|
Post by larry001964 on Apr 7, 2012 10:22:24 GMT -5
Decided to take some compression readings, since the engine is thru it's break in period... These numbers are with one base gasket... It looks to be somewhere between 201 to 205 PSI.. Thought I would post this so that others considering building a similar engine would know what to expect.. Here's the first check.. 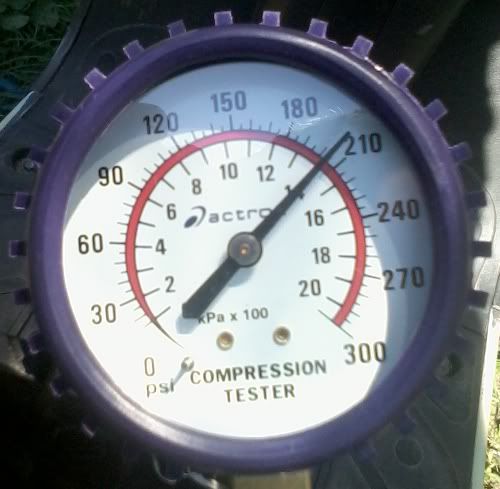 Here's the results from the second test.. Pretty consistent.. 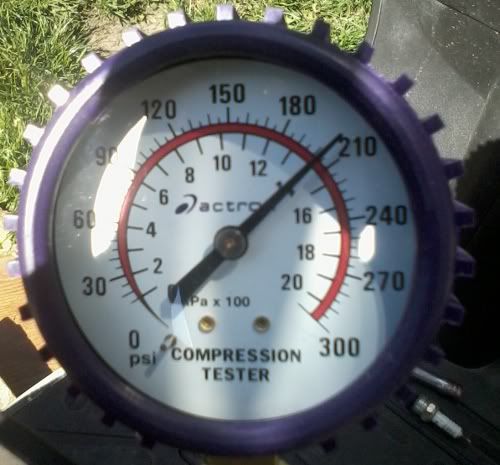
|
|
|
Post by larry001964 on Apr 7, 2012 17:58:42 GMT -5
Well the verdict on the home made key guides is in, after driving 160 miles the new guides are showing signs of being cut thru just like the originals...
Back to the drawing board finding a different material...
|
|
|
Post by larry001964 on Apr 7, 2012 23:17:14 GMT -5
Have an Idea It appears as if the ramp plate is acting like a knife with all the stress and cutting thru the key guides. It cuts thru on the side pushing the variator. Then if not caught in time cuts the variator..
What if I were to double the thickness of the metal on the ramp plate where the key guides go, to displaces the stress over a double the area, then build new custom key guides to match. What do you think ?
I've never seen this kind of problems before in a variator setup on any qmb
|
|
Deleted
Deleted Member
Posts: 0
|
Post by Deleted on Apr 7, 2012 23:30:16 GMT -5
more surface area means less pressure as you know so yeah...i can see what you are seeing...yeah i think that would work..but how to do it? hmm
GD man it must have serious torque. how can a 150 vari not do this im wondering?...they arent much bigger not doubting you...just perplexed...
|
|
Deleted
Deleted Member
Posts: 0
|
Post by Deleted on Apr 7, 2012 23:31:44 GMT -5
and yeah props on that compression...that sucker tighter as James Camerons submarine 
|
|
|
Post by larry001964 on Apr 7, 2012 23:40:24 GMT -5
more surface area means less pressure as you know so yeah...i can see what you are seeing...yeah i think that would work..but how to do it? hmm GD man it must have serious torque. how can a 150 vari not do this im wondering?...they arent much bigger not doubting you...just perplexed... Honestly I'm perplexed too, I've never seen a 150 variator so I don't know.. I know they are bigger, about 115 mm or so compared to my 87 mm.. I think i can build it up with a welder and grind off whats not needed with my Dremel.. And the compression I''m wondering if that's why it's so difficult to start, but it did start three times today with just the starter. And I used Brent's "bbk How To" on setting my rings just recalculated the gap amount for a 52 mm..
|
|
Deleted
Deleted Member
Posts: 0
|
Post by Deleted on Apr 7, 2012 23:46:26 GMT -5
yeah the compression and cranking...thats certainly related. back it down to about 190 with some more base gaskets and it will crank easier...ive done this.
|
|
|
Post by larry001964 on Apr 7, 2012 23:51:57 GMT -5
Ohhh yea that bigger front tire and brake for a 150 helped a lot, no more brake fading, and it actually feels much better and stabler at high speeds, even in cross winds it was stable and didn't feel like it wanted to lift up on me.. World of difference, have to take a newer photo to show all this LOL..
