|
Post by ryan on Aug 23, 2013 8:52:39 GMT -5
i ran into the same thing exactly when i lost my bearing lol but there cheap enough to obtain.
|
|
|
Post by 190mech on Aug 23, 2013 9:16:17 GMT -5
Before you cut much more on the jug,make up a set of dummy main bearings and assemble the crank,piston and jug in the cases and check the port durations and squish.Figure how to get optimum durations from your measurements,then reassemble into one case half and look at how the piston,cyl skirts,transfer tunnels,etc match up...
|
|
|
Post by waltinhawaii on Aug 23, 2013 11:03:33 GMT -5
Thanks John. I'm not changing the opening/closing values yet (staying away from the top or bottoms of the ports) until I can do exactly what you are saying. Just trying to maximize the size of what I have for now, and clean up the flow a bit.
Ryan, thanks for the help!
|
|
|
Post by ryan on Aug 23, 2013 11:26:53 GMT -5
walt if you need a stroker crank i found one for a hell of a deal. message me
|
|
|
Post by 190mech on Aug 23, 2013 11:55:56 GMT -5
This is how your cylinder should look when done: 
|
|
|
Post by moofus02 on Aug 23, 2013 12:45:04 GMT -5
That looks awesome John I wish they looked like that from the factory lol
Sent from my SPH-L720 using proboards
|
|
|
Post by 190mech on Aug 23, 2013 14:13:48 GMT -5
Yeah,Me too!I think a lot of us would be limping around with serious injuries if we had them like that!!
|
|
|
Post by waltinhawaii on Aug 23, 2013 17:11:41 GMT -5
Those transfers are about the size of some people's apartments, John. I thought about slapping some steel to the outsides of the current transfers so that I could get them like that, with wide, sweeping arches and also, cutting off the existing cylinder transfer sides gives you acces to the actual ports from the sides and makes porting them much much easier, same as porting most exhaust ports is simple from the outside of the cylinder. But, adding material to the sides for more space in the transfers means having to do the same to the cases in order to have a case-to-cylinder seal. With the minarelli's the left side of the case is actually lower than the cylinder so having wide arches under the transfers will have the cylinder overhanging open air on the bottom when it meets the cases. So the cases will have to be beefed up and welded with aluminum bosses and then milled down to match the widened cylinder.... not a pretty picture is developing, even if you COULD avoid all those damn cylinder studs in the way. Thought about it for a LITTLE bit and sorta dismissed it as too much work. Possible to do it, probably, but who in his right mind would?? OK, so maybe I would have... 20 years ago... these days I tend to be a bit on the lazier side. Path of least resistance and all that. Hey, that's why I joined up here. YOU guys are supposed to develop all the crazy stuff and let me lean back and watch and marvel at all the perfectly good metal being turned into scrap 
|
|
|
Post by 190mech on Aug 23, 2013 17:58:00 GMT -5
Walt,Ive been trying lots of crazy ideas for years and the 'dud' pile just grows bigger,,You have a good understanding of what the Mina engine is about(hauling people around the world),its not a race bred engine!Looking at the 3 Ex port jug,I see possibly narrowing the area between the main and aux ports to 3-4mm,that would increase the aux flow a good bit without getting into the studs.Aux ports should open after the main Ex port.I agree on the transfers,If I was younger and had lots of time,I'd look into making up a better jug with "tea cup handle" style transfers..Splicing on a MX jug is a huge task,then the wimpy bottom end and paper thin cases buckle under the big load increase(how do I know that??).So I say,just enjoy your build,try for 130 degree transfers and 190 degree Ex durations,that ought to put a smile on your face!
John
|
|
|
Post by waltinhawaii on Aug 23, 2013 20:33:52 GMT -5
Hahahaaha,been there, done that... too. I once grafted an MX (Yamaha) jug onto a Puch case... the last bike I worked on before realizing there was no real future in trying to scatter most of my body across as much asphalt as possible. That engine graft required relocating the studs, not a fun job. But now that I'm older and not so wise, I find that I'm hankering for another ride so picked up the heap on page 1 of this thread and trying to get up to speed on the last few decades of 2 stroke development. Quite interesting. Port timings seem to have stabilized, but pipe development has allowed radical overlap of transfers and exh ports, they seem to not worry about sucking out new charge, they just restuff it back into the chamber before piston close and rely more on the pipe pulses than before.
Yes, I have come to the same conclusion, rework the sub exh ports and thin the webs between the subs and main to gain some area. Plan on drilling the piston above the bridges, though, to allow more cooling gas and oil to reach the bridges, so hope my layout is accurate enough to locate the holes correctly. We'll see.
|
|
|
Post by ryan on Aug 23, 2013 20:38:01 GMT -5
walt i sent you a message, i found a 45 stroker for almost 2 times cheaper than the hoca.
|
|
|
Post by 190mech on Aug 24, 2013 5:35:58 GMT -5
Great to have an "outside the box" builder here! When the Ex port overlaps the transfers,the piston sides must be round(no flats) as the two gasses will mix when the flats align.Here is a poor picture of a failed CR125 jug install on a Mina engine because of that very reason.  Your piston drilling is to connect the underside of the piston to the boost port for cooling?Like this example?  
