|
Post by xtremrox on Jul 5, 2024 10:48:48 GMT -5
And yeah these non programmable cdis are pita to work, you want 12-16° btdc timing at peak power but if you get that right everything else is f upped The programmable PVL kit is great for this stuff at least. I can set it wherever. Trying to figure out what it wants right now is what's tough for me. For me a curve made like this has allways worked 0-idle range rpm 10° Idle range 25° Idle range-powerband 35° Then at begining of powerband usually 8-9krpm you set a point at 35° and next point at peak hp rpm at 15° Then next point at max rpm at 8° From there its easy to fine tune if the middle of powerband feels kinda lazy set a point between 35° and 15°,then rise that point a bit and test add and rise points till it feels good. If egt seems too high rise the last point degree by degree until egt is fine. If peak power seems a bit low try to rise or lower the 15° point.
|
|
|
Post by 90GTVert on Jul 5, 2024 10:59:37 GMT -5
The programmable PVL kit is great for this stuff at least. I can set it wherever. Trying to figure out what it wants right now is what's tough for me. For me a curve made like this has allways worked 0-idle range rpm 10° Idle range 25° Idle range-powerband 35° Then at begining of powerband usually 8-9krpm you set a point at 35° and next point at peak hp rpm at 15° Then next point at max rpm at 8° From there its easy to fine tune if the middle of powerband feels kinda lazy set a point between 35° and 15°,then rise that point a bit and test add and rise points till it feels good. If egt seems too high rise the last point degree by degree until egt is fine. If peak power seems a bit low try to rise or lower the 15° point. That's somewhat close to what Wobbly recommends according to an old post that 190mech shared. I thought it would be interesting to fine tune with this ignition, but everything else is so frustrating ATM that it's just another variable to further confuse myself with. One thing I can't change is the starting advance. That is a bit annoying. It's trying to start at it's mechanical timing, which is 30* from what the Andromeda software instructions say and what I saw when I was trying to start it with a timing light after I first got it. I could set mechanical timing lower and advance the curves accordingly, but I don't think I could make 10* work within it's limitations for earliest ignition timing points. As long as it keeps starting, I'll leave it as-is.
|
|
|
Post by xtremrox on Jul 5, 2024 11:55:16 GMT -5
For me a curve made like this has allways worked 0-idle range rpm 10° Idle range 25° Idle range-powerband 35° Then at begining of powerband usually 8-9krpm you set a point at 35° and next point at peak hp rpm at 15° Then next point at max rpm at 8° From there its easy to fine tune if the middle of powerband feels kinda lazy set a point between 35° and 15°,then rise that point a bit and test add and rise points till it feels good. If egt seems too high rise the last point degree by degree until egt is fine. If peak power seems a bit low try to rise or lower the 15° point. That's somewhat close to what Wobbly recommends according to an old post that 190mech shared. I thought it would be interesting to fine tune with this ignition, but everything else is so frustrating ATM that it's just another variable to further confuse myself with. One thing I can't change is the starting advance. That is a bit annoying. It's trying to start at it's mechanical timing, which is 30* from what the Andromeda software instructions say and what I saw when I was trying to start it with a timing light after I first got it. I could set mechanical timing lower and advance the curves accordingly, but I don't think I could make 10* work within it's limitations for earliest ignition timing points. As long as it keeps starting, I'll leave it as-is. Ahh so good memories starting a 125cc with 37° btdc 0-8000rpms holy shit the kickback was epic😂
|
|
|
Post by 90GTVert on Jul 5, 2024 18:26:59 GMT -5
Speaking of memories... I was looking for something I posted in this thread and stumbled on a pic of the RC-One's first piston with 2,154 miles on it. I had some fuel supply issues along the way, but life sure was a lot simpler before the PWK. 
|
|
|
Post by 90GTVert on Jul 6, 2024 6:15:09 GMT -5
I got one pipe measured at least. Note on the header flange : Shown are the S6 flange's dimensions with round entry and exit. I made a flange that matches the MHR 94cc oval exhaust port and in that case the ID at the entry would be the equivalent of about a 31.7mm circle and outlet is round 34mm. 
