|
Post by 90GTVert on Apr 10, 2021 9:17:28 GMT -5
Thank you!
|
|
|
Post by mrchilled85 on Apr 10, 2021 9:26:38 GMT -5
dam what a lovely gift 
|
|
|
Post by FrankenMech on Apr 10, 2021 19:20:40 GMT -5
The universal thread type for adapters seems to be a tapered pipe thread. Taper pipe thread is one of the worst thread types for leaks and problems. Everyone seems to use it for an intermediate thread type though. Fortunately there are multiple types of thread sealants available.
|
|
|
Post by 90GTVert on Apr 15, 2021 11:59:50 GMT -5
I got the adapter from Scott a few days ago. Thanks again!
I hooked up the regulator and hose today. Turned the tank on and sprayed connections with soapy water to see if I saw bubbles. That looked OK. The regulator dial was closed, so I opened it a little and the ball popped up to something like 5-10 LPM IIRC. I went to adjust it and the ball just dropped, like there was no pressure. The gauge on the regulator says about 1,750 psi regardless of if the bottle is on or off. I tried turning the dial off and way open and opening and closing the bottle. No change. I don't know what I've done, but I'm guessing either I broke it or it's a faulty regulator?
Sorta EDIT : Before I hit post, I did a quick search. So I guess the ball is only supposed to move when there is gas flow... and there's no gas flow if you're not using the welder. The gauge shows bottle pressure and won't move, even with closing the bottle, till gas moves.
The only high pressure bottles that I ever recall working with were nitrous bottles and they just had a valve to open/close and a pressure gauge so this is pretty new to me. I'll figure it out eventually.
I did watch a couple of TIG vids, because I was totally lost with a lot of the concept. At least I mostly know what things do now. Assuming the regulator is fine, I'm hoping to set the torch up later and see what happens. I bought a cheap auto-darkening helmet lens that is now taped to a GoPro. Not sure if I'll get anything worth watching out of that, but I was kinda hoping to show just how poorly I start off.
|
|
|
Post by Kenho21 on Apr 15, 2021 22:31:35 GMT -5
Man, I miss all the good threads. Congrats man! I have little doubt you’ll become proficient with time.
I’m sure you’re just as grateful as you say, and rightfully so. I hope everyone has others around them that make gratitude come so easily.
|
|
|
Post by 90GTVert on Apr 15, 2021 23:00:34 GMT -5
I'm really tired ATM, but I'll at least leave you with a screenshot of me trying to burn my pinky off so you can see that the welder works. Needs a better operator. 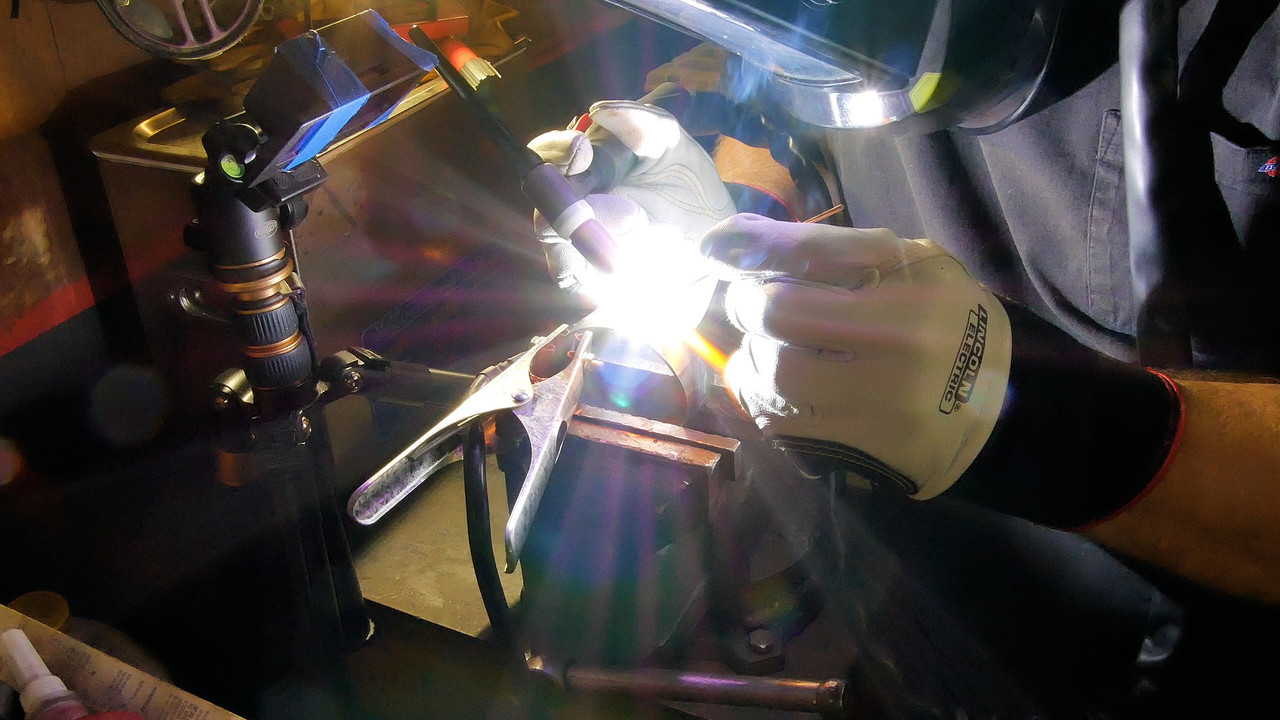
|
|
|
Post by FrankenMech on Apr 16, 2021 4:18:57 GMT -5
You will get the hang of it. I always felt that a TIG welder was like O-A welding with an electric flame. I haven't TIG welded since about 1972 so I am just a bit out of practice. I haven't done any O-A welding in 20+ years.
|
|
|
Post by 90GTVert on Apr 17, 2021 0:08:14 GMT -5
