|
Post by oldgeek on Jun 7, 2015 21:40:46 GMT -5
It seems likely to me that the wheel would spin ok on the stand, but when drive pressure is applied, things may shift and bind?
|
|
|
Post by 90GTVert on Jun 7, 2015 21:48:21 GMT -5
I prob should check that out. I don't think I paid it much mind. I guess it would have to be enlarged and sleeved if it were really bad.
|
|
|
Post by oldgeek on Jun 7, 2015 21:50:20 GMT -5
Yeah, that is what I was thinking could be done to fix that if needed. Could put a nice bronze bushing in there.
|
|
|
Post by thatcrazyguy on Jun 8, 2015 7:22:24 GMT -5
Inspiration in a thread:)
|
|
|
Post by 90GTVert on Jun 9, 2015 12:44:19 GMT -5
I took the gearbox apart today. First noticed grey gear oil with under 100 miles on it. Never a good sign. Once I drained the gear oil I put the drain plug back and it stripped the case. The threads have felt tight for a bit so I assumed this was coming sooner or later. 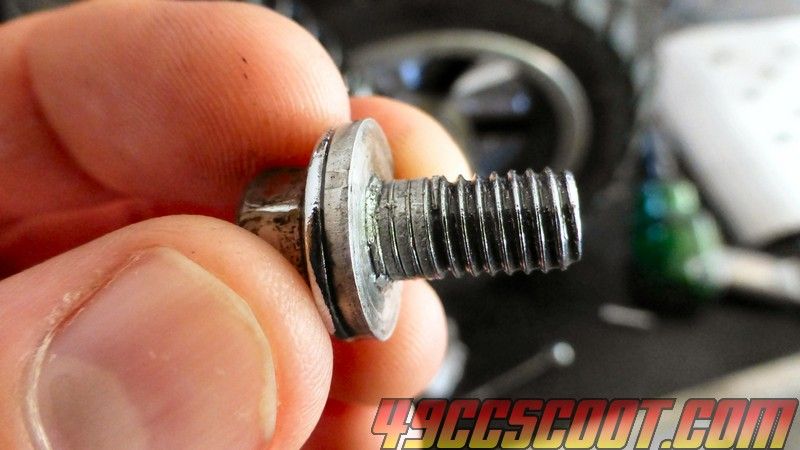  The countershaft didn't look too bad.  The receiver or bushing or whatever for it didn't look too good. The pics make it look worse than it looks or feels, but there is roughness there that can be easily felt running a small screwdriver over the surface. This also is the spot where dark residue seems to be coming from. Nice catch oldgeek. 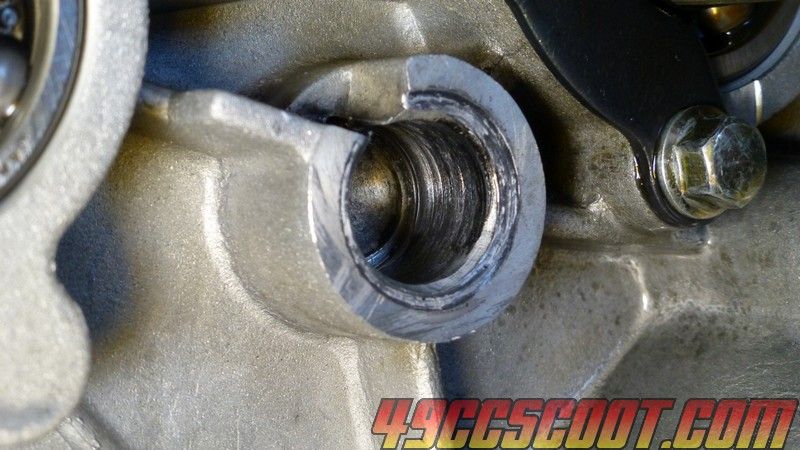 So then I wanted to figure out some measurements so I could look for a bushing. I used a micrometer and a snap gauge for the most part. 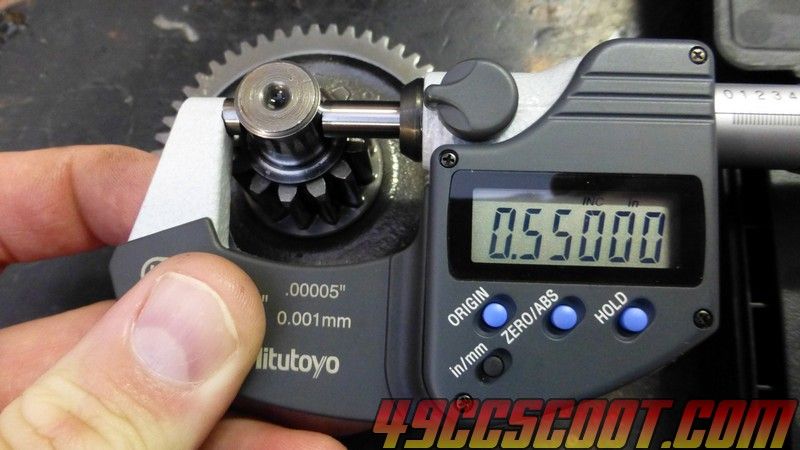 (This is a different case.) 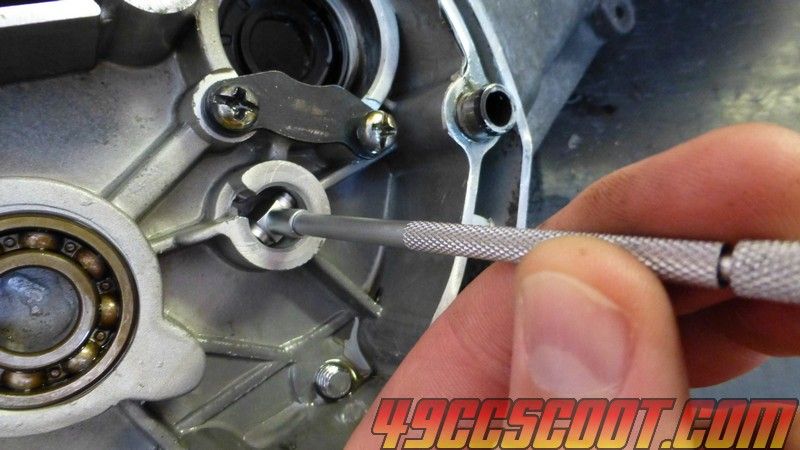 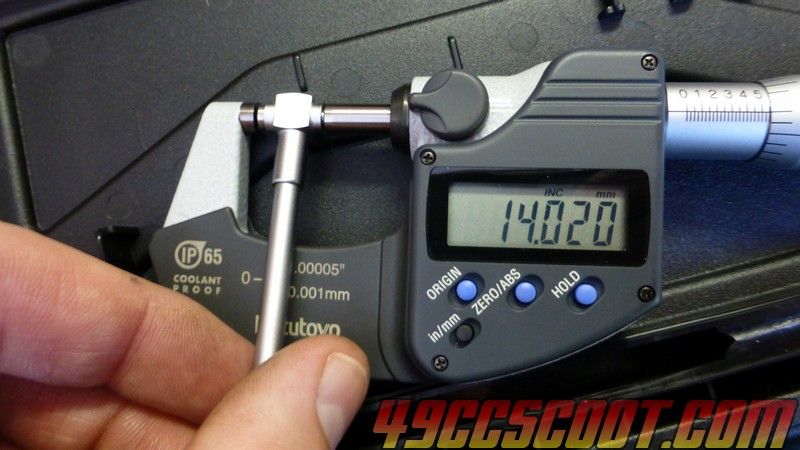 Countershafts (CS)
| Current CS
| CS From Fail
| Different CS
| O.D.
| 0.548"/13.92mm
| 0.548"/13.92mm
| 0.550"/13.97mm
|
Cases (Smallest point, both out of round some)
| Current Case
| Different Case
| I.D.
