|
Post by Lucass2T on Nov 13, 2019 6:58:13 GMT -5
Ideally you would want a tps to control timing. I think the later honda cr125's with keihin carbs have throttle position sensors for input for the ignition.
Maybe some 125cc 2t roadbikes have m too?
|
|
|
Post by 90GTVert on Nov 14, 2019 15:09:42 GMT -5
|
|
|
Post by 90GTVert on Nov 15, 2019 11:24:37 GMT -5
Someone says I need to weld my crank pin in with this ignition. I thought this was only for really high powered stuff, like beyond what I'll probably ever do with it. If there were truly a 14HP limit (that seems really precise), then an awful lot of midrace stuff would need welded cranks. 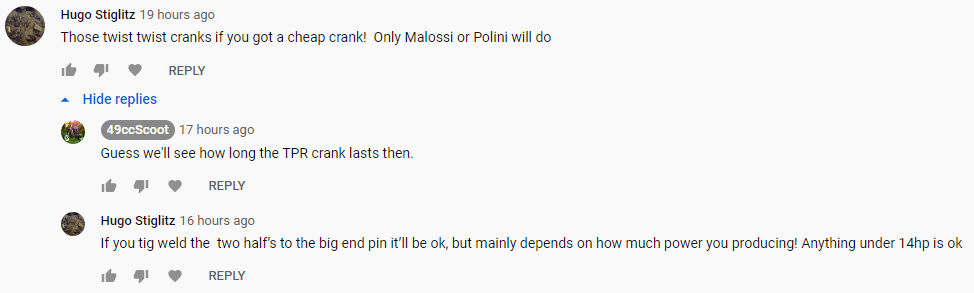 I also would have thought trying to spin a heavier flywheel would be more likely to twist a crank, but I don't always do well with my intuition regarding physics. Should I be constructing a 1/4" thick steel scatter shield around the engine before I consider an exhaust?
|
|
|
Post by pitobread on Nov 15, 2019 15:11:10 GMT -5
None of my cranks I have had are welded.
I guess they all blew up without me knowing.
|
|
|
Post by 190mech on Nov 15, 2019 19:08:28 GMT -5
Welding a crank pin is a band-aid for a poorly designed crankshaft,let those arm chair advisors weld theirs all day long,us normal(read dumb) folks dont like the idea as heat affected zone causes warping and lots of tool steels are not weld friendly,other than that its the perfect solution for a non existent problem... 
|
|
|
Post by aeroxbud on Nov 16, 2019 17:45:17 GMT -5
Could welding it poorly even distort the crank somewhat?
|
|
|
Post by 90GTVert on Nov 16, 2019 18:15:46 GMT -5
Sounds like it could cause all sorts of problems. I think I'll just take the cylinder off and fill the cases with concrete for reinforcement. Probably the safest bet.
|
|
|
Post by ryan_ott on Nov 16, 2019 19:48:42 GMT -5
I think I'll just take the cylinder off and fill the cases with concrete for reinforcement. Probably the safest bet. Don’t forget the valves, valve springs, modify the cylinder head, find a place for the oil pump and dipstick... Should be pretty safe then. Oh and a CV carb...
|
|
|
Post by jloi on Nov 16, 2019 20:29:48 GMT -5
CONCRETE OMG!! NO . you should be using Portland cement
|
|
|
Post by Kenho21 on Nov 16, 2019 21:23:35 GMT -5
I like to use a high-temp candle wax.
|
|
|
Post by 190mech on Nov 17, 2019 9:44:47 GMT -5
Been thinking about twisted scoot cranks;I saw a lot of twisted cranks years ago with MX and enduro bikes,most were caused by poor riding practices,jamming on the rear brake with the throttle on,downshifting at high RPM,over revving for long periods were the main reasons..With a scoot CVT system,a crank has a pretty gentle life as everything in the drive line is under some slippage..
|
|
|
Post by 90GTVert on Nov 19, 2019 15:55:02 GMT -5
|
|
|
Post by Kenho21 on Nov 19, 2019 16:45:32 GMT -5
Nice work and great vid! That looks like it’ll be a super handy tool. Smart.
|
|
|
Post by 90GTVert on Nov 20, 2019 17:59:01 GMT -5
I could use a little help on an issue. Not for me, asking for a friend. lol
Actually, back to the ground to kill vs ground to run issues. I should be fine as this is ground to kill and my scoot is the same way. I've got my MVT setup on the engine and filmed all of that and done a lot of editing already, but I'm missing that bit that I'd like to at least give a real quick bit of info about for the people that it may help.
Ryan has mentioned to me on a few occasions that a relay can be used to make the ground to run system work with the ground to kill, but I've never seen any details.
The only thing I can think of wouldn't really be a perfect setup, but it could work (I think). You could use a relay basically as intended, but switching a ground on instead of typical batt power on. If the switching signal were connected to the ignition switch's switched batt + wire, and then a ground was put in place of the usual batt + input on a relay, and the accessory terminal of the relay were connected to the wire leaving the ign to go to the CDI, then when the key is turned on the CDI should receive the ground that it needs to run via the relay (as long as there is battery power).
That sounds simple enough, but then the kill switch operation will be backwards, because no fix is applied to it. It's just enabling the ignition when the circuit is closed (kill) and disabling with it open (run). It also depends on having a battery, not that that part should be a big deal since it wouldn't even have to be in great condition for a switching signal.
Is that the common solution, or is there something I'm missing with the relay setup/selection that will allow it to sort of reverse the entire circuit so the kill switch operates as it should as well?
|
|
|
Post by 190mech on Nov 20, 2019 19:19:13 GMT -5
ERR,It seems we are talking about AC CDI(ground to kill) and DC CDI(open to kill),if thats so,then if an AC CDI system is installed on a DC CDI engine the best cure is install a proper switch and not a relay to do the work..Designing a relay system should be considered if what happens when the relay coil fails?Then the system should keep running..Thats the way we do it on aircraft anyway...
|
|