Vid is up! I wanted to share the whole process from start to the first TIG welds I've ever made. I left in all the bits that make me sound dumb, but I hoped to show just how clueless I was about TIG beforehand (and still am). At least I've made it to a point where I know what the knobs do, even if I can't produce a decent weld. youtu.be/1jQ_G3xdVCM
|
|
|
Post by yambw’s on Apr 17, 2021 2:56:28 GMT -5
community’s epic! Guys sending equipment so you can show/teach like minded others with there projects...brilliant!
|
|
|
Post by oldgeek on Apr 17, 2021 6:03:36 GMT -5
Your first attempts look pretty good to me! The foot switch is just a switch. On a entry level machine there is no amp adjustment on the fly unless you reach over and turn the knob while welding with your third hand. Lol!
As someone commented on your video, try fusion welding without a rod it is a lot easier and works great on well fitted thin parts like the pie cuts.
Another thing that may help is less tilt on the torch. IRRC no more than 15° tilt, It keeps the argon plasma stream directed to the weld puddle, the leading edge of which should be your focus point.
Have fun!
|
|
|
Post by AtariGuy on Apr 17, 2021 9:12:04 GMT -5
Your first attempts look pretty good to me! The foot switch is just a switch. On a entry level machine there is no amp adjustment on the fly unless you reach over and turn the knob while welding with your third hand. Lol! As someone commented on your video, try fusion welding without a rod it is a lot easier and works great on well fitted thin parts like the pie cuts. Another thing that may help is less tilt on the torch. IRRC no more than 15° tilt, It keeps the argon plasma stream directed to the weld puddle, the leading edge of which should be your focus point. Have fun! indeed! And i second the great job you're doing! You literally went from "i'm not sure what these parts are" as you unboxed them to an assembled, working tig welder machine. Thats the first 2 weeks of classes in welding school. After that, it's literally torch time. I have yet to meet anyone who hasn't needed to resharpen a tungsten at least once in their first 15 minutes of ever picking up a torch. When i was being taught, my mentor told me to just focus on the torch (as oldgeek and the youtube commenter both mentioned) - and to go for 8 inch passes. And a tip for tungstens, use the side of your grinder and point the tip away from the rotation. The sharper the point, the less "arc spray" you'll have. The shop i worked at in minnesota had stupid expensive benchtop diamond wheel sharpeners, but a 120 grit angle grinder sanding disc works just as well. 20 degrees is a good tip (think sharpened pencil)
|
|
|
Post by captincvmn on Apr 17, 2021 10:39:58 GMT -5
I myself cringed watching the point up sharpening of the tungsten. If it were to dig in or catch it would impale you. Likewise sideways to the wheel the tool rest can swallow the object wedging it against the wheel. Side wheeling would be safest but after awhile can chew into your stone and cause separation of the stone in extreme situations.