|
|
|
Post by 90GTVert on Jul 6, 2024 8:57:15 GMT -5
|
|
|
Post by xtremrox on Jul 6, 2024 11:06:22 GMT -5
I got one pipe measured at least. Note on the header flange : Shown are the S6 flange's dimensions with round entry and exit. I made a flange that matches the MHR 94cc oval exhaust port and in that case the ID at the entry would be the equivalent of about a 31.7mm circle and outlet is round 34mm.  The malossi exhaust is very close to FOS exhaust caculations for the 94cc (as expected) The stage 6 exhaust is a bit longer (as to be expected with more displacement and diferent cylinder duct desing). Both have almost identical baffle agle, s6 has a bit steeper diffuser (as espected with its better transfer desing) imo if you could make the end of the baffle a bit smaller like 19mm then a stinger adapter with larger id so the baffle goes inside the stinger adabter a bit then test stingers with id from 19-25mm.
|
|
|
Post by xtremrox on Jul 6, 2024 18:28:55 GMT -5
One thing that would be amazing is a portmap with these dilensions 1.Btdc heigth in the bore 2.width and heigth of all ports at 3 diferent points 3.distance from exhaust port top to a transfer ports top 4.width of the bridges between ports With these you can analyze the engine in very precise detail. Also port pos/dir/axial parametres are important
|
|
|
Post by 90GTVert on Jul 6, 2024 21:07:10 GMT -5
|
|
|
Post by xtremrox on Jul 7, 2024 5:05:07 GMT -5
That didnt do much(based my exhaust caculations on that map) only echaust port can be roughly caculated. The transfers are not to scale and no actual size data is given. The exhaust had width data and given that i know its timing i was able to roughly caculate its area
|
|
|
Post by 90GTVert on Jul 7, 2024 7:24:25 GMT -5
That didnt do much(based my exhaust caculations on that map) only echaust port can be roughly caculated. The transfers are not to scale and no actual size data is given. The exhaust had width data and given that i know its timing i was able to roughly caculate its area I knew that wasn't what you were after, but I just got the cylinder back on so taking it off wasn't an option. It's off now though... I got up at 5:30 this morning and figured I had time to take a quick break-in ride before I had to get ready to be somewhere. Started up and idled OK with no drama. I started to move and was sort of surprised it didn't load up because I had put a 50 pilot jet in it, plus the 220 main and the 30 hole atomizer with the largest ID of the ones I have... and it was about 80F with 95% humidity already. Well, I was even more surprised when I got about 40-50ft and it shut off. Went to kick it and it was seized. WTH? I take the CVT cover off, thinking I just got this top end together and I've checked squish twice and I'm careful to keep the engine openings covered so nothing can fall in when it's apart so it has to be OK. CVT is fine. Can't move the variator in either direction. Uh oh. Then I think maybe something fell in to the stator/rotor and jammed up, but it's easier to pull the spark