|
Post by 'O'Verse on Apr 6, 2016 23:23:42 GMT -5
One of the better write ups for sure! Came out clean. That box design sounded raw... didn't it?
|
|
|
Post by 90GTVert on Apr 7, 2016 6:37:45 GMT -5
|
|
|
Post by 90GTVert on Apr 7, 2016 16:40:11 GMT -5
I thought I would go out today and check the fit of the header and muffler and get tabs welded to the muffler to support it using the stock bracket. I should have known it wouldn't be simple. Here's the header as close as it gets with the axle/muffler support bracket in place. Pretty far off.  I thought it must be meant for engines without the bracket, so I took the bracket off just to see. I wouldn't want to leave it off anyway, because of the long axle. Still not close to fitting properly.   Then I figured if I cut the brackets off, it should fit. While I was working on it, I sanded down the chrome a bit or at least roughed it up and I smoothed out the entry at the flange. 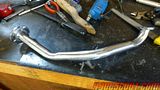 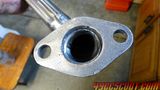 Then it fit, but not at all how I'd need it to. It sat very close to the bracket and it aimed directly at the muffler supports on the bracket. 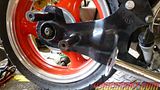 I needed some extra pipe and I didn't have anything lying around that would work, so I cut the stock header apart. The stock pipe is actually 2 pipes. It stays 19mm all the way through, and just looks like it steps up because there's another pipe welded over it. 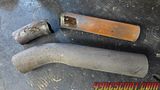 The center pipe is smaller than my aftermarket header and the outer pipe is larger. If the pipe right at the head were replaced and the flange was modified, you could make a header larger than this aftermarket one out of the stock piece. Kinda wish I knew that before I got into this and bought a different header that I made the muffler fit. I cut the newer header in 2 places. In one spot I added a little over an inch from the stock header to make it come out enough that it wouldn't sit so close to the engine. The rear cut was done so I could rotate the pipe and get it to fit. I left my welder set the same way that worked well for the 16GA steel I had been working with and that was a mistake. The header seemed to be the same thickness or close, but I burned through and made a nasty mess on the first weld (I mean nastier than my normal mess lol), then woke up and turned it down. It wasn't going to work out to sit above the 2 supports like the stock muffler did, short of pretty much building a new header out of the 2 headers. I cut one support mount off of the bracket and set it up to hang under the other. It's lower than I would have liked, but hopefully I won't grind the muffler away on the first sharp right turn. Still needs cleanup and some finishing, and I'm not exactly thrilled with it, but at least it does fit now. 
|
|
|
Post by 190mech on Apr 7, 2016 19:06:02 GMT -5
Like my buddy always says about China products,"You are not buying a finished product,you're buying a kit!" 
|
|
|
Post by 49dykon on Apr 7, 2016 19:38:45 GMT -5
Thanks man! Ill try my fabrication skills out and try to get something written up about it maybe alittle different then that one. Hows the pipe sound have you started it up yet?
|
|
|
Post by 90GTVert on Apr 7, 2016 20:04:50 GMT -5
I don't have the new cylinder in yet. Once I do, I'll do some checks and stuff. No rush. They're talking about 40MPH winds and possibly snow Saturday. Windy pretty much every day in the forecast again.  I'll try to post a clip whenever it's making noise.
|
|
|
Post by jkeney on Apr 8, 2016 0:29:22 GMT -5
I just mounted the header pipe to the head and bent it to meet up to be mounted above the stock mount. I did cut one of the two of them off as my new muffler is much shorter. I also cut both header mounts off cause I have the long axle and swing arm set up with a more than adequate support on the muffler mount.
|
|
|
Post by 90GTVert on Apr 8, 2016 14:07:07 GMT -5
Glad I'm not in a hurry. The bore kit arrived in MD yesterday, near Baltimore. Today they sent it an hour and a half west of Baltimore. Problem is, I'm a little over an hour and a half east of Baltimore. Says it will be delivered today, but I have a feeling they mixed up the zip code since mine is 21655 and it's in 21755.
|
|
|
Post by 90GTVert on Apr 8, 2016 18:27:52 GMT -5
I made an adapter for a pressure tester for the exhaust with a piece of aluminum and a hose barb.  I didn't have any kind of rubber plug that would fit the muffler outlet, but I had 1/2" NPT plugs. The hole was a bit large, but I managed to get about 1 thread into it partially. Then I wrapped the plug in tape and sealed around it with silicone and was able to get it to seal.  I found about 8 pinhole leaks, mostly the header. It wasn't that bad, but I had one that I ground and welded and whatnot about 6-7 times and it would always have a pinhole somewhere around it. I tried welding a distance around it, just on it, heavy, light... didn't matter. I could get the tiniest little pinhole that made a fine foam at 5psi, but that's the best I could do. I finally gave up and tried this stuff I bought years ago for securing a brass fitting into an aluminum transmission. Some sort of special solder. That did finally cover it. I never got it to seal and hold pressure because it was leaking from the bolts that go into the muffler. I never worried about it because I could still get 5psi and see leaks. I guess I'll coat them with RTV on install, though I don't know that they'll be a noticeable leak in regular use.
|
|
|
Post by 190mech on Apr 8, 2016 20:10:31 GMT -5
Spent a few hours on this exhaust build eh?Have you kept track of the hours?It takes me 25 to 30 hrs to build a 2T pipe and folks think they are worth $150,guess my time is worth little!Super glad to see you grab the bull by the horns and build a one off system!Should do well as the volume is better than the rest out there,cant wait to hear how it runs!! 
