|
Post by oldgeek on Mar 16, 2019 12:42:42 GMT -5
Well after tear down and quick inspection of the motor it likely would have not run very long anyway. I am not sure which came, first a bad seal on the FW side or a bad crank bearing on the same side. The spring that holds the seal on the sealing surface came off, I may have pushed the seal n a bit far when I installed it. 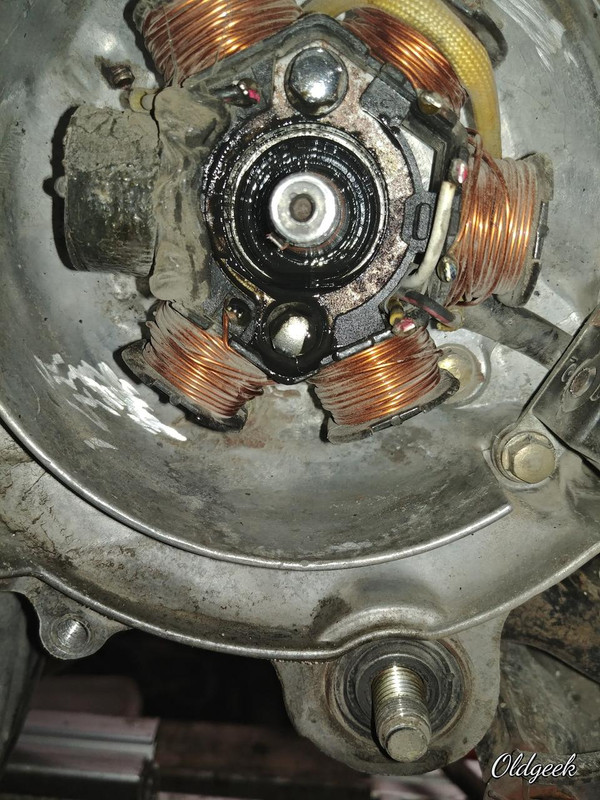 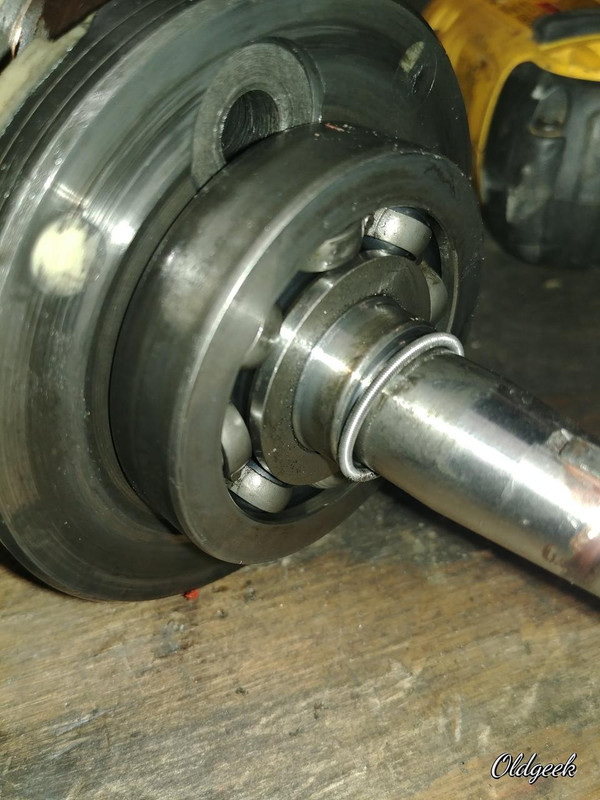 The bearing had just started getting sloppy, you can see where it allowed the crank to contact the cases, more so on the FW side than the variator side. 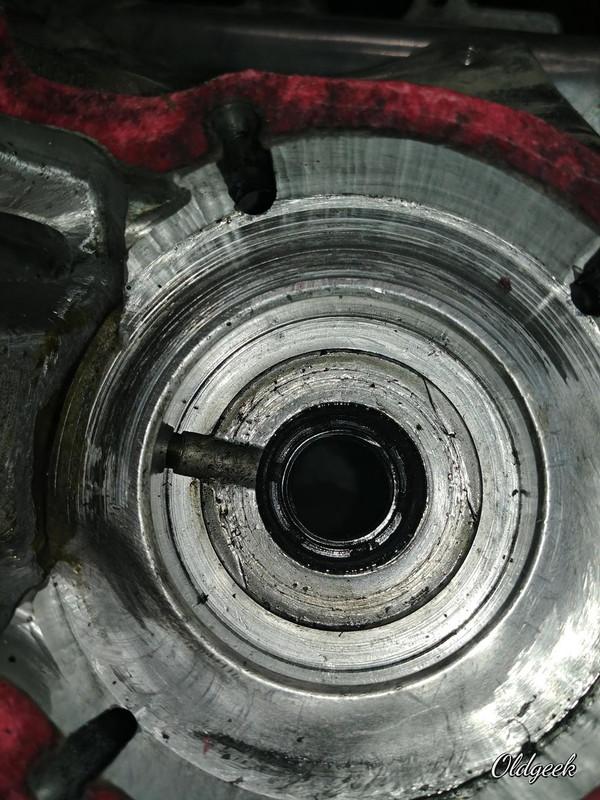 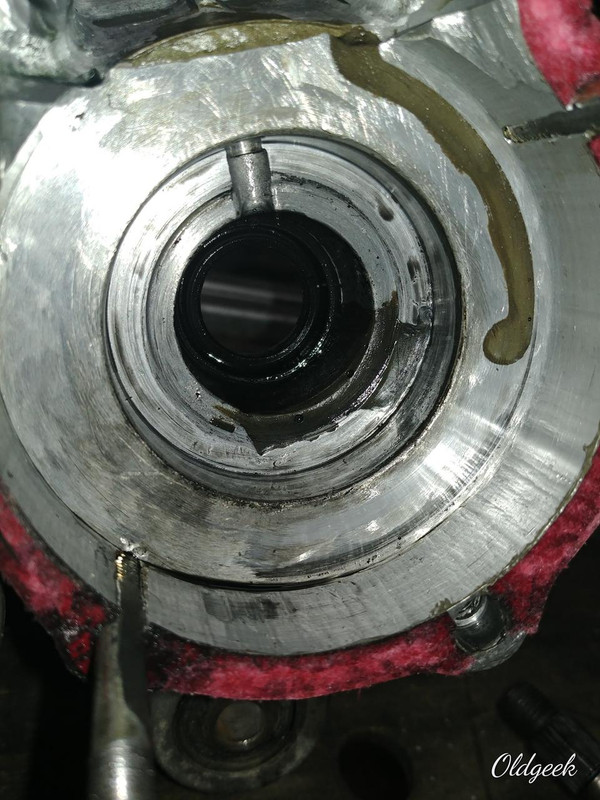 The big surprise to me was when I opened the gearbox expecting the repair I made to be trashed but