|
Post by 90GTVert on Jul 9, 2020 11:13:23 GMT -5
After looking it over, I think I'm gonna have to (or would prefer to now) make the crank adapter as a nut. The bolt pattern for the fan/pump drive bolts on the rotor is pretty big. There are M5 (looks like it, haven't checked) threaded holes tighter to center. Even those would need a chunk of steel rod 2" or just under. Don't have that on hand, not cheap, tougher to work with in the mini-lathe. LOTS of material removed to take it down to 5/16" for the pulley mount.
I considered making it in 2 pieces. I could cut a round plate on the lathe. Then cut the rest and weld them together. That leaves me open to failed welds (I think I'd be fine for this piece), but more importantly a part that's not totally true and that would be a big deal at 14,000RPM. I guess both parts could be left with a little excess and machined after welding to keep them true. I'm sure someone better than me could do it no sweat, but I'm trying to be realistic here and not go overboard with work when maybe the nut will be fine.
I've got rough dimensions for the nut worked out. The thing is gonna be 2.2" long overall to start. That seems ridiculous. I am leaving room to cut the shaft end down. You know, you can cut it down but it's tough to add it on later. 0.4" deep to go into the center of the rotor, 0.55" of hex area, so that's nearly an inch. Then the mounting shaft section, for a pulley that's (IIRC without the paper) ~0.8" thick. The adapter will have to be bored in about 0.7" so the crank fits in there, plus of course threaded. I'm slow on the lathe, plus there's likely to be a lot of test fitting and humming and hawing so this will keep me busy for a while.
|
|
|
Post by 90GTVert on Jul 9, 2020 16:38:15 GMT -5
This is definitely going to keep me busy. I just got the crank end done. Started the tap on the lathe. Took it off and finished it by hand. Threads looked great to me. Went to thread it onto the crank and it looked a little wonky. Wasted that time and material. I guess I'll start all over again tomorrow. If I screw that one up too I'll be ordering more hex stock.
I did the same thing with the direct drive adapters for the stock water pump project. The worst part is that I don't know what I did different from the straight ones to the crooked ones. I get a couple of threads in on the lathe (work in the chuck, tap in the tailstock) so I'd figure it's straight. That's by hand turning the lathe. It gets very hard to turn by hand so I switch to the piece in a vise and using a T handle to finish.
I can't thread with the lathe and I can't thread straight without it. These are the times that I start to truly believe that I'm just too damn dumb to do anything right. I come in just now so I can get cleaned up and start on dinner and my father says he never had any trouble threading. I told him to try threading a piece that's machined true otherwise and rotates. If it's off at all you will see it or if you miss that you'll feel it when it spins up. It's different than re-threading something that was stripped where you'll just toss a bolt in. As long as the bolt fits and goes through whatever it's for, you don't need to worry if it's true. That's not how it works when you're attaching it to the crank and spinning it at high speed.
|
|
|
Post by 190mech on Jul 9, 2020 17:20:35 GMT -5
I ran into that problem years ago when a buddy wanted to make a bunch of prop adapters for big RC aircraft using string trimmer engines..very few would run true without super careful setup..I think for your application the bolt on flange setup would work out better,maybe a built up scheme like this; 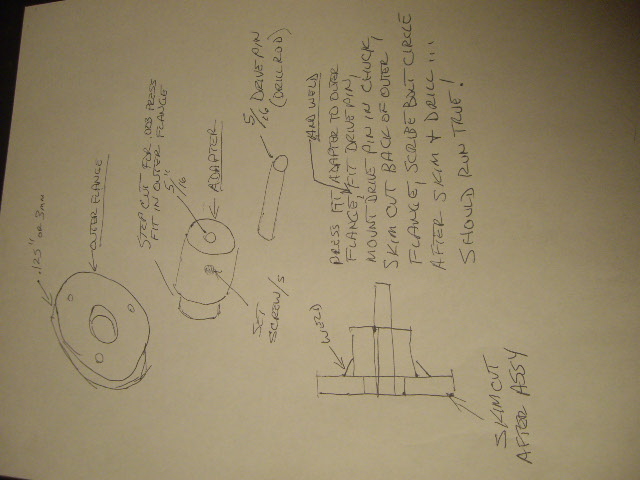 Will be glad to help with this project!
|
|
|
Post by pitobread on Jul 10, 2020 9:47:50 GMT -5
Hey Man, Keep at it. You aren't dumb! I teach a lot of apprentices and it just comes down to experience.
