|
Post by 90GTVert on Apr 17, 2016 5:50:37 GMT -5
The interesting part is if the valve is almost touching the piston with an A-9 cam and nobody is checking P2V clearance,you'd think the "slap together tuners" would be bending a lot of valves,,Heck,maybe they are!! I did have clearance with the stock cylinder kit and if I was using a base gasket in the BBK I'd be OK. It's just when I decided I wanted more compression that it became a problem. Slap together builds wouldn't likely feature any cc'ing of parts to even realize compression could be dropping with the kit I'm using. Prob just goes together and you either think the kit sucks or you want it to be faster so you think it is. I had the idea last night that maybe the 125cc GY6 heads have less volume and could bump compression, but when I looked up some info, they have smaller valves too. I did some searching in Wiseco and Pro-X catalogs and found a few 58.5mm bore options. One had a 14mm pin, one has a 15mm (like the GY6), and one I can't find info on. No idea on any other specs, like compression height. The one that is a 15mm pin is for a 70s Honda CB550K/CL550F, Wiseco # 40059M05850. The one I'm not sure of is a 1995-2001 Yamaha XJ 600 N or XJ 600 S Diversion. That was in a Pro-X catalog, but no piston kit #. I don't really see it as a sensible option or something I need to do, but I was curious what's out there. The thing is, the CB550K piston is $180. Even assuming it would be a great choice, it would make no sense to spend that kind of money unless you were confined to a specific bore size for some sort of competition maybe.
|
|
|
Post by 190mech on Apr 17, 2016 6:43:17 GMT -5
Here are some piston dimension links,I found nothing in them of your 58.5 bore though.. www.tkrj.co.jp/product/index.htmlwww.mitaka.co.uk/catalogue_index.htmI looked at the CB550 pistons on ebay,some of the used pics show a nice dome.. The XJ600 has a very tall dome and the diversion pic looks a bit flatter... Theres gotta be a link somewhere that has 4T piston dimensions!!
|
|
|
Post by 90GTVert on Apr 17, 2016 8:17:13 GMT -5
Thanks for the links and time to look John.
|
|
|
Post by 90GTVert on Apr 18, 2016 15:27:22 GMT -5
Last time I was waiting on the BBK, USPS sent it to a town with a zip code 1 number off of mine. Now I'm waiting on the piston that was supposed to be here Saturday or today, but they sent it to a different town. They must not like 4T engine parts.
|
|
|
Post by 90GTVert on Apr 19, 2016 5:56:16 GMT -5
I love the efficiency of the postal service. The piston was in a post office about 5 miles from my town's post office. Rather than just send it to the right post office, they send it 20 miles away from the original to a sorting center, then it will go 15 miles back to my post office hopefully. The main route between those two runs right past the correct post office and my house for that matter. I'll probably get it today anyway, but it's weird to watch them work.
Also realized I didn't order a valve with the piston. When I was ordering, I kept thinking I was forgetting something. Saturday, I ordered valves from a place in NJ so hopefully they'll get here quickly. The piston isn't really holding me up anyway because of my blunder. I figured I'd at least have valves around in case I could make a couple of cuts and turn one into a relief cutter. I've seen some attaching steel to a valve to make a cutter, but was hoping the approach of just cutting/grinding part of the face would work. While I have used a rotary tool and stone before, I wasn't cutting anywhere near the depth I need and thinning the piston out so much. I figured it's in my best interest if I have to do that kind of cutting to get the angle right so I don't end up removing any more material than needed.
I only found the standard 23mm ex and 28mm intake valves, I'd like to have 0.050" radial clearance. That would require a valve just over 24mm, which I didn't find. I tried looking at valves available for the 50 too, since they use the same stem diameter and similar lengths, but no luck there either when looking for cheap valves. If I cut that way, I'll probably just use the ex valve the same size and I should be able to do the rest with a rotary tool to get radial clearance.