it was not. The real issue in the gearbox was the brand new outboard bearing for the primary shaft was bad. Most likely that is where all the metal in the gearbox came from. 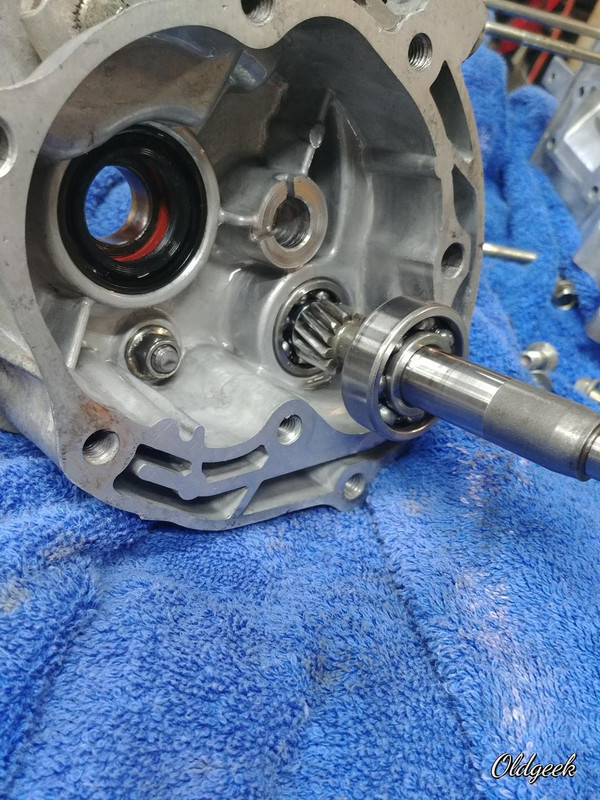 The only problem with the repair I made is that the bushing turned just a small amount, I should have put a pin in it like I was going to. 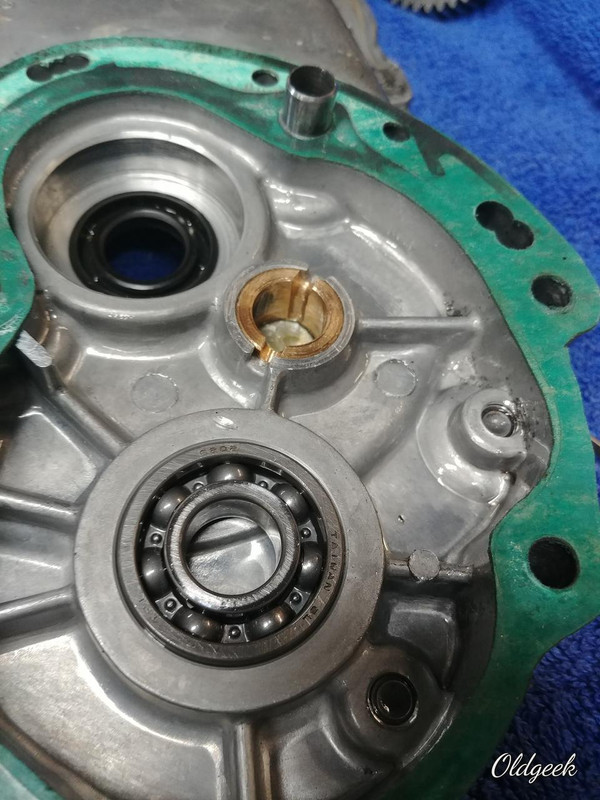 I may try to rebuild this set of cases if I can get the crank bearings sorted out. There was not a trace of the retaining compound I used to hold the bearings in place when I pulled the cases apart. I checked fitment of a brand new bearing in the cases. They are really no looser than they were when I assembled it the first time. I may try to do something else to hold them in place.
|
|
|
Post by 190mech on Mar 16, 2019 17:22:16 GMT -5
Have had some success with using shimstock to tighten main shaft bearings to cases,Brent has done it too..Might be worth a try,if the shim doesn't get crooked during fitment all is good..For epoxied cases that cant be heated when installing bearings,I bump them in with a brass hammer till they seat,then use a Tusk style tool to pull the crank into each side,yeah its more work,but the epoxy doesn't get soft...
|
|
|
Post by oldgeek on Mar 16, 2019 17:47:13 GMT -5
Spent about 2 hours trying to get the bearings off of the crank, failed miserably. There was even a welder involved. 
|
|
|
Post by 190mech on Mar 16, 2019 23:35:10 GMT -5
|
|
|
Post by oldgeek on Mar 17, 2019 9:05:32 GMT -5
Checking the piggy bank and cup holder for change now!