plug out first and look. I see nothing with just a flashlight. I get the borescope and a circlip is between the piston and the head. I hoped I got lucky and it wound up there without damaging anything. Not the case. I had to hammer the piston down, because the circlip was stuck between the bore and the piston and I couldn't get the cylinder off. I went to remove the circlip from the opposite side so I could get the pin out and it was in there with the opening aligning with the cutout in the piston. I know damn well I don't put circlips in like that. I stick a 90 degree end pick in there and all I have to do is twist my fingers with really no force and the clip moves around in it's groove. It should be pretty well stuck in place. The good news is, that made it easy to rotate it and pop the clip out at least. Here's what I'm looking at. Trash. 40-50ft on a brand new piston, cylinder kit with low miles because I just got it within the last couple of months too. 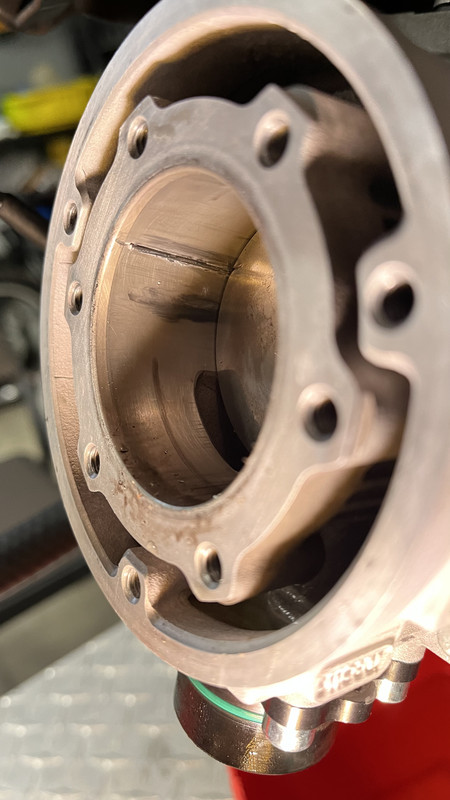 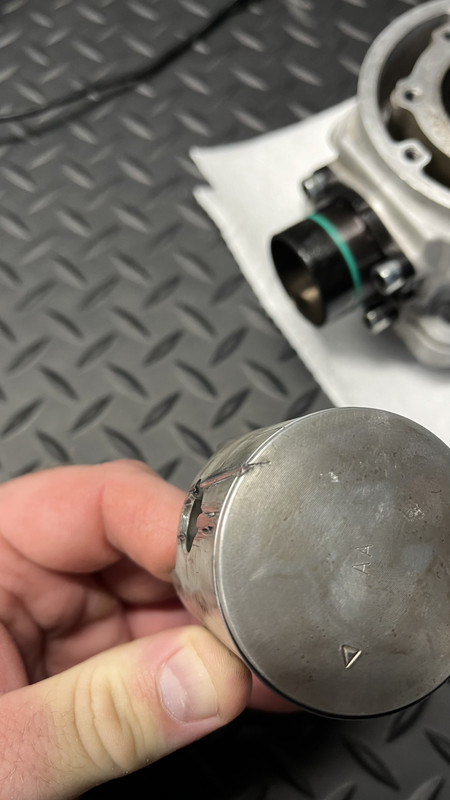 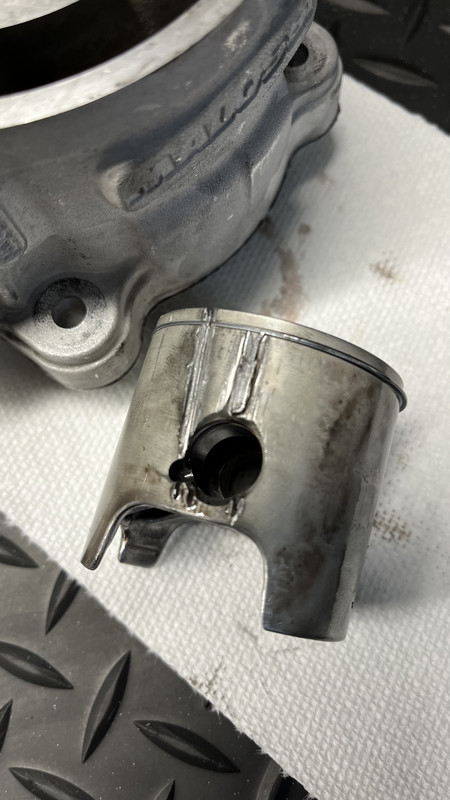 I use a special tool to install circlips. It's been great. Got the 13mm clip version at the same time I got the RC-One 2+ years ago and I've used it every time I've had to install a clip. There's an obvious click and a feeling as the clip goes into it's groove. When I first got it, I'd always go at it with a pick a little to make sure it was in there, but I've grown to trust it so I only do that now if anything looks suspect to me. I do look to see if the clip appears to be in though. I will say that I recall thinking the tool worked a bit easier than normal on both sides of the piston this time though. It tends to take a decent bit of force to get the clips to squeeze in there. It wasn't like they went in easy, but a little easier... enough that I did notice. I just thought, hey the tool is working great today and never put any more thought into it. I don't want to blame anyone else for what is probably a mistake of mine. It could be that I looked at the clip and didn't see that an end wasn't in or something and it popped right out because of that. The fact that the opposite side moved freely and was out of it's installed position paired with the tool working especially easy does make me wonder a little though. I can see some marking inside of the clip groove that still had a clip in it, so it could be that it was pressed against and worn enough to rotate freely in the 3-5 minutes that it idled and 2 seconds of light throttle. The other side where the clip came out looks clean and new, so that's probably saying I didn't get it in there right I guess. Haven't had time to look at it much. Gotta get ready to head out, but I wanted to post while I was replying anyway. Needless to say, this sucks. I don't even know if I'll be able to get it back together right away now. Trying to keep up with it has drained me and my wallet. So glad I've gone 0.01 quicker in the 1/8 mile so far for all of the trouble and expense. That justifies it totally. ðŸ˜