|
|
|
Post by 90GTVert on Apr 8, 2016 20:34:25 GMT -5
This is way easier than a 2T pipe, and I didn't build the header, and I've spent way too much time on it. I liked figuring out how to get the muffler together. Beyond that, not really fun to me. That's kind of how most big metal projects go for me. I lose interest after the hows are figured out and then I just want it done because it aggravates me. I'd rather port, polish, write down numbers... pull out my whiskers one by one.
|
|
|
Post by 90GTVert on Apr 9, 2016 14:46:54 GMT -5
I cleaned up the exhaust today so it doesn't feel like a novel written in braille from the welding BBs. 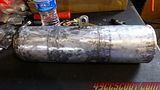 3 coats of BBQ black and it's finally done. Looks pretty much like a stock exhaust. 
|
|
|
Post by 90GTVert on Apr 13, 2016 7:27:59 GMT -5
The 58.5mm (155.36cc) high compression BBK came in Monday. It looked like a good deal for ~$55. 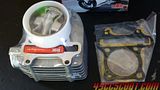 No issues fitting this small upgrade into the cases. 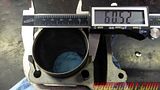 Here are some pics of the old and new pistons. 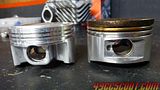 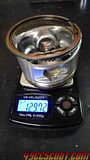 Here's a closer look at the crown. 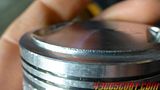 I cc'ed the piston and came up with 3.8cc, using the center raised section as the measuring point. If using the lower portion of the crown around it's perimeter, cc would be +1.1.  There were so many sharp edges on the piston, and I mean some could cut you, that I thought it best to mildly round them off. Far from blending, just at least making them dull. I didn't cc it again, but the material removal was minimal. 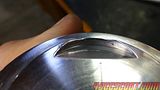 I set the cylinder up to check the piston's position at TDC. After the time sanding the piston, my hand was cramping up and I couldn't get it to cooperate to get the rings in the bore. I've never struggled like that to get a piston in the bore. I grabbed clamp and used it like a ring compressor. It shouldn't be necessary, and wasn't later, but it did work.  Here's the piston at TDC with the supplied base gasket. It sits 0.53mm below deck at it's highest (center) point. 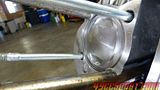 The old cylinder setup was 0.64mm below deck, but it was an essentially flat top piston. Having this piston sitting that low creates a lot of extra trapped volume and I feared it would not be the high compression kit that it was claimed to be. I took the numbers and did the math and if I bolted the kit on as-is out of the box, the high compression BBK would give me a static compression ratio of 8.93:1. Stock was 9.69:1. Nothing can just be easy. I wasn't sure if it was a compression height issue with the piston, or because of the cylinder height/base gasket. I compared the two pistons and the compression height is only about 0.3mm less on the high compression piston than the standard stock piston. The best I could measure, stock is 20.25mm and the 58.5mm piston is 19.95mm. Considering that's from the edge of the crown and the crown does go up 0.8-1.0mm on the high compression piston, the piston is not causing the problem. I never measured it, but that leaves cylinder height or the base gasket thickness as the issue. 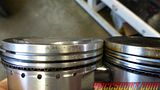 I set the cylinder up without any base gasket to see what would happen. The piston's center peak was then 1.25mm above deck. That would put compression at 11.49:1. Could be pushing it, but I'd try it, if it worked out. 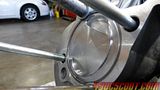 Unfortunately, I have to consider clearances. I took a spring from a hardware store and cut it in half to make checking springs for the valves. These make it easy to push on the valve.  I set up a dial indicator and checked for piston to valve clearance across about a 20 degree range for each valve.  It's sure not gonna work as-is. The intake valve is alright, because the lowest clearance I measured was 0.074" @ 5° ATDC. The exhaust valve, not so much. At 10° BTDC I got only 0.002" clearance. I'm not 100% certain that's all clearance or partially movement of the indicator/engine from pressure trying to push the valve. On each side of that number, I got 0.004" at 5° BTDC and 0.011" @ 15° BTDC. I'd pretty much have to space the cylinder up 1mm (~0.039"-0.040") to be in the realm of acceptable clearance, or cut the valve reliefs deeper. I have no idea what squish clearance is at this point to know what possibilities there are. Another option, possibly alongside other mods would be to advance the cam. I've got plenty of clearance on the intake, it's just the exhaust that's bad. Advancing the cam would close the exhaust valve earlier BTDC and should create clearance. It would open the intake valve earlier and reduce clearance, but there's room to spare on that side. I was tired of fooling with it at that point and came in last night. This makes me wonder how many people bolt on BBKs and go slower or the same speed. I wouldn't think a 5cc increase with a 0.76:1 drop in compression would get you too far.
|
|
|
Post by 190mech on Apr 13, 2016 19:48:29 GMT -5
You could possibly polish that 'turd kit' with a thin base gasket(manila folder) and cutting the valve reliefs deeper.Advancing the cam will hurt the top end revs(which I think extra revs are needed)..We made our own relief cutters with old valves by either epoxy bonding very course sand paper the face and spinning them with a drill motor with the head installed ,or cutting notches in the face of an old valve and doing the above,,We'd try to find the next bigger valve to fab a cutter(1.94 valve,2.02 cutter),maybe there is a better way these days,but we still MUST maintain the proper 'crash' clearance in all 4T motors..2T's have their quirks,but not near as many when stuff starts bending at high revs!!
PS,The new piston is heavier,but its shiny,so that equals 'mo better'!!
PPS,What would you have with a thin base gasket with the stock setup??
|
|
|
Post by oldgeek on Apr 13, 2016 20:18:43 GMT -5
 Glad I just mess with the 2T's!
|
|