stock tail light socket could use something similar. Only stock tail light in the house is on this Roketa. It's different too.
|
|
|
Post by 90GTVert on Mar 26, 2016 11:45:07 GMT -5
The only thing I could find that was about the right thickness around here was an old piece of a gutter. Didn't seem like a great idea, but I tried it. Got the wire crimped in well. It bent when I was trying to insert the connector and I bent it back. Didn't break, but this stuff sure isn't meant to bend and spring back like a suitable material would. It's a PITA to make and I have no great desire to try again with any material. 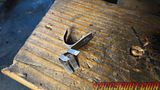
|
|
|
Post by 90GTVert on Mar 26, 2016 21:17:10 GMT -5
The wind calmed down to 5-10MPH in the afternoon, so I finally got a chance to go over the jetting. I started out with a 115 main jet and here's how it went : Jet | MPH/RPM To
| MPH/RPM From
| MPH/RPM Avg
| Max CHT
| 115
| 48.9 / 7350
| 47.9 / 7300
| 48.4 / 7325
| 343F | 120 | 47.6 / 7250
| 47.3 / 7200
| 47.5 / 7225
| 330F | 125 | 47.7 / 7250
| 47.0 / 7200
| 47.4 / 7225
| 311F | 110 | 49.3 / 7450
| 48.4 / 7350
| 48.9 / 7400
| 361F | 105 | 50.5 / 7600
| 49.5 / 7500
| 50.0 / 7550
| 376F | 100 | 48.1 / 7300
| 48.1 / 7300
| 48.1 / 7300
| 386F |
I chose the 105 out of those. If I had one, I would have put in a 107-108. I have a drill set and of course the one that's 106.7 (IIRC) is missing. It was 57-58F with only 45% humidity though, so most weather I ride in should be warmer and with higher humidity and make it run more rich than today. A 109 is what came stock in this scooter. I still had it saved from when it was new. Everyone and their mother says to use a 120-130 main jet with an open filter. 105 does seem small, especially being smaller than even the stock jet, but it clearly works and a 125-130 would obviously be the wrong choice for me. The 125 was starting to cut in and out very mildly so the 130 would probably be pretty bad. Once again, you can see the results you get if you believe in jet recommendations. Once again I say the only way to get the most from your setup is to tune it. Remember those are max speeds each way, not a real average. It still needs work to be suitable for use on 50MPH roads. I ordered a shock from a 2012 Honda CBR250R a couple of weeks ago. I found that it was the same length eye to eye as what I had and used smaller bolts than some bike shocks. At less than $15 including shipping, I couldn't pass it up. I thought I may save the money on buying an aftermarket adjustable shock. I seem to have been blinded by the price and length specs, not noticing how much beefier the CBR shock is. I'm not interested in welding a new mount on and doing a spacer so the bottom can bolt up to this thing. Maybe I'll mod T2 for it one day. Since that failed, I ordered a 300mm adjustable shock from treatland.tv and it showed up today. It definitely feels better with the new shock. It's less bouncy. Messing around while setting the preload, I think I see another part of why the ride on this scoot feels a little strange. The way this engine is mounted, it moves so much that whenever you hit a bump the wheelbase elongates a couple of inches. Still, I think when I can stiffen the front up a little, it will help more and I won't really have much to complain about. I tried to dig into the front the other day, but I need a 12mm allen key for the shock caps and I only had up to 10mm. Top to bottom in the 1st pic : 300mm adjustable, stock, CBR250R 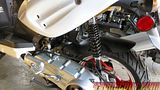
|
|
|
Post by 90GTVert on Mar 28, 2016 16:12:19 GMT -5
My next project is a bit of CVT tuning.  Before any tuning took place, I wanted to clean the entire CVT and check it over. Both halves of the front pulley had grooves at the outermost area of belt travel that I sanded out. 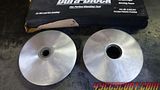 There's definitely room for improvement in the variator, but for now I just installed 12g sliders as a starting point and left it alone otherwise. 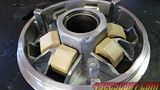 The clutch/rear pulley nut was a pain to remove. I don't have a 41mm socket to use an impact as I normally do. I tried the vice and a strap wrench, but I wasn't so sure the wrench wasn't going to break so I stopped. I moved on to using an adjustable wrench and "tapping" the wrench on a hard surface. I think this thing was over-torqued from the factory. I ended up holding the assembly just above my head and slamming it into the work bench to finally get it moving. Even after it moved, it took ~5 more hits to get it moving with what seemed like more reasonable force. I was previously unaware that roller pins in the torque driver are standard in the GY6, but it's cool with me. 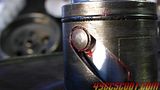 The old belt was 1mm thinner than the new belt, so I swapped it out. 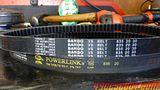 I noticed that there's a big difference in how the belt rides without the fixed half of the front pulley in place squeezing it and how it rides with it. Notice how much farther out it sits in the first pic (no fixed half installed) vs the second. 