|
|
|
Post by larry001964 on Apr 9, 2012 8:50:13 GMT -5
Think I have and Idea how to fix this variator cutting thru the keyguides.. I'm going to drill a hole thru the first backing plate so the boss can slide thru it, and weld these too backing plates together.. a little grinding and I can make new key guides. What do you think ? 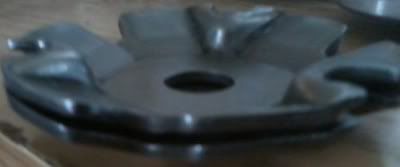 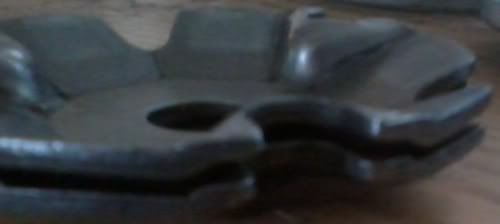
|
|
|
Post by theswede on Apr 9, 2012 12:05:52 GMT -5
Larry, I can tell you you are not alone in having these issues with the backing plate killing the guides. I have had it happen on my china-scoot twice, and I never found a proper fix for it. I simply ended up replacing the variator each time... Both times this happened it was with a kit I bought from Autotech355. You can find more details about the last time it happened here (the busted guide was the least of my problems): scooterrebels.proboards.com/index.cgi?action=display&board=50ccscooters&thread=1791The only (vague) theory I have is that since it is pretty hilly where I live I am subsequently forcing the engine to run at max torque more than the average rider. Also, I have usually been running a little too heavy weights to keep the RPMs down, possibly this could have an impact.
|
|
|
Post by larry001964 on Apr 9, 2012 14:42:38 GMT -5
Hello theswede and welcome. Ohhh im sure it's torque and resistance related, problem is how do we solve it. I believe what im building now should do it. Last little bug left with the stroker i hope
|
|
|
Post by theswede on Apr 10, 2012 5:34:56 GMT -5
Your idea about welding two backing plates together has merit, but I think you may run into issues. If you slide the boss thru the inner plate, I believe you will end up with roller movement issues. The rollers will no longer have enough space to move all the way up the ramp as the plate now sits closer to the rollers. Also, the plate may end up grinding against the ramp as mine did when my dr pulley sliders had worn out...
I think that welding the plates together, and then use a lathe to remove the middle part of the outer plate (to that it is returned to the same thickness around the center) would be a better way of doing it.
Or perhaps cut out the guide holder parts of the 2nd plate, and then weld these onto the 1st plate. That's probably easier.
An alternative which I have considered doing myself is to fab up guides out of bronze. That may possibly hold out better than the plastic stuff.
|
|
|
Post by rocketdog on Apr 10, 2012 6:07:34 GMT -5
Have you guys tried the DR Pulley Guides? They seem to be made out of different plastic than the stock ones, hence perhaps stronger.
Larry 210 is a lot of compression for the motor. You might try two base gaskets. It would certainly make it easier to start.
|
|
|
Post by theswede on Apr 10, 2012 9:22:14 GMT -5
I tried Dr Pulley guides the first time this happened to me. They disintegrated in no time at all...
|
|
|
Post by larry001964 on Apr 10, 2012 10:06:39 GMT -5
I tried Dr Pulley guides the first time this happened to me. They disintegrated in no time at all... Hi guys and thanks for all your input it is greatly appreciated, I'm pretty convinced that it's the thickness of the backing plate and the higher resistance created by the higher torque and speeds,, I do think theswede is right in his case also with hills, it makes the backing plate like a knife and cuts just about anything plastic you use.. I thought of bronze for new guides... Not sure what metal to metal contact would do with no lubrication so I was trying to avoid that, also I'm sure it would give a tinging sound at an idle, and im not sure it would not damage the aluminum variator.. I was in Fort Wayne Sunday seeing my newest granddaughter, stopped by a friend of mine that sells and repairs scoots, he was showing me a 150 variator.. The 150's are a little thicker, and the outer diameter of the key guides is longer giving more leverage and less stress, the guides on the variator are also heaver.. I'm really thinking doubling the thickness of the key guide arena on the backing plate and custom made key guides is answer.. But how to accomplish this is the question... I agree about doubling the plates may cause roller issues.. Been looking at that and I just don't know... What ever the answer is I would like it to be something easily duplicated so that others experiencing this can fix the problem.. But what I'm thinking is using a mig welder building up the key guide area only then grinding it down to the thickness I want 4.5 mm then making custom keys to match.. On the compression, yea I've been thinking I need to tear down the top half and get that extra base gasket in there. Been looking for a good set of rings and gaskets without having to buy an other kit.. Not finding much in just the gaskets and rings for a 52 mm, so I guess it's going to be another NCY 52 mm kit and a extra base gasket.
|
|