|
|
|
Post by oldgeek on Mar 17, 2019 14:40:34 GMT -5
I finally got the bearings off, but it was not easy even with the right tools. Here is a picture of one of my fails. I thought this setup would pull the bearing right off but my krap weld broke. then I welded the chain to the sides of the bearings, but the bearing broke. Thats when I gave up yesterday. 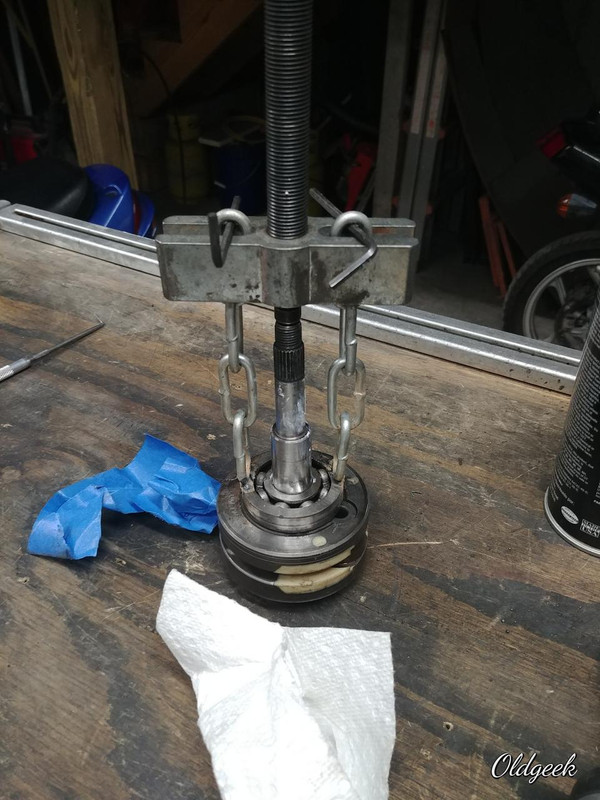 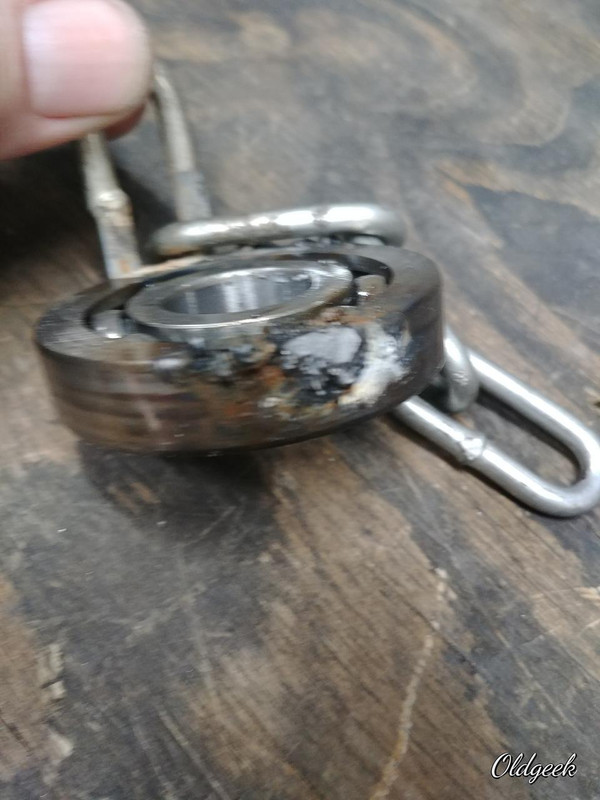 Today I went to HF and bought the "proper" tools. I ended up with this set. It was $39.99 but I used a 20% off coupon so $31.99 was much better. 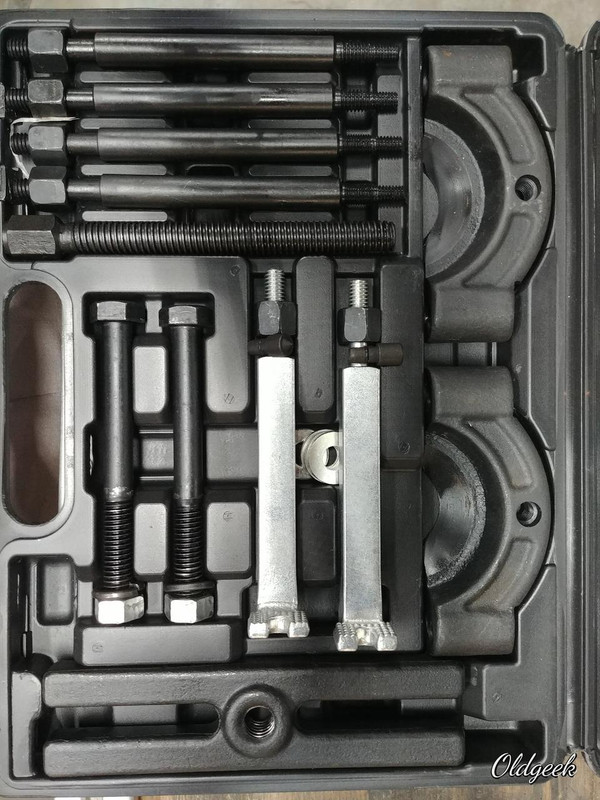 Getting the tool to fit behind the bearing was impossible on this crank. The sides of the crank are dished and the bearings sit recessed in the dished part of the crank wheels. 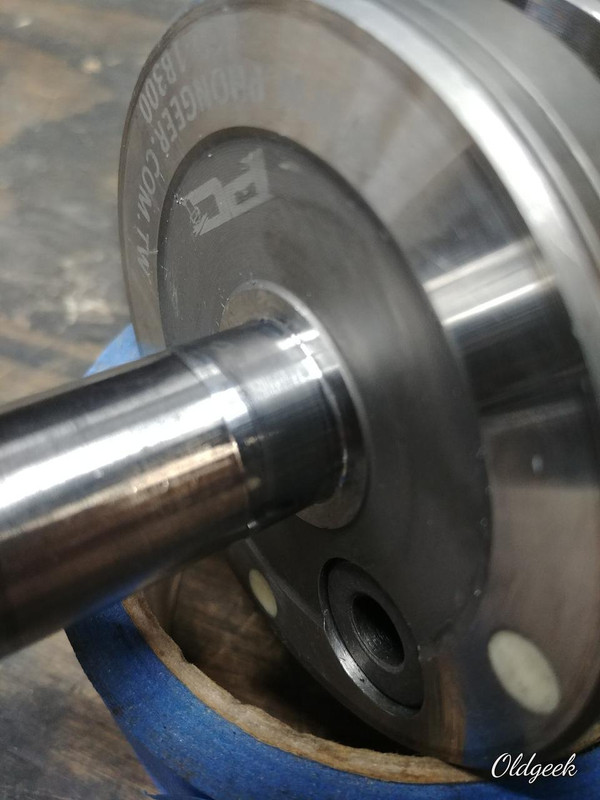 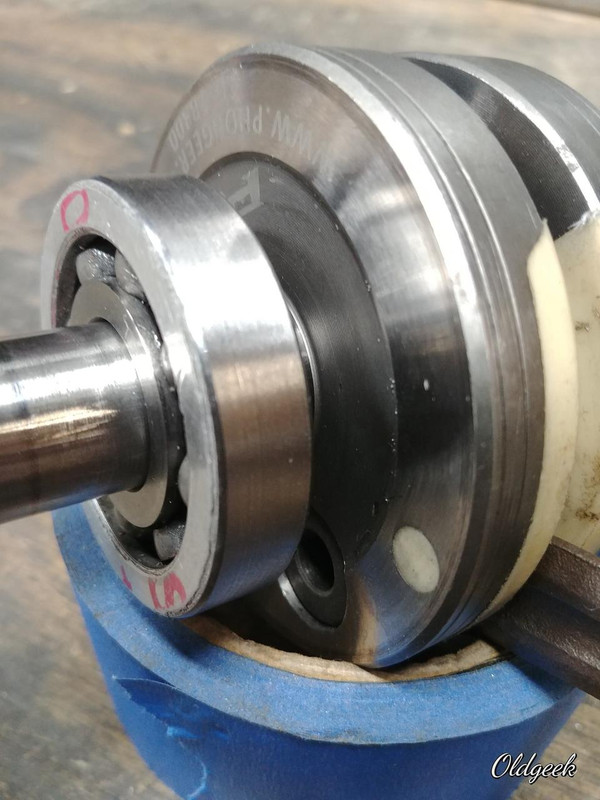 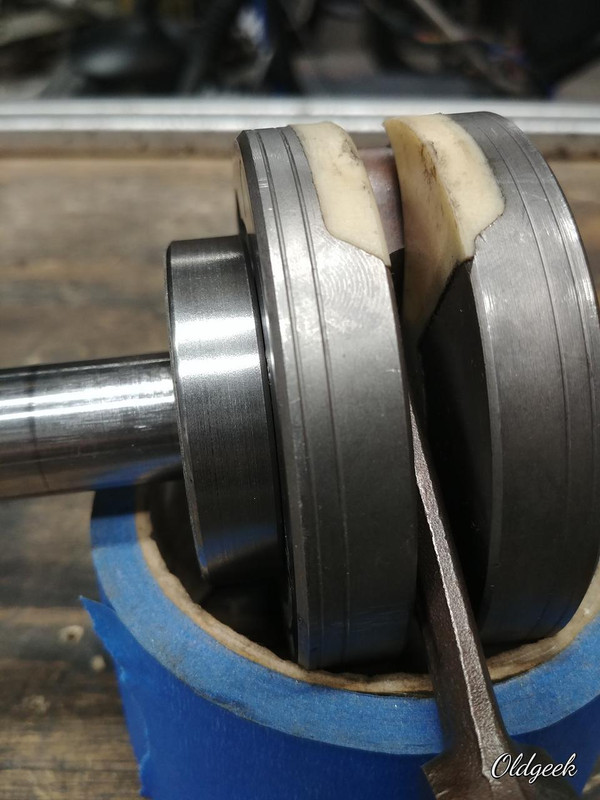 I ended up mostly just squeezing the bearings with very little if any of the tool