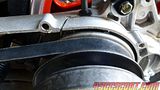 The belt hangs out way past the end of the drive boss in stock form. I added a 1mm spacer, but I was afraid to try more than that because the variator relies on it's aluminum splined section to lock it to the crank so I didn't want to give it too much less contact area. The last pic shows the difference with and without the spacer. Still not near the edge. Variator and fixed half changes could probably free up a little more room for the belt to travel down without having to elongate the boss. 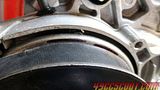 It rained in the morning, then there was a brief period where it was fairly calm and not raining. I got the CVT together, but by the time I took the first test ride the wind was back. There was nearly a 10MPH discrepancy between the to and from speeds because of wind so I called it quits for the time being. I at least got to see that RPM kicked up to over 6500 quickly and didn't change a lot at higher speeds. From watching the tach at other times, I could see that ~6500RPM seems to be where the engine begins pulling a bit harder so if nothing else I should be able to get better acceleration out of it. I think I may take the spacer out of the variator before I try tuning again, then add it in after I figure out what weights work and see what happens.
|
|
|
Post by 90GTVert on Mar 28, 2016 21:19:50 GMT -5
The 12mm allen wrench showed up this afternoon so I worked on the forks tonight. I had 1/2" PVC caps on hand, thinking they'd work. They were a little too large O.D. to fit. I had 2 bushings from a 139QMB stock variator around that are a little under an inch long and fit well so I used those. 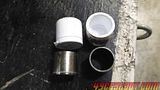 The Ride-On tire sealant/balancer also came in. I forgot about these larger tires needing more and only ordered 8oz. They say 6oz per 130/60-13 tire. I added it to the rear tire and I'll just leave the front alone. The front was only 0.5oz out of balance anyway and tire punctures tend to happen to the rear tire. I rode 5-6 miles to spread the Ride-On around the tire and see how the suspension felt. Increasing preload in the front and using an adjustable rear shock made a big difference. The ride is a little more harsh, but it doesn't feel bouncy, doesn't dive as bad with braking, and doesn't sag as much when I sit down. The Ride-On made the first mile or so bumpy, but by the time I was heading back it felt the same as when the tire was balanced with weights.
|
|
|
Post by 90GTVert on Mar 30, 2016 18:50:20 GMT -5
Today seemed to be the day with the least wind forecasted, so I tried to get some CVT tuning done. I went from 12g to 10g sliders along with the 1000RPM contra spring and didn't really see a change in speed. There were differences in the speeds for each test run, but they didn't follow a real pattern. The wind is kind of screwing that up. I was checking belt travel and it didn't change with any of the sliders. I chose 10.5g (stuffed 3 10s to make 11g) for now. It gets the revs up well for acceleration, but doesn't rev much more than stock at speed. I didn't bother with the clutch springs yet, since it doesn't do too bad starting off. As far as I can tell, this thing is more limited for speed by horsepower than CVT tuning right now. With that in mind, I figured it was a good time to mod the ignition pickup for a few degrees of advance. When I pulled the flywheel off, I saw a 6 pole stator in there. 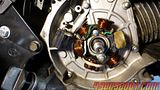 I have an 8 pole and a flywheel for the 8 pole around. The connectors even match up. I've heard that it's a simple swap, but never done it before. Might as well give it a shot. 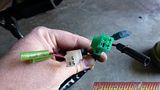 I elongated the holes in the 8 pole's pickup and then installed it and the flywheel. No more difficult than installing a new 6 pole would have been. Till I started it anyway. It fired up and I looked at the headlights. I revved the engine and the bulb got really bright and then blew out. Crap. I thought it must need a different regulator/rectifier. I checked the voltage and it was getting over 50VAC at the headlight connector. I had 4-5 other rectifier/regulators around that look similar so I started trying and testing VAC. Everything was too high until I swapped in a regulator that is marked for a 1PE40QMB. I was seeing only 12V max at the light connection. 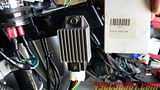 Fired it up and the headlight worked alright so I put it together and took it down the road. It felt slightly better accelerating, but not much help at speed. I came back and the idle was high, I thought just a side effect from the advance. I went to adjust the idle and realized the tail light was out. Should have known it would blow with the headlight. I replaced it and the new bulb didn't light. I tried another and it didn't illuminate either. I then noticed the headlight was really dim. Then I saw that when I first started the engine the headlight was very bright at idle, then it got very dim. Even when it was bright so I thought there should be enough power to light the tail bulb, the best I could get was a faint orange glow. At that point I decided the 8 pole isn't worth it to me at this point. I elongated the mounting holes in the stock 6 pole's pickup and put the stock stuff back on. 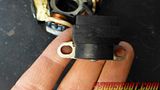 Everything appears to work fine again. So much for a simple swap.