|
|
|
Post by 90GTVert on Apr 20, 2016 7:06:10 GMT -5
The stock replacement piston showed up late yesterday. It's pretty close to stock, but a little different. The valve pockets are cut different and the compression height is a hair higher on the stock piston. The stock rings are still great, so I planned to use them if I go with this piston. End gap on the 2nd ring is right at the minimum figure I'd use. 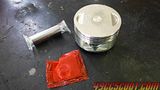 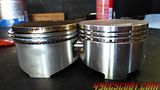 I cc'ed the piston and it's 1.1cc just like the stocker. I installed the cylinder with no base gasket and took some measurements. You won't see a big jump like the BBK, because the stock setup uses a thin base gasket. The piston's highest point, barely raised at all, sits 0.34mm below deck. I probably should have been measuring from the edges with all of these, but I have checked actual squish vs calculating it in most cases and found it easier to measure all pistons from the center. 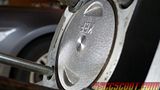 I checked squish and P2V clearances. Minimum squish was 0.050". it could be a few thousands less, because I used grease to hold the solder on the piston and I'm not sure if it stayed all the way to the cylinder wall where it should be tightest, but it was definitely close. The intake valve has 0.095" of clearance, and the exhaust side has 0.047". Static compression ratio with that setup should be 10.10:1. Slightly lower since I would need to do make a little room still in the exhaust valve pocket. That doesn't sound too bad, but I like the idea of a little more compression still because the cam really seems to kill dynamic compression and 10:1 still leaves room for a bit more I think. I may be all wrong and it may knock like hell with any reasonable timing or overheat, since I've never worked with this engine before. I know the small ones have ran higher than that though. I did the math on what would happen without the base gasket as well as having the cylinder milled 0.34mm/0.013" so the piston sat pretty much flush, 0 deck. The head would probably be easier, and possibly something that could be done with sandpaper and glass, but milling the cylinder would reduce trapped volume the most for the biggest gain in compression with the same change in clearances. I'd imagine that would need to go to a machine shop, because I don't know that sandpaper and glass would deal with unlike materials well. That would move compression ratio up to 10.62:1. Going by previous numbers, it should change minimum squish to 0.037" and leave 0.034" and 0.082" exhaust and intake P2V clearances. It wouldn't require so much cutting like the BBK piston would, but it would be about 0.9:1 lower compression ratio than it too. If that were done, I'm not sure I'd do the milling right away. It may be that I put it together at 10.1:1 and have it milled at a later date if all goes well. Not sure. While I was at it, I calculated what it should be like with the BBK and the thin base like the stock bore uses. That would put static compression at 10.95:1 and leave about 0.010"-0.012" P2V clearance on the exhaust side and 0.086" on the intake side. Squish would be 0.050" or more. At this point, I like the compression number from the BBK w/o gasket the best, but it requires deep cuts in the exhaust valve relief. With a gasket, I'd have to remove just over 0.010" less in the relief, but compression drops from 11.49:1 to 10.95:1. The stock setup with milling doesn't sound bad at 10.6:1 with pretty tight squish and less cutting needed for the ex valve. Stock w/o a base is better than what I started with, but I don't think about an 0.4:1 jump in static compression will give me big gains. One thing stock could have going for it is the flat top piston that may offer some slight advantage in flame front and mixture travel. No idea what the difference would be real world. So in short, I still don't know what I'm doing, but I'm still thinking I'll cut the BBK piston and hope it doesn't cause a problem. Good news is that I have a solid backup that will at least run now, if I were so lucky that only a piston failed and didn't take anything else with it. Damn 4Ts take so much effort for small power numbers relative to 2Ts.
|
|
|
Post by cwazywazy on Apr 20, 2016 8:22:14 GMT -5
Yup, I say cut the BBK piston and go without the base gasket. Might as well go all in. 