under the bearing. I went straight to the 20 ton press and it is a good thing I did. I had lots of pressure on it and was scared something other than the bearing was going to give before it finally moved with a loud pop. Moved the tool to the variator side bearing and had to use twice as much pressure as I used on the other side to get it off.
|
|
|
Post by pitobread on Mar 17, 2019 15:04:37 GMT -5
Often starting those separators, I only have a teeny bit under the bearing then I press it off.
|
|
|
Post by Jwhood on Mar 17, 2019 17:15:17 GMT -5
Damn geek that's impressive that even welding link to bearing didn't even budge it loose
|
|
|
Post by oldgeek on Mar 17, 2019 17:39:56 GMT -5
Damn geek that's impressive that even welding link to bearing didn't even budge it loose Err my welding is pretty krappy, but I did put some pressure on it with that arrangement and it did not budge.
|
|
|
Post by oldgeek on Mar 21, 2019 21:41:54 GMT -5
I ordered some .05" aluminium sheet from Feebay. I plan to make a spacer to fit between the case halves so hopefully I can use standard width crank bearings, instead of the special narrow bearings that you are supposed to use with this crankshaft.
I have also been thinking about reasons that the crank bearing on the FW side could have failed. 1) the bearing was krap. 2) the FW may be out of balance. 3) the seal leaked and helped kill it. 4) the retaining compound failed and the resulting bearing slop beat the bearing to death. 5) Poor lubrication because I closed up the pocket at the top of the crank bearing oiling passages.
Anyway, one way or another I am going to try and use this set of cases for this same build again.
|
|
|
Post by oldgeek on Mar 22, 2019 22:41:23 GMT -5
I have come to the conclusion that these Michelin SC tires are very hard to mount and unmount compared to the other brands I have worked with. I am working on swapping the Michelins off of some of my other scoots and putting them on my Kymco scoots. I am also balancing them in the process.