| 0.554"/14.07mm
| 0.552"/14.02mm
|
So it looks like my current clearance is about 0.006". Tightest clearance of all of the numbers would be about 0.002". I figured I should either shoot for 0.002" with a new bushing, or try to size the bushing as close as possible to the smallest case I measured at 0.552"/14.02mm. The case measures about 13.5-13.75mm deep where the countershaft rides. The O.D. of the case there is 24.23mm, roughly 5mm wall thickness. 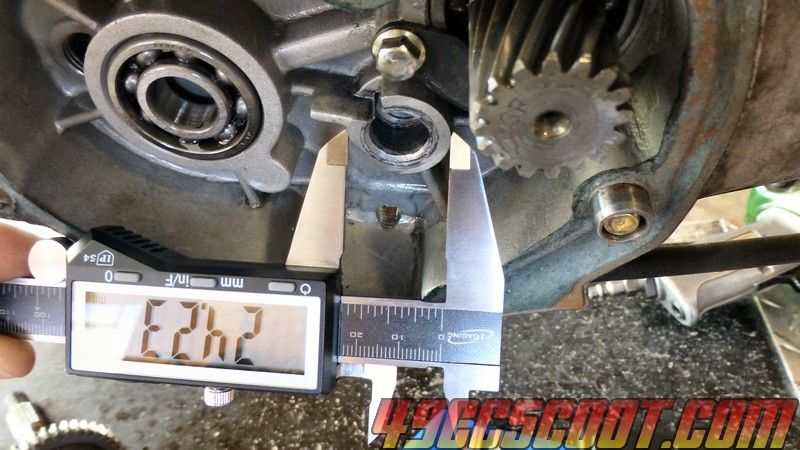 I went on McMaster-Carr to see what I could find. I don't see measurements of the bushings ID, but rather the OD of the shaft they are intended for. 14mm is the closest shaft diameter I see. My countershafts are 0.03-0.08mm/0.001-0.003" shy of that. Sounds reasonable to me. Plugging in the depth, the closest things I see are : Part #7811K21 For 14mm Shaft, 18mm OD, 14mm Long $3.41 Part #7811K24 For 14mm Shaft, 20mm OD, 14mm Long $3.98 I think I'd be much better off with the 18mm OD, leaving about 3mm wall thickness. Hopefully that's enough that I don't end up cracking a case. Both are bronze sleeve bearings in "Alloy 932". They also have them in oil impregnated versions "SAE 841". The 932 is good to 450F. 841 only up to 220F. 932 sounds better suited to me and it will be lubed by gear oil hopefully. It'll prob be fun trying to drill the case to accept the bushing without going too large or crooked. I haven't decided if I'll repair the drain plug at the same size yet or a different one. I'd like to go magnetic, but may not ATM. The M8x1.25mm drain plug I looked at was almost $20. If I see one in a similar size for closer to $10, I may switch. Looks like no car show this weekend most likely.
|
|
Deleted
Deleted Member
Posts: 0
|
Post by Deleted on Jun 9, 2015 13:50:17 GMT -5
"snap gauge"; looks like a very handy tool to have. never seen one before...learn something new here every day. You guys and your abilities in ad hoc, Zen Engineering are amazing. Give you a McMaster-Carr catalog, a busted engine, and stand back!
(Threadjack off)
|
|
|
Post by 90GTVert on Jun 9, 2015 13:56:47 GMT -5
You can get a set of snap gauges cheap. Mine are from Harbor Freight IIRC. They call them telescoping gauges, which I think is the proper name, and they cost about $15. I was worried that maybe they wouldn't hold since they're cheap. They're spring loaded and when you want to lock them in you twist the end so the gauge holds the measurement/position. I haven't had any issues with them though.
|
|
|
Post by 190mech on Jun 9, 2015 14:21:03 GMT -5
Youll need to find a drill bit smaller than 18mm,maybe 11/16" or so to open the hole,then preferably use a 18mm reamer to finish it..A drill press with the case well supported should work.I'd do a 'test run' on a scrap piece of aluminum before doing the real thing!
