|
Post by waltinhawaii on Aug 24, 2013 15:27:34 GMT -5
This rotozip is like the 'ol dremel on steroids! Roughing out the exh port: 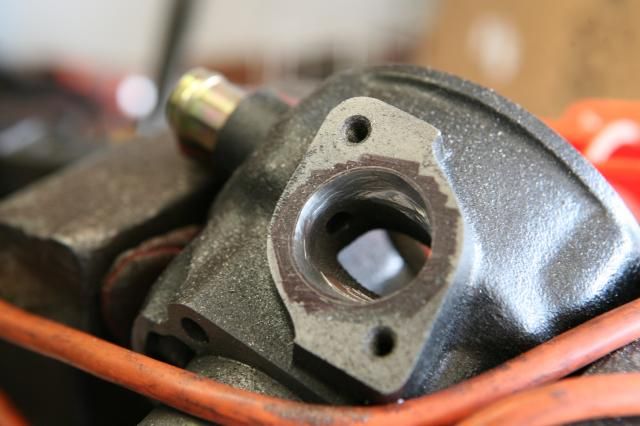 Notice I don't have my long bits yet, so I haven't touched the upper or lower edges of the exh port yet; no timing changes. Only widening the flange area to suit the pipe outlet better, with a nice round opening and derestricting the exh. Here I'm smoothing out the aperture:  Might as well knife edge the opening to the transfers while I'm here: 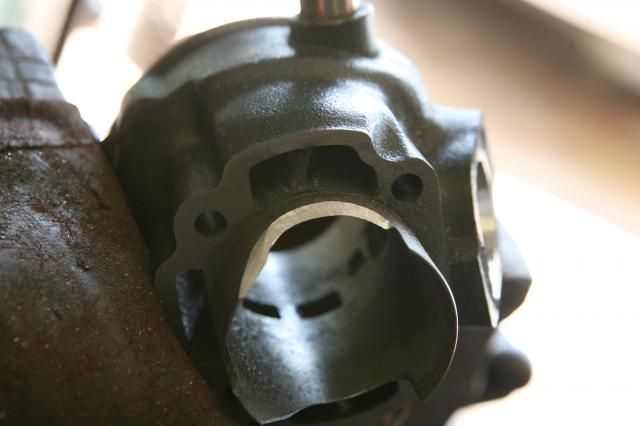
|
|
|
Post by 190mech on Aug 24, 2013 16:24:02 GMT -5
Walt,Sorry I missed that you were talking about Ex bridge cooling holes,thats a great idea if you are gonna slim down those bridges,,About piston flats,here is our dirt cheap scooter pistons;  Note the flat sides(bean counters saving metal) Here is a super high power Aprillia piston;  Note the round sides so no cross contamination can occur between the Ex and transfers.They also use piston pin plugs to help this problem too. Yes ,that was my CR125 build,,ended up using an RM 125 jug,it ran like stink till the paper thin cases gave up,,lessons learned.. No,No to knife edges!!Think of this flow as a non supersonic aircraft wing,smooth rounded curves to guide the airflow and not causing tumbling around sharp edges!Here is a pic of the RSA125 cyl base,note how smooth the edges are?  Triple Ex ports like wide Ex outlets,here is the Aprillia RSA125 again; 
|
|
|
Post by waltinhawaii on Aug 24, 2013 21:18:41 GMT -5
Beautiful cylinder! Haven't seen enough modern cylinders... still learnin'. sorry, poor choice of words. My knife edges are not very sharp, but definitely sharper than the RSA above. The 52mm jug has very thin walls anyway, maybe I should have left them alone; but very rough casting. Trying to pull the transfers down a little toward the exh port to give a bit more area; very slow work. I've enlarged the sub exh ports very slightly, but the main connection into the main exh port is still very clogged. Can't do too much about that, though, they sit right over the lower studs so making the tiny connections into the main exh port larger risks holing into the stud tunnel cavities... which I can't easily fix. too tired to post pics, will do some tomorrow.