|
|
|
Post by 90GTVert on Apr 1, 2016 13:01:04 GMT -5
With some less than great tuning/riding weather for an underpowered scoot, I thought I might as well dig in a little deeper. I like that the frame stands on it's own with the frame-mounted centerstand, but I think I like it better when the engine has it's own stand. I've had a Hoca HB/A9 cam here for quite a while, waiting till I got the basic tuning done. 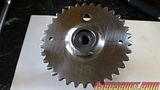 Here's the A9 with the stock cam. 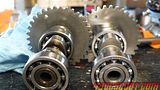 I didn't want to just throw the cam in there. I wanted to do a few checks, so I started by setting up a degree wheel. The piston stop I used on the smaller engines doesn't fit so I had to make a new one. I used a steel bracket from a hardware store. All I had to do was drill two of the existing holes larger and chop one corner off that ran into the cam chain to make it fit. I also added a bolt in the center because the piston crown isn't up high enough to hit the stop. I used some steel tubing to make spacers so I could easily bolt on the stop. 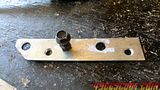 The first thing I did was find true TDC. It was actually very close to the T mark on the flywheel. Maybe a 1/4 of a degree or so off. Here's the degree wheel with the engine's timing marks lined up for TDC. 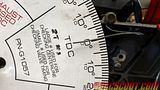 I checked piston to valve clearance with both cams next. I set the valves to 0 lash... no play, but not tight and pushing the valve at rest. The stock cam left about 2.4mm for the intake and 3mm for the exhaust. The Hoca cam left about 2.3mm for the intake and 1.7mm for the exhaust. Even the tightest is basically 3% of stroke, so it should be alright. I know these a big globs of clay, but this stuff wouldn't stick. I was hoping it would stick better with more on the crown. Still had it fall off a couple of times and ended up checking with solder too. 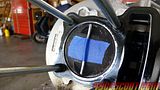 Then I wanted to get some specs for anyone interested. I strapped the engine down to the bench and set up a dial indicator, also strapping the stuff it was standing on down, to keep everything stable. Lift was measured from atop the valve retainers. Lash was again set to 0. 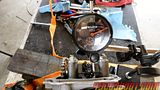 Let me just say that taking lift measurements every 5 degrees of crankshaft rotation, one lobe/valve at a time, is not a lot of fun. It took me about an hour per lobe. My numbers are a little different than what I've seen on other cam charts, but I went back and rechecked my numbers at 0.050" lift that I recorded for opening and closing of each lobe and they appear to be correct. Here's some info for both. 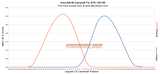 I'm used to specs at 0.050" lift for automotive cams so I noted the points where 0.050" lift occurred and used that for these figures. FWIW, the stock cam was 208°in/217°ex and max lifts were 0.260"in/0.260"ex. The Hoca cam was 229°in/241°ex and max lifts were 0.302"in/0.313"ex. I noticed that the marks on the A9 don't line up so they're parallel with the top of the head as they should at TDC. Setting the degree wheel to 2°ATDC made them line up well. I'm guessing this is poor quality control? If they wanted to build retard into the cam, I'd think they'd do it in the grind, not the pressing of the sprocket. There's already a good bit of retard built in compared to stock, even if everything were advanced 2 degrees. The first pic is the cam with timing right on TDC. Second and third pics are the cam lined up with timing moved slightly.  I looked at the springs at full lift while I was at it. These engines sure don't leave a lot of room between the coils, or mine doesn't anyway. I could get a 0.008" feeler between the intake coils I could reach without much resistance and 0.015" on the exhaust. 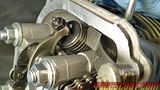
|
|
|
Post by 190mech on Apr 1, 2016 20:14:50 GMT -5
Glad to see a bit of 4poke tech here,looks like the Hoca cam does have some more lift and duration(bet lots of the cheapies dont)..Will be interesting to see the performance increase...
|
|