|
|
|
Post by 90GTVert on Jun 9, 2015 14:33:32 GMT -5
Thanks John. I planned on drilling small, but wasn't exactly sure what course I'd take from there. Looked up reamers and what I see is about $50 and up unless I wait about a month for a hand reamer from China. My father works at a hardware store so I'll ask him if he can get one from any of their suppliers. Sometimes stuff is much cheaper, sometimes I can get it online cheaper.
|
|
|
Post by 90GTVert on Jun 9, 2015 14:45:05 GMT -5
There's an M8x1.25 magnetic drain plug on eBay from Taiwan for $7 right now, if I want to wait till July sometime to get it. I decided to just order 10 small magnets for $5. I'll see if I can make my own magnetic plug out of an existing one. If it works, for $5 I'll have enough to do one for every engine I have and more.
|
|
|
Post by oldgeek on Jun 9, 2015 18:29:47 GMT -5
Brent, could you drill completely through the case if necessary? Then you could bring it to size with simple tools like a round file. Then use some type of rubber plug to seal the hole, or even a threaded pipe plug.
You have quite a challenge before you. Good Luck!
|
|
|
Post by 90GTVert on Jun 9, 2015 22:54:55 GMT -5
Prob could be done with a threaded plug to seal it securely without much worry in the future. I would think the reamer would give a more true bore. I may look into adjustable reamers. Didn't even check the prices earlier because I assume they're high, but if they aren't terrible it may be a tool I would have more use for someday. I Time-Serted the drain plug hole, cleaned the aluminum out of the bolt's threads, and ran a chase over the bolt just to be sure it was good. 