|
|
|
Post by aeroxbud on Jul 7, 2024 7:34:01 GMT -5
Just wow. When you think your luck must turn and soon. That's terrible. 😞
|
|
|
Post by xtremrox on Jul 7, 2024 8:37:00 GMT -5
That didnt do much(based my exhaust caculations on that map) only echaust port can be roughly caculated. The transfers are not to scale and no actual size data is given. The exhaust had width data and given that i know its timing i was able to roughly caculate its area I knew that wasn't what you were after, but I just got the cylinder back on so taking it off wasn't an option. It's off now though... I got up at 5:30 this morning and figured I had time to take a quick break-in ride before I had to get ready to be somewhere. Started up and idled OK with no drama. I started to move and was sort of surprised it didn't load up because I had put a 50 pilot jet in it, plus the 220 main and the 30 hole atomizer with the largest ID of the ones I have... and it was about 80F with 95% humidity already. Well, I was even more surprised when I got about 40-50ft and it shut off. Went to kick it and it was seized. WTH? I take the CVT cover off, thinking I just got this top end together and I've checked squish twice and I'm careful to keep the engine openings covered so nothing can fall in when it's apart so it has to be OK. CVT is fine. Can't move the variator in either direction. Uh oh. Then I think maybe something fell in to the stator/rotor and jammed up, but it's easier to pull the spark plug out first and look. I see nothing with just a flashlight. I get the borescope and a circlip is between the piston and the head. I hoped I got lucky and it wound up there without damaging anything. Not the case. I had to hammer the piston down, because the circlip was stuck between the bore and the piston and I couldn't get the cylinder off. I went to remove the circlip from the opposite side so I could get the pin out and it was in there with the opening aligning with the cutout in the piston. I know damn well I don't put circlips in like that. I stick a 90 degree end pick in there and all I have to do is twist my fingers with really no force and the clip moves around in it's groove. It should be pretty well stuck in place. The good news is, that made it easy to rotate it and pop the clip out at least. Here's what I'm looking at. Trash. 40-50ft on a brand new piston, cylinder kit with low miles because I just got it within the last couple of months too. 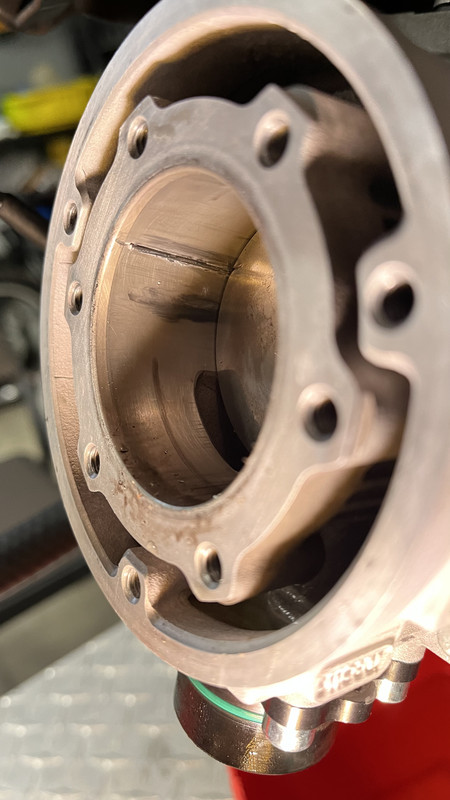 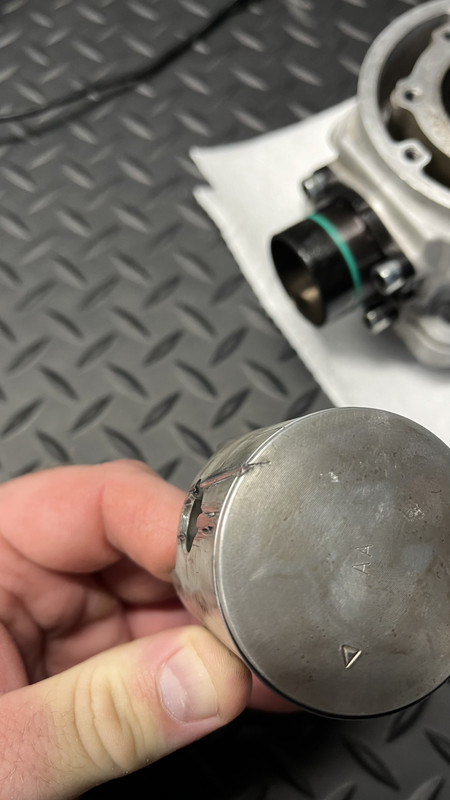 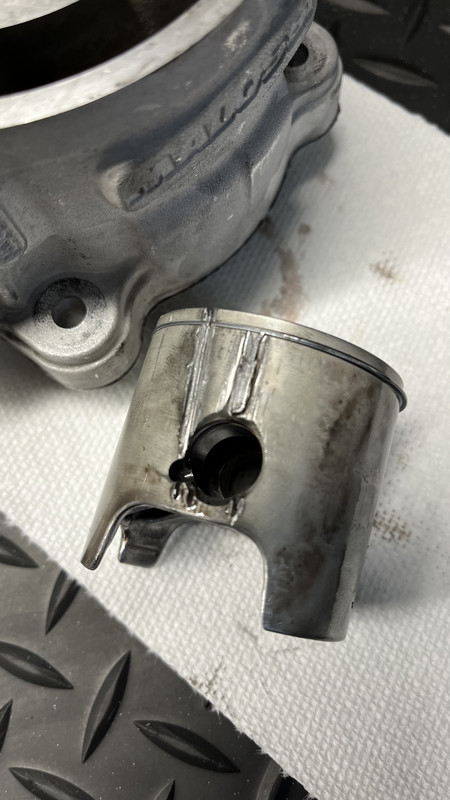 I use a special tool to install circlips. It's been great. Got the 13mm clip version at the same time I got the RC-One 2+ years ago and I've used it every time I've had to install a clip. There's an obvious click and a feeling as the clip goes into it's groove. When I first got it, I'd always go at it with a pick a little to make sure it was in there, but I've grown to trust it so I only do that now if anything looks suspect to me. I do look to see if the clip appears