|
|
|
Post by 90GTVert on Apr 21, 2016 7:20:49 GMT -5
The valves came in yesterday. I ordered both intake and exhaust valves, even though I only need to cut the exhaust side. 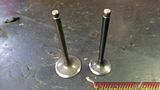 The current exhaust valve is just over 0.900" diameter and I'd like to have 0.050" radial clearance for the valve pocket, so I thought the larger intake valve could come in handy. 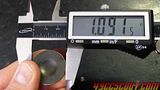 I put the intake valve into a drill and spun it against a grinder to take off about 0.090" and make it roughly 0.100" larger than the exhaust valve, which should give me the 0.050" radial clearance. 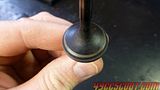 Then I put the valve in a vice and made some cuts to hopefully turn it into a cutter. Pretty random, because I wasn't really sure what I wanted/needed. 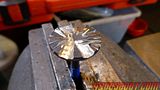 I set the BBK up and rotated it to the point of least P2V clearance on the exhaust side and then taped the whole bore, other than around the valve relief, to keep debris out. 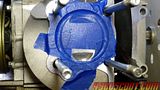 I put the cutting valve in place of the exhaust valve, with some oil on the stem, and installed the head. Neither of my drills would fit into the head, but luckily I had a drill bit extension around that uses a set screw and secured the valve in it. Long, but it works. 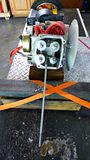 I then started cutting and checking and cutting and checking and cutting and checking. You can see that it's way off of where the valve reliefs are. After I got a bit of depth, I checked P2V clearance and I was only at 0.022", which is pretty much where I figured it would be by trying to match up feeler gauges to the pocket. 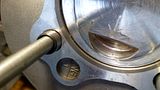 I've been careful to make sure I never spin the valve/cutter while it's on the valve seat. Even if it were the proper valve to fit, there's debris in there and I don't want to damage the seat. Also, I use a shop vac before each disassembly to reduce the risk of whatever debris may be in there from ending up in the cam chain passage. I kept cutting and it seemed to go much slower after the first few times. I cut some more area out of the valve, hoping it may be more aggressive with less contact area on the face. Didn't seem to make much difference. 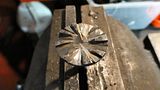 I'm currently at 0.033" minimum clearance. With as slow as it's cutting now, I'll be all day. I'm going to see if I can sharpen the edges with a file or something. I've seen people using sandpaper stuck to valves and I thought that would be way slower, but I think that would have been faster than what I've done so far. Oh well, some progress anyway.
|
|
|
Post by 90GTVert on Apr 21, 2016 10:14:51 GMT -5
Using a file on the cutter would take nearly forever, so I attacked it with the cutoff disc again. The old profile seemed pretty tame with boxy peaks. I tried to make them more triangular so the leading edge is the highest point and then it tapers off. It's ugly, but maybe this will speed it up. 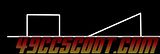
|
|
|
Post by 190mech on Apr 21, 2016 12:05:26 GMT -5
Now youre talkin'!I always try to angle the cutoff wheel to have a negative rake so the cutter will tend to dig in,,keep at it and use some lube so the cutter doesnt get clogged.. 
|
|
|
Post by 90GTVert on Apr 21, 2016 12:13:34 GMT -5
Oh, that worked alright. I had been cutting for about a minute at a time before, and seeing hardly any change. I loaded the fresh cut valve up and in about 10-15 seconds I stopped because it felt way different than before. I pulled it out and it had cut what I feared was too much already. 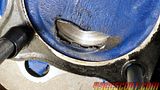 I checked P2V clearance and the minimum on exhaust is now 0.084". I had planned to stop at about 0.070" to stay a little more safe on the crown thickness, but it's too late for that now. At least since the valve is so far misaligned, it didn't cut from the deepest point of the factory relief, so that should give me a tiny bit more thickness. If you make a cutter like the finished product, easy on the pressure and you better check it very frequently! I cleaned up the sharp edges a bit. 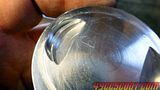 Then I cc'd the piston again. I'm going to recheck it later, because it seems like too much change. This pocket added 1.3cc, and that seems like too much. Maybe I didn't get it sealed around the piston all the way and some leaked. I had been checking twice to be sure I got the same results, but I only did this once quickly. If that's right, this relief dropped compression all the way from 11.49:1 to 10.51:1. Sounds a bit far off.
|
|
|
Post by 90GTVert on Apr 21, 2016 16:11:16 GMT -5
I checked the piston crown twice more. These times it came up as 1.2cc more, instead of 1.3cc like last time. Doesn't make much difference. It comes out to 10.57:1 that way. It's a shame the valve reliefs didn't line up so I have this double cut. Oh well, at least it still ended up 0.9:1 above stock and higher than I would have got even milling the stock cylinder after the stock piston was cut.