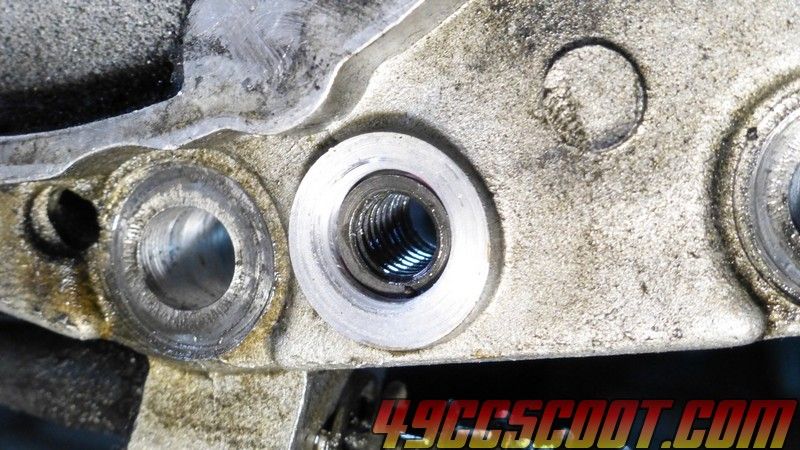 I can't seem to stop taking engines in and out of scooters lately. 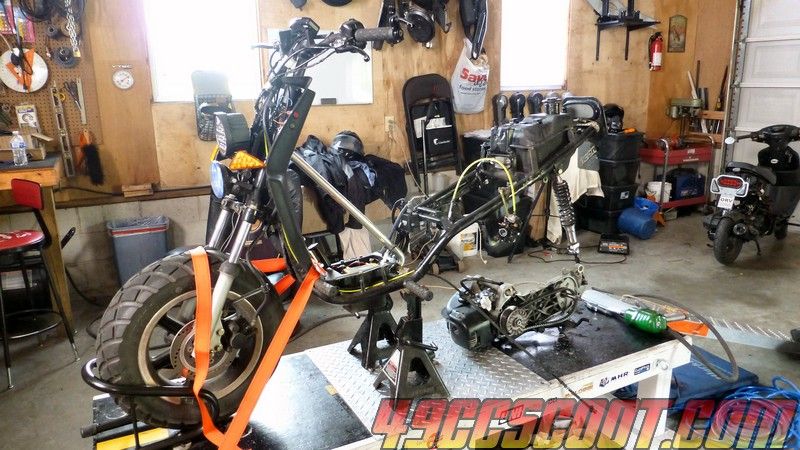 T1's engine, the 103cc that was good for 70MPH with a Peace Pipe, was just sitting around. I stuck a degree wheel on it. I didn't zero the wheel or scrutinize port opening and closing. Just quick numbers. I'm not even sure why I bothered, I know it's too aggressive to stick a PG pipe on and putt around. 198 exhaust, 137 transfer.  You can tell I seized this one more than once. 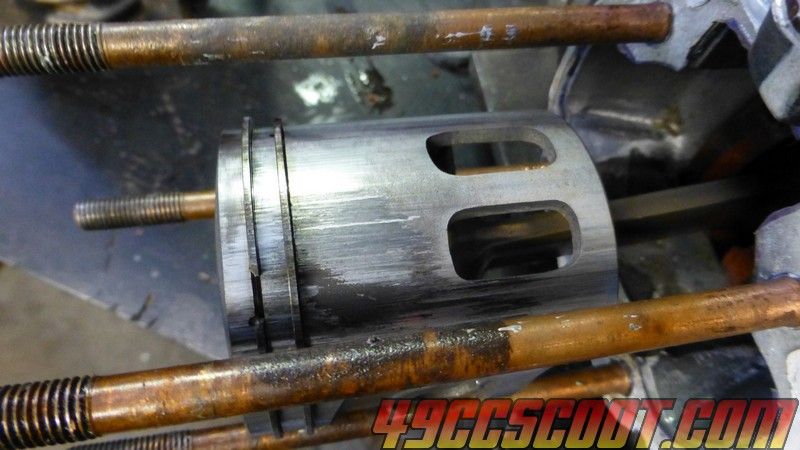 The crank is brown from sitting so long. I did squirt some oil in there when I stole the VFORCE reeds from it not long ago, but otherwise I've paid no attention to it. This one has ceramic bearings on the crank so my main concern was the rod, but everything is smooth and quiet without excessive play or resistance. 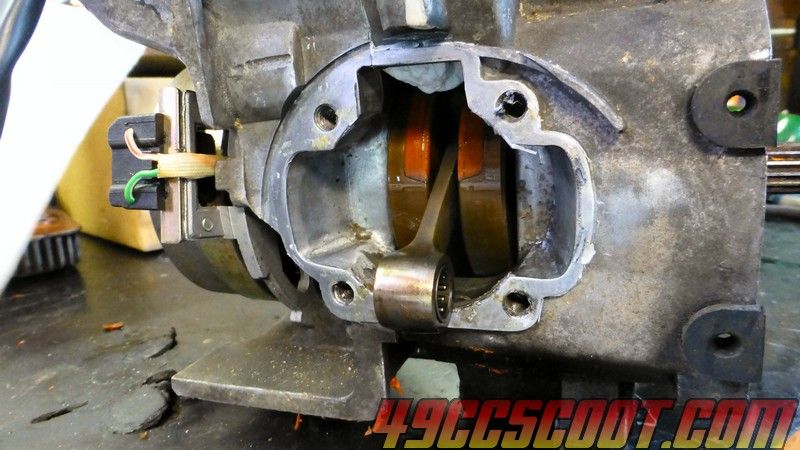 I still have the old 54mm Hoca standard cylinder sitting here. I think piston to wall clearance is a bit more than it should be, but it should be usable. I used the Malossi reeds and a spacer and I had a spare stock intake. I had to open the intake up for the 21mm carb. Cut some new gaskets and got it together not long ago. If I'm lucky it'll pass a pressure test sometime tomorrow. I'll prob go with a stock or Hoca TD and a Hoca variator. The only things I'll be taking form the 103cc that I was using are gears. Two 103s. 