Here is my approach.
Tapping is not really a precise thing, I mean it is and it isn't.
I would make myself a spring center, or buy one. It is a tool that goes in the tailstock that allows you to load up on a tap and keep it centered the whole time, you can do this manually by continually moving the quill out after every turn.
With a Taper tap(which is what 90% of home shops have at their disposal) you can still easily go crooked after a few threads, this is because on a taper tap, you really are not hitting full thread depth untill your at least 6 threads deep in most cases. because the snout of the tap is relieved heavily to allow for easier cutting and almost a reaming action, you can for sure get a few threads started then due to uneven pressure on the tap handle get it going crooked.
SO all that said, here is what I would do.
Tap your part first. if the hex is out a tiny bit, big deal. obviously try to get it good, but just tap your piece first thing.
Then either make an arbour, use a bolt or even the tap and chuck it up in your 3 jaw running true. Thread on your tapped out hex piece and turn your OD to your pulley dimensions.
This is about as good as it will get.
|
|
|
Post by pitobread on Jul 10, 2020 10:01:46 GMT -5
The best option is to tap your part, then chuck up a hunk of garbage, turn it and put a thread on it to suit then thread on your adapter to that and turn all your operations onto the piece that you threaded on. Good excuse to learn how to thread! There are lots of youtube tutorials out there to get you making scrap parts er, good parts!
Then from that you could mill your own hex onto it.
That is about as dead nuts other than using a threading bar to get everything running as true as possible. But sometimes you just have to work with what you have.
|
|
|
Post by pitobread on Jul 10, 2020 10:07:17 GMT -5
Other things to consider, are you center drilling your hole? your tap drill is it cutting evenly?
Once the hole is cut is it running true end to end?
All of that stuff can play a part in your tapped hole running true to everything else.
If you have a tiny boring bar, cutting the hole undersize and boring it true to center is always your absolute best option. The tap, much like a drill will follow the path of least resistance, once there is a hole there it wants to try and follow it as much as it can.
You can make a tiny boring bar out of the solid end of an old drill, or any piece of high speed steel and some grinding time.
|
|
|
Post by pitobread on Jul 10, 2020 10:25:45 GMT -5
Final though, put a nice chamfer on the hole before trying to drive the tap in will help a lot with centering.
|
|
|
Post by 90GTVert on Jul 10, 2020 11:05:18 GMT -5
SO all that said, here is what I would do. Tap your part first. if the hex is out a tiny bit, big deal. obviously try to get it good, but just tap your piece first thing. Then either make an arbour, use a bolt or even the tap and chuck it up in your 3 jaw running true. Thread on your tapped out hex piece and turn your OD to your pulley dimensions. This is about as good as it will get. John actually suggested the same to me in a PM earlier. Basically. He said to use a chopped off crankshaft. I have one of those already because I used it to lighten a flywheel. So if you tap first, then machine, it pretty much forces everything to run true to wherever the threads are... aside from the hex section. Other things to consider, are you center drilling your hole? your tap drill is it cutting evenly? Once the hole is cut is it running true end to end? All of that stuff can play a part in your tapped hole running true to everything else. If you have a tiny boring bar, cutting the hole undersize and boring it true to center is always your absolute best option. The tap, much like a drill will follow the path of least resistance, once there is a hole there it wants to try and follow it as much as it can. You can make a tiny boring bar out of the solid end of an old drill, or any piece of high speed steel and some grinding time. I am center drilling. I never even knew what center drills were when they showed up at my house before the mini-lathe, but have since watched drill bits flex enough and done things off center enough to realize their importance. I don't know that the hole is running true. I'm cutting it so I can end up with 0.710" depth when finished, in a part over 2" long so it's a blind hole. Not really sure how to check the hole itself other than putting a rod matching the ID at some point of the process and seeing if there's runout. I did grind an old drill flat on the end and then cut reliefs in it so I could finish the hole more square. The depth measurements around the hole were pretty close with quick checks. At the time I wasn't worrying about great precision, but mainly making sure the center and edges were roughly flat. Thanks for the advice. Even though I do like John's plan better than what I've been doing, it aggravates me to get things wrong when I really have no idea what I even did. I decided to try it again. Went out this morning and chucked up a new piece of hex. This time I indicated on it. After 15-20 minutes, I couldn't manage to get it closer than 0.001" of runout. Not sure if it's accurately runout since I was indicating from the lowest point of each flat section. I'm also not confident that hex stock (or at least this hex stock) is super precise on all flats. I never did this the first time around. Thought maybe this would be the key. I went through and carefully drilled the hole. Started with a center drill closest to the size and went up in drill size only in small steps. Finished with flattening the end of the hole. Moved on to tapping. Getting it started with the tap in the tailstock. I can only go so far this way because the mini-lathe doesn't have the torque to get in very deep and then I can only turn it so far by hand. I left the tap in place and spun it. It's wobbly already, before I've done any hand tapping. OK. WTF? I put the tap in the headstock chuck and spun it. Wobbles. Looks pretty similar to my finished tapped parts. So I guess the only way to easily fix that is to buy a new tap and hope it ain't wonky.