I put the top end together with ThreeBond at the base. From what I've seen, people use a different formula for 4T gaskets, but it's worked for me on 2Ts and gearboxes.
|
|
|
Post by 90GTVert on Apr 22, 2016 14:20:13 GMT -5
I got the engine back together and installed. There have been multiple changes since it last ran, so I'll start with the exhaust since I have pics and video for that one. Here it is bolted up and I made a video revving and WOT on the road. I think it sounds better in person. It doesn't get the deep thump that the boxy chambered muffler I built long ago had, but it sounds OK. I'm not sure I like the loud exhaust, but I'm not sure that I don't either. lol I like listening to it at idle or free revving, I feel like it draws a lot of attention since I have to be WOT or near it to ride this thing like a motorcycle though. 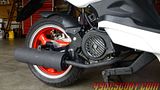 And it's me, so you know something had to break. I noticed a rattle when braking and realized the bracket for the muffler support had broke in half. On closer inspection, it looks like the header makes the muffler want to sit farther in, toward the wheel, so I suppose it broke from the stress of that. It wasn't tough to install and I didn't have to force anything, but then I did just use the bolt to tighten the bracket. I may have clocked the header wrong on install. It will swivel quite a bit, so I tightened it down all the way inward and I don't know that I had it like that when I welded everything up. I'll have to redo it and probably need to swivel the header out a little when installed, because it's pushing the muffler all the way up against the bracket for the rear wheel. So there's fail number one. 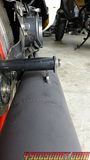 I'll move on to the dual headlight mod next. One filament is out on one bulb, and it seems like when I switch them I have one high filament and one low on at the same time. I set them up so both high and both low beam wires were connected to the same sides on their respective bulbs, so that seems a little strange. The headlight connections will need a little rearranging. No idea if they'll be bright enough or not yet. I swapped out the old stock brake hose for a braided stainless hose and replaced the stock master cylinder a little while ago as well. This was a success. The front brake feels much better. I do believe it's the best brake feel that I have had on any of these scoots. I'm not saying it's got a ton of stopping power, after all it's a stock brake system, but it feels smooth when applied. I may just be over-reacting because the front brake was jerky before and felt rather unsafe. I don't think so though, because I have rode T2 lately and it has basically the same brake system and a recently swapped master cylinder and it doesn't feel this good. The front tire was flat. I have noticed it a few pounds low here and there, but never thought too much of it. I pumped it up over 40psi before I rode the scoot and it was still up when I returned home, but I definitely need to find out why it's losing air so I'll have to get some soapy water out and spray the tire and valve stem down. The other change that we've focused on a lot lately in this thread is engine work. It's went from 150 to 155cc, increased compression from 9.69:1 to 10.57:1, had a Hoca A9 cam installed, and received mild port work. I put a 115 main jet in to start with, 10 up from the 105 that I found to work best before all of this. I went for a little over a 20 mile ride to break it in and to get the clips for the exhaust video somewhere remote enough that I figured no one would steal my camera sitting on the side of the road. Unfortunately, it's windy today so it was hard to really tell what's what. There's a little more power there, but not a whole lot. At one point there was a side wind pushing me hard enough that I was leaning into it and I got to about 54MPH before I let off for bad bumps in the road ahead (this was after I knew the exhaust was busted). I doubt it had much more in it than that. It's not in tune, so I don't know how much difference that will make, but expect no miracles. According to the forecast I last watched, I've got 5 more windy days at least. Whenever there's a break from wind, I'll try to tune the carb. I saw a max of 407F CHT, which I think is the highest I've seen. One bit of good news is that I never heard any spark knock, so at least the elevated static compression doesn't appear to be causing any trouble. I did an oil change pre-start, and I'll do another before the next ride. It's only been 20 miles, but I like to change it at a short interval with new parts in place.
|
|
|
Post by 190mech on Apr 22, 2016 17:15:34 GMT -5
Sounds real good!The heat in the header may have caused the muffler to move inward.A wider triangular bracket may be needed as well as a second support elsewhere to make it reliable..As you well know Ive had mounting problems more than once with my pipe builds... 
|
|
|
Post by 90GTVert on Apr 22, 2016 18:31:43 GMT -5
I changed the oil. Then I replaced one headlight bulb that had a bad filament. I realized the bulbs were just clocked wrong relative to each other, making it look like one was on high while one was on low. Then I checked out the wheel and tire and found the issue. The schrader valve was leaking. Replaced it and the leak is gone. 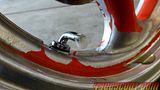
|
|