to be in though. I will say that I recall thinking the tool worked a bit easier than normal on both sides of the piston this time though. It tends to take a decent bit of force to get the clips to squeeze in there. It wasn't like they went in easy, but a little easier... enough that I did notice. I just thought, hey the tool is working great today and never put any more thought into it. I don't want to blame anyone else for what is probably a mistake of mine. It could be that I looked at the clip and didn't see that an end wasn't in or something and it popped right out because of that. The fact that the opposite side moved freely and was out of it's installed position paired with the tool working especially easy does make me wonder a little though. I can see some marking inside of the clip groove that still had a clip in it, so it could be that it was pressed against and worn enough to rotate freely in the 3-5 minutes that it idled and 2 seconds of light throttle. The other side where the clip came out looks clean and new, so that's probably saying I didn't get it in there right I guess. Haven't had time to look at it much. Gotta get ready to head out, but I wanted to post while I was replying anyway. Needless to say, this sucks. I don't even know if I'll be able to get it back together right away now. Trying to keep up with it has drained me and my wallet. So glad I've gone 0.01 quicker in the 1/8 mile so far for all of the trouble and expense. That justifies it totally. 😠Ohh that sucks. I have had this happen few times and i have figured that it is becouse of reusing the clips. When you put it in its desinged to be VERY close to its fatigue limits, so it presses very hard against the piston and it is harder to squeeze it any more so vibrations wont shake it off. But when you take the clip off it usually has to twist more than when putting it in and it almost allways twist a little sideways ant tries to jump out as one side gets free and the twisting force is relased. THAT is the end of life for the clip as its neutral size is now a fraction smaller and it has passed the point of no return to its original size and when you put it back it feels not so stiff becouse now it is just reshaping permanently, then the vibrations can vause it to rotate and when it reaches a point where the cutout is facing the exhaust it causes the clip to bend a lot, then when it tries to go back to the groove it can never go perfectly straigth in that causes a little twist as it hits the outer lip of the groove and then the top of the clip wedges between the piston and the cylinder. You can usually tell this by the groove being polished a bit or the lip of the groove having indents. It sucks that one so inocent looking piece is the cause of most catastrophic cylinder damages. One way to resovle this problem is to plug the pin hole like some diy race engines do to pervent shorting of trasfers there is mainly 2 ways i think 1.a high tempature plastic plug that goes inside the pin with interface fit and sit a bit inside the pin hole so it wont Touch the cylinder 2.a aluminium insert in the same orientation as the plastic one, or a inster that replaces the clip all together and sits on the clip groove(i dont know how the piston is modified for this and the installing would be pita becouse you have to instal the piston to the crank before the crank goes to the cases unless you use like liquid nitroqen ect Thats why factory race bikes just use piston pins with ends shut