To make the balancer for the front wheels, I used an axle from the red Kymco, it was pretty hard to get the axle out of the forks on the red Kymco. I noticed it is very slightly bent, and seemed to affect the consistency of the balancer. So I used an axle from another scoot to balance the wheels. The Michelins are a PITA to work with but it will be worth all of the trouble I am going through when I get them all done.
|
|
|
Post by 190mech on Mar 26, 2019 5:42:06 GMT -5
Intro;Years ago I was installing a BC800 on my sportbike and was going to epoxy the magnet to the fromt wheel.mixed up some J-B(slow cure) and glued the magnet to the wheel,,checked it 30mins later and was shocked to find all the J-B had crawled off the rim onto the magnet!! Fast fwd to yesterday..Thought back to that time and wondered just how thick the steel particles are in J-B,so I mixed up a batch and put it between my caliper jaws and squeezed the jaws hard between my fingers,,.002"!So perhaps this steel epoxy would be a better choice than a clear base locktite product..Even better would be to heat the cases to 200F when doing the install,then they would expand to running temps and hold even better..Its a long shot but may be worth a try for loose case bearing pocket repair... 
|
|
|
Post by oldgeek on Mar 26, 2019 19:06:51 GMT -5
Intro;Years ago I was installing a BC800 on my sportbike and was going to epoxy the magnet to the fromt wheel.mixed up some J-B(slow cure) and glued the magnet to the wheel,,checked it 30mins later and was shocked to find all the J-B had crawled off the rim onto the magnet!! Fast fwd to yesterday..Thought back to that time and wondered just how thick the steel particles are in J-B,so I mixed up a batch and put it between my caliper jaws and squeezed the jaws hard between my fingers,,.002"!So perhaps this steel epoxy would be a better choice than a clear base locktite product..Even better would be to heat the cases to 200F when doing the install,then they would expand to running temps and hold even better..Its a long shot but may be worth a try for loose case bearing pocket repair...  Interesting angle on the epoxy! What you are saying makes sense. I have previously thought about using JB weld, but was worried about the heat, I dont know why though, I dont seem to be afraid of using plenty of JB Weld throughout the cases LOL! The spacer I am making is almost done, it's a fragile thing, the case edges are so thin. I should have made the spacer wider and let the excess hang out of the cases so the spacer would not be so flimsy. I received the 6201 SKF bearings I ordered for the gearbox, and just now realized that I probably need to replace all of the bearings in the gearbox because of the metal that I have been seeing in the gear oil. More time, more money.
|
|
|
Post by oldgeek on Apr 7, 2019 21:01:50 GMT -5
In between rides, I have been slowly putting this motor back together. I have pulled the old bearings from the gearbox and installed the new ones. I also removed the bushing repair I made in the gearbox so I could re bond it into place. Still thinking about drilling and pinning the bushing in place to prevent it from ever rotating.
I am still kicking around ways to install the crank bearings and the crank. The previous set of bearings were pushed onto the crank, and were the hardest bearings to remove I ever dealt with. I think I will sand and polish the crank a bit so the bearings are not quite so hard to install and remove.
To secure the crank bearings in the cases, I believe I am going to try 190mech's JB weld idea. JB weld specifications, if accurate look pretty good when compared to loctite 620. The 620 seems to be the best thing they have for an application like this, and is what I plan to use if I do not use JB weld. I previously used loctite 680 to secure the crank bearings in the cases, but it failed and the bearings became loose. So I figure something that resists heat better and is stronger is needed.
Next up the cylinder needs honed and I have a new set of rings around here for the piston...somewhere.
|
|
|
Post by 190mech on Apr 7, 2019 23:56:55 GMT -5
If the bond is done cold,when the cases heat up they'll expand a few thou thus breaking that bond..Ya got a way to heat them to a contant temp of 200-250 degrees F till the glue sets??
|
|