|
Post by chadbullet on Jan 1, 2024 17:39:36 GMT -5
I've been looking into measuring port timing and received a motion pro degree wheel for christmas. It is drilled for m6 in the center. I would like to mount in on the end of the crank of my Honda af16 engine which is m10x1.25. I thought I had a pretty good solution figured out. 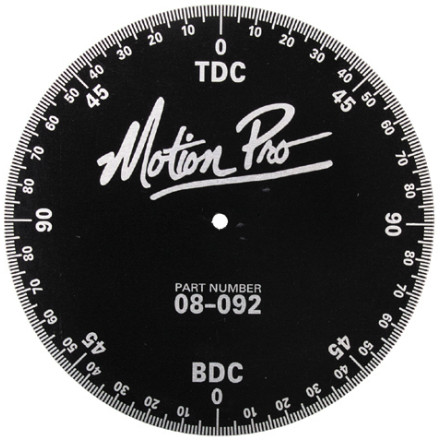 I found these on amazon... www.amazon.com/dp/B0C4VBD2GJ?psc=1&ref=ppx_yo2ov_dt_b_product_details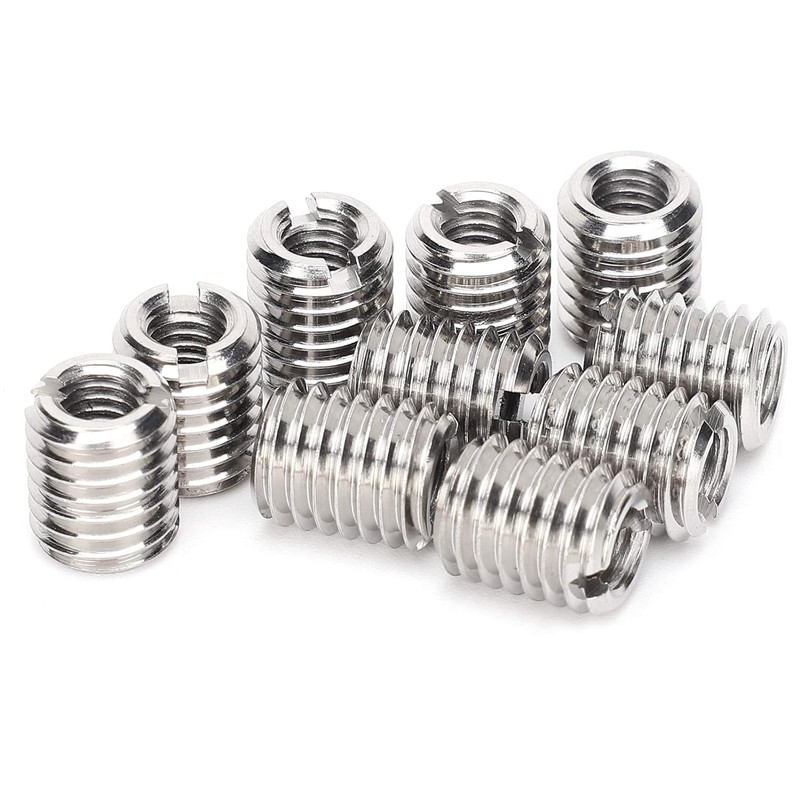 Basically I would use an m6 bolt to thread into the adapter and then use an m10x1.25 coupling nut to adapt to the crankshaft. Well, unfortunately the adapters I received are actually m6x1.0 female to m10x1.5 male. I believe the listing is just wrong, rather than that I just received the wrong item. I cannot find any source of m6 to m10x1.25 adapters. Does anyone else have any other ideas on how to mount this degree wheel to my crankshaft? I'd rather not try and drill it out any larger.
|
|
|
Post by oldgeek on Jan 1, 2024 18:23:15 GMT -5
I dont know if it will mount on either side without some sort of adaptor that adds length?