|
|
|
Post by 190mech on Jul 7, 2024 16:11:33 GMT -5
So sorry! Do you think they might have sent 12mm clips instead of 13mm clips?
|
|
|
Post by 90GTVert on Jul 7, 2024 16:12:56 GMT -5
Ohh that sucks. I have had this happen few times and i have figured that it is becouse of reusing the clips. When you put it in its desinged to be VERY close to its fatigue limits, so it presses very hard against the piston and it is harder to squeeze it any more so vibrations wont shake it off. But when you take the clip off it usually has to twist more than when putting it in and it almost allways twist a little sideways ant tries to jump out as one side gets free and the twisting force is relased. THAT is the end of life for the clip as its neutral size is now a fraction smaller and it has passed the point of no return to its original size and when you put it back it feels not so stiff becouse now it is just reshaping permanently, then the vibrations can vause it to rotate and when it reaches a point where the cutout is facing the exhaust it causes the clip to bend a lot, then when it tries to go back to the groove it can never go perfectly straigth in that causes a little twist as it hits the outer lip of the groove and then the top of the clip wedges between the piston and the cylinder. You can usually tell this by the groove being polished a bit or the lip of the groove having indents. It sucks that one so inocent looking piece is the cause of most catastrophic cylinder damages. One way to resovle this problem is to plug the pin hole like some diy race engines do to pervent shorting of trasfers there is mainly 2 ways i think 1.a high tempature plastic plug that goes inside the pin with interface fit and sit a bit inside the pin hole so it wont Touch the cylinder 2.a aluminium insert in the same orientation as the plastic one, or a inster that replaces the clip all together and sits on the clip groove(i dont know how the piston is modified for this and the installing would be pita becouse you have to instal the piston to the crank before the crank goes to the cases unless you use like liquid nitroqen ect Thats why factory race bikes just use piston pins with ends shut Brand new clips. I got the circlip tool because it makes it easy, but it would also put less stress on it than me fumbling with it, I think. It’s worked multiple times and ultimately if it were an issue of it not getting in there then it’s my fault for not being more thorough. Hard to believe I wouldn’t have looked at the ends, but I’ve also learned that I can’t see like I used to close up anymore so who knows.
|
|