|
|
|
Post by pitobread on Jul 10, 2020 12:50:48 GMT -5
It could be your tap is worn out and cutting oversize. That will for sure not make your life easy.
This is why tapping isn't that precise. I mean in a ultra rigid VMC with a roll or form tap yeah you can make some damn precise threads, but when you start putting less rigidity and the human factor into it, you end up with some issues.
The other problem is trying to use a thread to locate, I mean it has to have clearance to fit, so it can't be size for size and there will be slop no matter what.
You could look into a tighter tolerance tap. not all taps are created equal and you can get taps with less thread clearance You could look for a H2 tap.
Out of curiosity what is your tap drill size? what is the thread you are trying to achieve?
You are right, hex stock isn't "perfect". .001 sounds pretty damn good to me.
Also since your tapping blind try and get a black oxide spiral flute, looks to be about a 20 dollar tap in H2, i am guessing this is m8 or m10.
|
|
|
Post by 90GTVert on Jul 10, 2020 13:34:54 GMT -5
Out of curiosity what is your tap drill size? what is the thread you are trying to achieve? M10x1.25 is the thread I'm after. The drill is 11/32". Chart says 8.75mm, that's 8.73mm. I already ordered a set of taps (taper, plug, bot) by Irwin earlier. Looked at a general purpose tap on McMaster and didn't want to pay $67 plus shipping for one tap. The wonky one is a Snap-On, but it's not like I can get the tool dude to stop here to even see if they'd replace it. Only been trying for 10+ years to get him to stop just once and he refuses (or actually says he will when he goes by every day and never does) so all Snap-On "lifetime warranty" stuff ends up being replaced with other brands.
|
|
|
Post by pitobread on Jul 10, 2020 13:47:04 GMT -5
|
|
|
Post by 190mech on Jul 10, 2020 16:49:04 GMT -5
Same with my shop,if I dont buy a $10,000 "taco wagon toolbox" from the snap-on guy yearly,he isnt to be found..He even stopped coming to the hospital helicopter shop on the field as their tool boxes are still working!!! PS,I've been picking up spiral flute CNC taps when replacements are needed,they seem to have an aggressive but smooth cut over the old straight flute taps.. 
|
|
|
Post by pitobread on Jul 10, 2020 23:03:09 GMT -5
Yeah those spiral flute CNC taps are the bee's knees.
|
|
|
Post by 90GTVert on Jul 13, 2020 16:06:46 GMT -5
New taps arrived. I had the other end of one of the previously tapped parts waiting with runout down to 0.002" or less and a hole bored. Tapped. Runout. 0.028" mounted to the crank end after setting the crank up in there at basically 0 runout. 0.038" with the tap screwed into the end of the part with the part in the chuck. 0.014" trying to measure on the end of the taper tap in the chuck.
So taps don't seem to be running true for me. Then I guess I'm adding my own runout too. I watched a few vids and I see others that seem to be proficient machinists mounting the tap in the tail stock chuck and going in to start. Others use different devices to help them out like pito said.
I may end up drilling all the way through a piece to see if it's coming out crooked there or if it is pretty much all the tapping process.
|
|
|
Post by oldgeek on Jul 13, 2020 20:58:52 GMT -5
90GTVert Would you mind snapping the occasional picture of your lathe setup as you are working on a part. It would help people like me that have no clue how to setup for even basic stuff on the mini lathe. I get frustrated every time I get near my lathe. You could post them in your mini lathe thread
|
|