|
|
|
Post by 90GTVert on Jun 10, 2015 11:49:14 GMT -5
I ordered these yesterday at about 1PM standard shipping from McMaster-Carr. Showed up about 15 minutes ago. I prob should have just ordered the reamer there and I could have been working on it. Didn't expect it quite that quick. 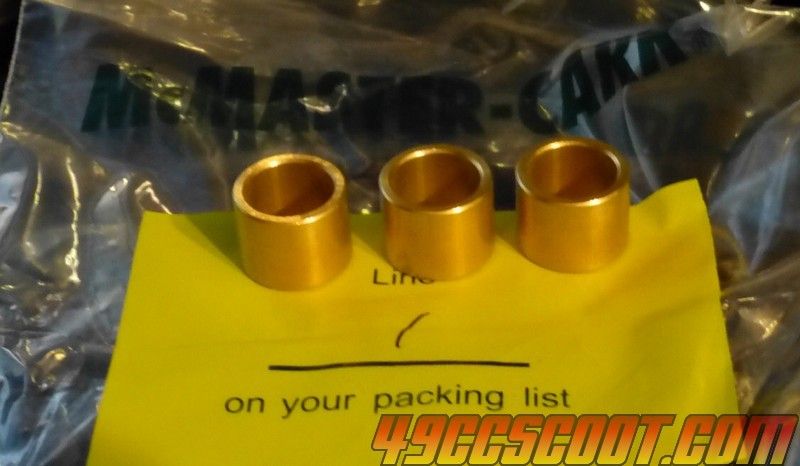
|
|
|
Post by 90GTVert on Jun 10, 2015 15:52:50 GMT -5
I checked the bushings out. Here's a little info in case it's of use. Again McMaster-Carr part # 7811K21. OD : 0.711" / 18.07mm ID : 0.551" / 14.01mm Length : 0.552" / 14.01mm 18.0mm = 0.709" so it looks like an 0.002" interference fit if I actually end up with an 18mm hole. Sounds reasonable enough to me. I wonder if I'll ever get it out if I need to? I guess at this point just get it to work and hope it's good to go. Nice fit with the countershaft. Not sloppy like the case, but not tight either. 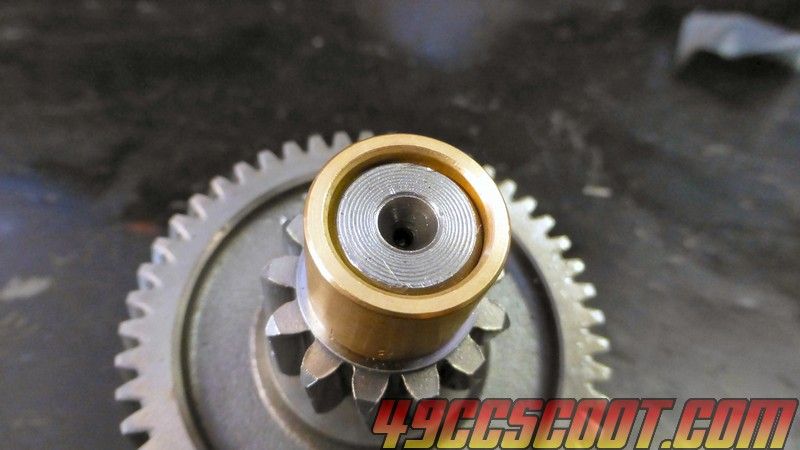 My father asked me for a pic of what I wanted, since I asked about a reamer. I guess adjustable is out. What I came across all have ends that wouldn't allow the cut all the way in unless I drilled all the way through the case as Scott suggested. I did the pressure test on the other 103 and failed. It had a small leak at the corner near the boost port on the base gasket. Took it back apart, cleaned everything, cut a new gasket, chased threads again, and reassembled. Crossing fingers and toes that it seals this time. I did check squish before it came back apart, just to make sure it's in the ballpark. Narrowest clearance I saw was 0.82mm, which isn't far off of what it was on the other engine. Should be fine even after the base gasket compresses after a re-torque (assuming it seals).
|
|
|
Post by oldgeek on Jun 10, 2015 16:11:36 GMT -5
I would not sweat a tight press fit in the case, I think loctite would fix any looseness of the bearing to the case. Then again you could always use the hot/cold trick to get it into a real tight hole.
Any idea what RPM's that shaft sees?
|
|