|
|
|
Post by waltinhawaii on Aug 25, 2013 21:13:32 GMT -5
Well, time to do some port mapping and to do that, I need some duration numbers. To get those, I need test bearings which will hold my working crank in the proper position but will be loose enough to get in and out of position without pressing. So, my old crank came out with one bearing still attached and one bearing in pieces... but for this exercise I think one tight bearing should do it... have to get the bearing off. To get it slightly off the seats, I tapped in two screwdrivers from opposite sides to move the bearing slightly; then used a pickle fork to move it the rest of the way off the crank (yes, that is a heat gun on the left of the crank, had to heat it bit to get it to move): 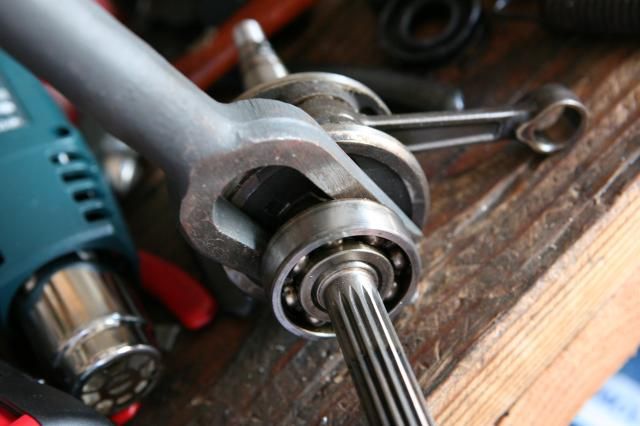 The crank seat is too obstructed to get calipers in there directly, so I had to measure using calipers and then measuring the calipers. For those of you following along, you can see just to the right, some distortion and melting of the cases; this is from the welding on the other side of the case and will have to be cleaned up. 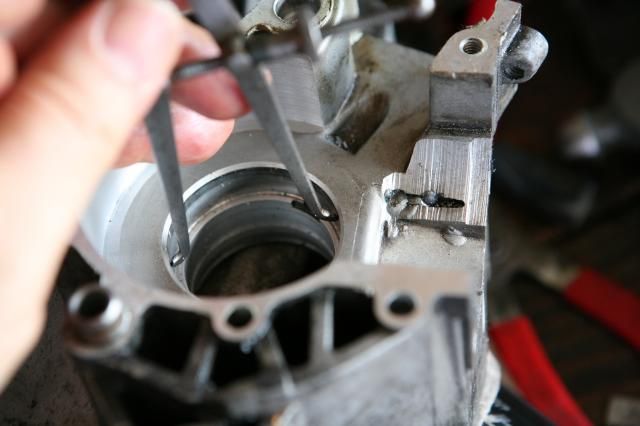 I got about 1.850" for the bearing seat diameter. The bearing OD measured 1.8515", give or take. Lined up the bearing in the lathe (I planned to cut a couple thousandths off one side, then flip the bearing over and cut the other half 1.5 thousandths)runout is less than half a thousandth: 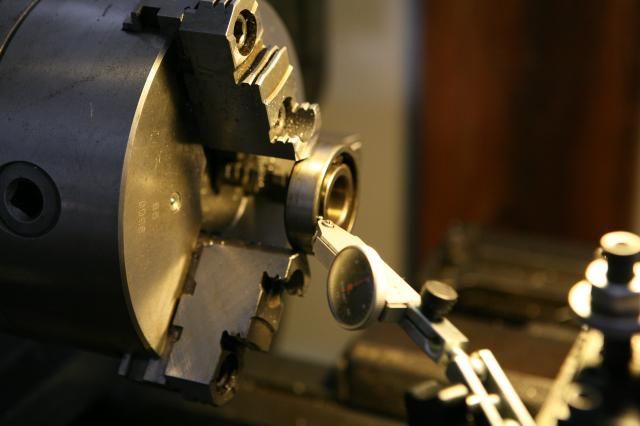 This is a photo after taking a cut with a carbide bit. If you look very carefully, you can see some slight shiny marks where the bit did a little bit of cutting between the jaws, then as you get closer to the jaws, the metal shows no evidence of cutting. This tells me 2 things; the metal is VERY hard so that even the carbide bit is having a hard time cutting it; and more importantly, the metal ring is being deformed, the race is pressed in slightly by the chuck jaw so it is being machined into a slightly out of round shape which will probably rebound when released from the chuck. This is not good. I'll have to find another way to reduce the diameter of this bearing shell. 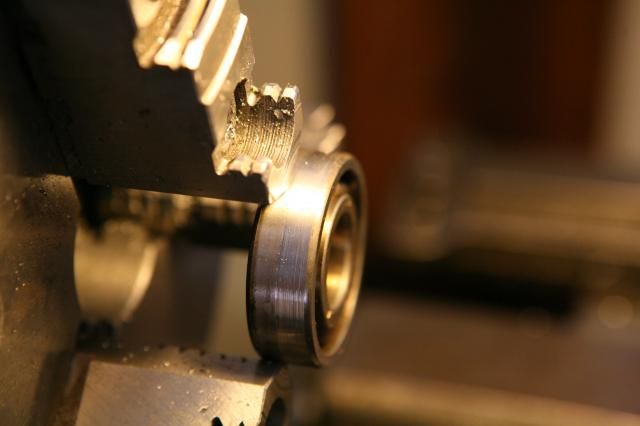 I took the bearing and then rotated it by hand against a spinning flapwheel: 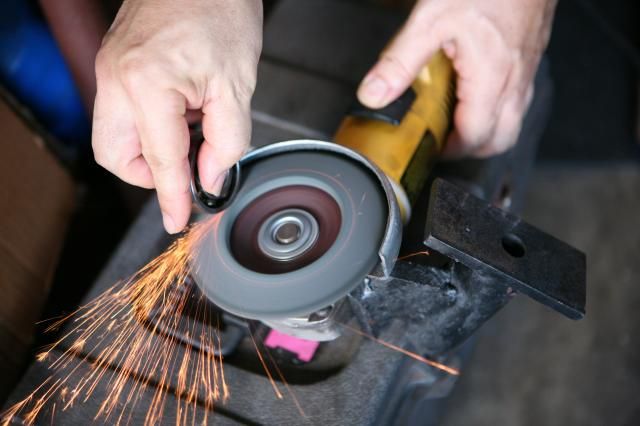 measured it and it had not changed dimension appreciably. Ah. OK, but it's a bearing... bearings spin. yes? so I put it back on the flywheel, took the flapwheel in hand and just put it against the bearing and let it spin while I sanded the outside; it rotated and tried to match the speed of the grinder, but I purposely moved the grinder so it would take a more crosswise cut, not along the same axis as the spin of the bearing. 