|
|
|
Post by waltinhawaii on Aug 24, 2013 10:56:13 GMT -5
Hi John. The piston drilling is much smaller holes, near 3/32" if I remember right, and 3 or 4 of them all strung out vertically in a line right over the bridge. they don't pass gas to any real extent, they are only there to provide some oil and cool air to the bridge surfaces, which need the additional cooling so the bridge sitting in the exhaust stream does not overheat and 'bow' outwards. This makes the bridged designs much less susceptible to partial seizures. In my cylinder, they get around this by having a rather wide 'bridge'... in fact, the bridge is so wide it looks more like 'wall' than bridge, there is so much area in contact with the cylinder it is unlikely to get too hot. But thinning out the bridge by widening the main exh port or subs is likely to increase the heat load to the point it might start bowing. Traditionally you would hone down the bridge surface a few thousands under the height of the rest of the cylinder in anticipation of the extra heat loading. I don't have a hone (yet), will have to find a delisle or similar.
|
|
|
Post by waltinhawaii on Aug 24, 2013 11:15:06 GMT -5
John, so the flats you are referring to, are alignment of transfer and exh port margins? So if rounded more they don't mix as much? I have read Jennings (a long time ago) but don't have a copy of Bell yet. The last time I tuned one of these, they were more worried about the direction of the transfers and distance to the exh port/short circuiting the incoming mix. But modern designs are much closer than before and overlap has increased substantially, to the point that I see exh subports stacked over transfers sometimes.
Was the CR125 project yours? Why did it fail? Did it also use the stock pipe setup?
|
|
|
Post by waltinhawaii on Aug 24, 2013 13:45:15 GMT -5
The outside of the exh port is oblong; need to correct this. As it turns out, a socket I had on the table was about the correct size, so I used it as a template (notice the 'poor man's dye chem' ...aka sharpie marker); 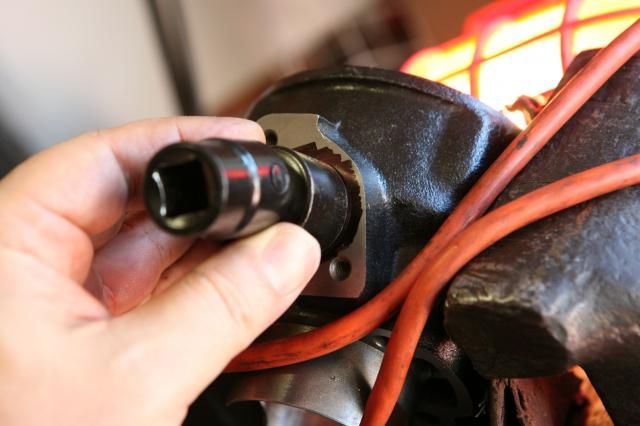 First attempt is centered on the existing port, and I probably should have left this, 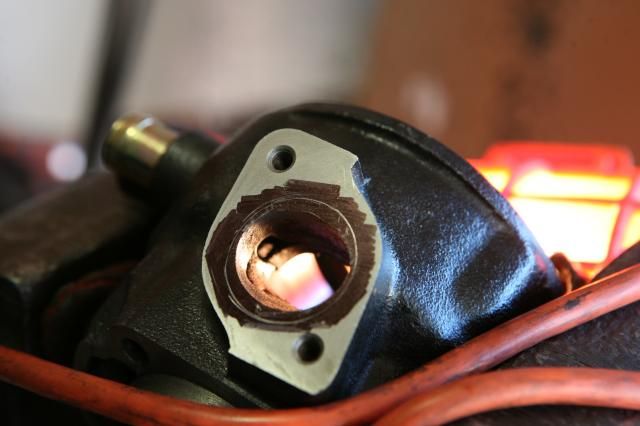 but it is close to one stud and about 2 times that distance to the other stud; so I reapplied the marker and traced out another hole. 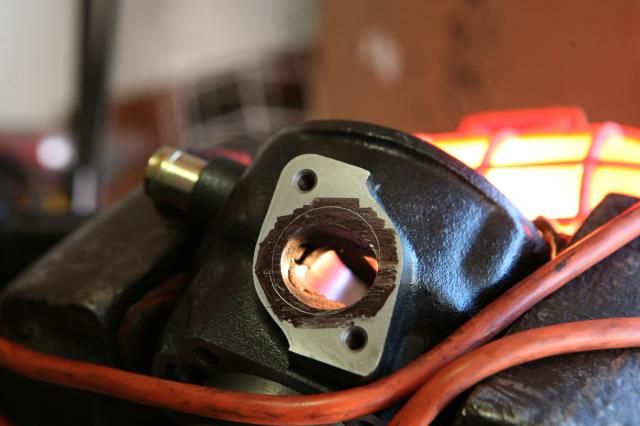 I briefly used the 90 degree right angle pneumatic on the exhaust port, but it was excruciatingly slow, so I looked around the shop (garage) and my eyes fell on the foredom, then on several 4 1/2" grinders and rejected all of them. Then I saw a rotozip case, still pretty new, that was donated by my father in law. Never used it before; so I got it out; ...it is HUGE compared to the tiny 90 degree pneumatic. I stuck it in the exh port with a carbide bit and WOW does it cut fast. Cast iron melts like butter before the carbide bit (still with a 1/8" bit too! ...wait till my 1/4" bits arrive....)
|
|