|
|
|
Post by chadbullet on Jan 1, 2024 19:25:01 GMT -5
I dont know if it will mount on either side without some sort of adaptor that adds length? if the m6x1.0 female to m10x1.25 male adapters I ordered had been the correct threading, I intended to use a threaded coupler that would be cut to length needed. Instead I'm left scratching my head. 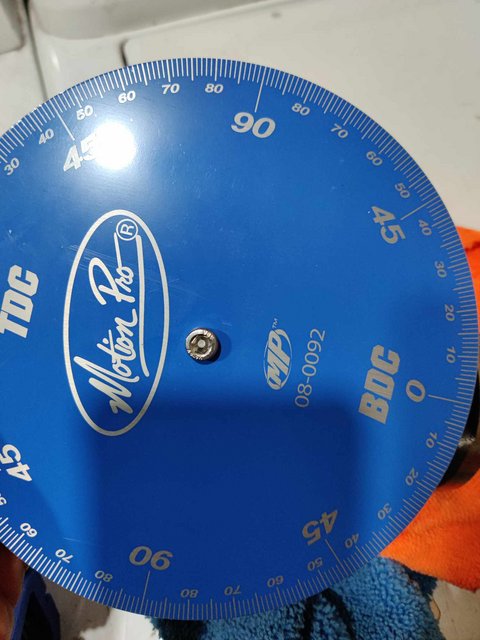 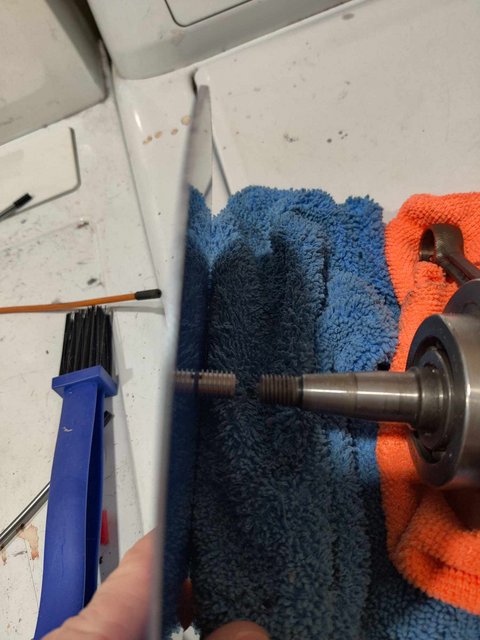 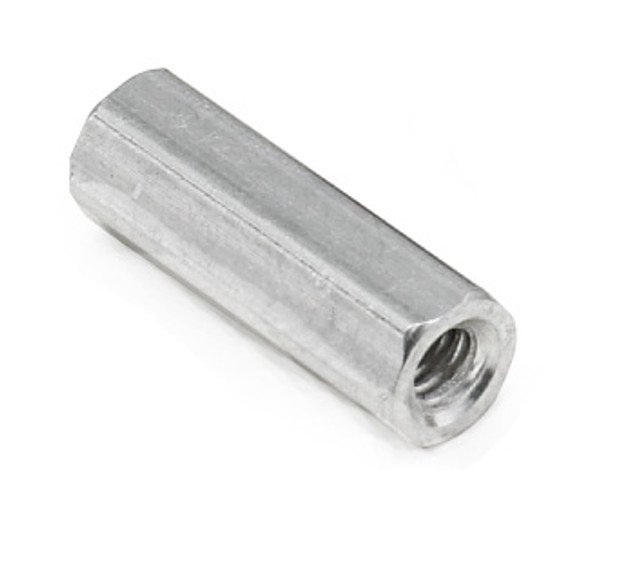
|
|
|
Post by 90GTVert on Jan 5, 2024 8:38:19 GMT -5
It would be easier with a lathe, but you can make your own adapter with drilling and tapping.
Get a piece of round bar. I'd use aluminum for easier working and it doesn't need to have a lot of torque applied to it anyway for this job.
Cut it as square as you can on both ends. Sand, file... whatever to get it straight. McMaster-Carr has 3" pieces of 1" 6061 for ~$5.50 as an alternative example, but you'd have to pay shipping.
Drill and tap one end to M10x1.25 and the other to M6x1.0.
You can grind flat spots opposite each other on the rod if desired to be able to get a wrench on it or start with hex bar.
|
|
|
Post by FrankenMech on Jan 5, 2024 21:23:12 GMT -5
I would just use a step bit and drill out the degree wheel.
|
|
|
Post by 90GTVert on Jan 7, 2024 13:45:11 GMT -5
I would just use a step bit and drill out the degree wheel. That was my first thought as well, but if it needs to be spaced out the adapter could work as the spacer.... I guess so could a coupling nut if it's long enough. It could be good to preserve the smaller hole if the wheel were used in other applications... but for scoots it's unlikely that you'll be putting it on a crankshaft smaller than 10mm. I use custom spacers to remove slop in the mounting if the center hole is too big, but then you may actually need a lathe for those.
|
|
sinfull
Scoot Enthusiast
 
Posts: 413
|
Post by sinfull on Jan 7, 2024 17:17:36 GMT -5
If you don't want to mess up the center hole, then just make a backing plate for the crank shaft, and bolt the degree wheel to it. 4 small bolts to the backing plate and keep the center hole. No machine necessary except drill and tap back plate for crank and attach the wheel to the back plate via a couple small bolts. Piece of flat steel and a angle grinder cut off disc , cut to shape, drill and tap for crank and attach wheel with small bolt pattern and you are good to go
|
|
|
Post by FrankenMech on Jan 7, 2024 22:48:01 GMT -5
Degree wheels are cheap, anywhere from $12-25 and printable pdf files can be had for free. It is not worth messing around with something you will only use once or twice in a lifetime unless you make a living out of building engines. Just drill out the center hole to the size needed and hang it on a nail on the shop wall when done to gather dust...
|
|
|
Post by Lucass2T on Jan 8, 2024 1:15:49 GMT -5
Degree wheels are cheap, anywhere from $12-25 and printable pdf files can be had for free. It is not worth messing around with something you will only use once or twice in a lifetime unless you make a living out of building engines. Just drill out the center hole to the size needed and hang it on a nail on the shop wall when done to gather dust... I made mine by printing one and glueing to an old record. It's basically free. I could JB weld a crank nut to the backside so I can screw it on the crank.
|
|
|
Post by FrankenMech on Jan 8, 2024 13:04:40 GMT -5
Use a piston stop threaded into the spark plug hole to find TDC. Then adjust the position of the degree wheel as needed for TDC. There are lots of explanations and video's on using piston stops to find TDC so I will not explain the process here. Google "finding tdc with piston stop".
Remember to mark TDC on the case for future reference for that particular crank etc. China made parts can 'vary' in quality and TDC for your particular set of parts can vary because of it.
|
|