I’m always looking at what can hurt me before proper technique.
|
|
|
Post by 90GTVert on Apr 17, 2021 10:58:40 GMT -5
I myself cringed watching the point up sharpening of the tungsten. If it were to dig in or catch it would impale you. Likewise sideways to the wheel the tool rest can swallow the object wedging it against the wheel. Side wheeling would be safest but after awhile can chew into your stone and cause separation of the stone in extreme situations. I’m always looking at what can hurt me before proper technique. And a tip for tungstens, use the side of your grinder and point the tip away from the rotation. The sharper the point, the less "arc spray" you'll have. The shop i worked at in minnesota had stupid expensive benchtop diamond wheel sharpeners, but a 120 grit angle grinder sanding disc works just as well. 20 degrees is a good tip (think sharpened pencil) I did it that way because of watching a pro "Mr. TIG" show how to grind tungsten. Here's the first and only video that I watched about grinding before I did that and it should start right at the part that I'm talking about. Oh, and I looked at a page that said to grind that way to have grinding marks running with the length of the electrode and not to have grind marks going around the electrode. I probably wouldn't have bothered to watch any video about that, but the lathe has made me respect angles of tools enough that I did think to look into that.
|
|
|
Post by captincvmn on Apr 17, 2021 12:48:52 GMT -5
It just worries me is all. No injuries allowed.
|
|
|
Post by captincvmn on Apr 17, 2021 15:38:36 GMT -5
This is my welder on my work truck I use. 3600 hours on it and climbing. Reliable Onan engine. Sits outside in the weather all the time. I’ve had this particular welder on a work truck for 14 years and I know who had it on a truck before me. It’s pushing close to 25yrs old I bet. 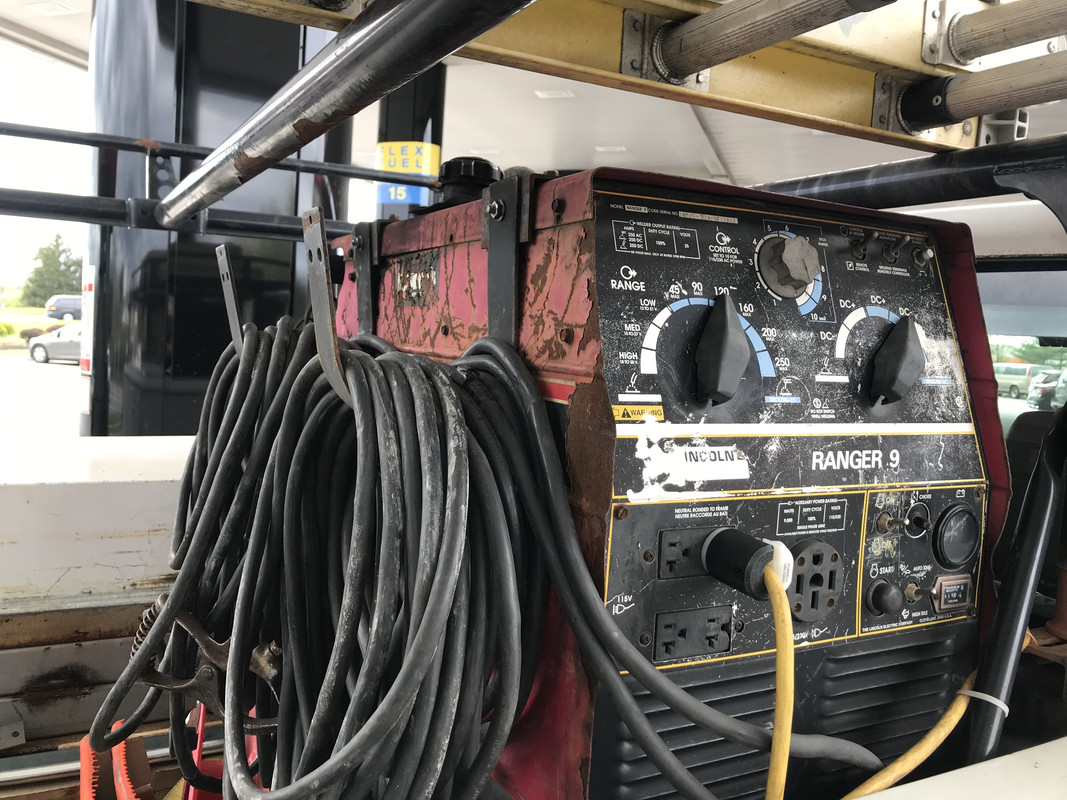
|
|