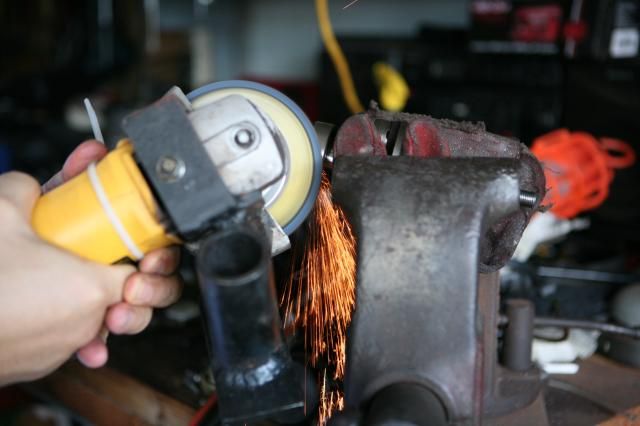 The grinder has an odd 'handle' on it because it's an old grinder that I don't use very often. I made this handle for it as a mounting device to use on my lathe as a grinder, to refinish gun barrels. 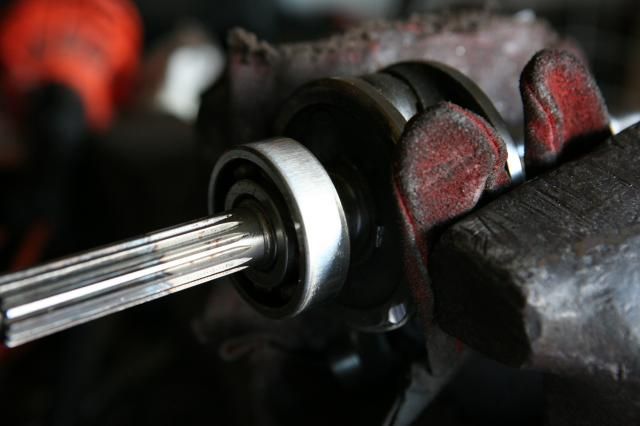 In about a minute the dimension had moved a few thousandths, enough to just fit into the case without pressing, but still tight enough so that there was no play. Now I'll have to find a way to do the inside of the same bearing... Don't have any flapwheels for the dremel.
|
|
|
Post by 190mech on Aug 26, 2013 4:09:10 GMT -5
Chuck it back in the lathe and use a stone on a dremel to open the inside up,the grit from the stone will jam the balls so the inner race wont spin while grinding..
|
|
|
Post by 2strokd on Aug 26, 2013 9:18:29 GMT -5
Great thread. Thought ide share some on John,s badass 125 build. The idea was great and honestly i still believe if we had a better case cast to start with this could be done to last?.. Tell ya what, the thing ripped while it did run!!!! Here is a pass when it was starting to come apart. If it had stayed together and i would have finished the day John,s build would still hold the record for the fastest ET at TwistandGone. Sorry to steer off topic. Been away all weekend 
|
|
|
Post by waltinhawaii on Aug 26, 2013 11:30:08 GMT -5
Brother, ain't no such thing as off topic if its got 2 wheels and can carry some groceries. Neat vid. How big was the field? Are there pics of the engine build? Is there a displacement limit/class? Sorry, I have no idea what the rules are. Used to be run what ya brung, but that's sort of an invitation to give the title away to whomever has the deepest pocket. Is the thick jacket for protection against roadrash? or is it that cold?
argh; work calls. Will be back tonight.
|
|
|
Post by 2strokd on Aug 26, 2013 11:55:04 GMT -5
Its not really that thick, its vented as well. Has a zip in liner. But yeah, protection mainly. A "real" riding jacket so to speak. I got it used, ide never pay the price for these things new. Field is all over the place. Should be pretty big this year?. Classes are heads up racing and range from bone stock to built engine/stock scooter frame, then to unlimited sprinter (drag frame). Ive got pics around here somewhere but no time to look em up right now, i gotta get back at it myself. Keep up posted, digging your work 
|
|
|
Post by 90GTVert on Aug 26, 2013 16:35:18 GMT -5
|
|
|
Post by waltinhawaii on Aug 27, 2013 0:06:39 GMT -5
Thanks for the info! ...but its in Indiana. Not known to be too close to Hawaii  what came in the mail today:  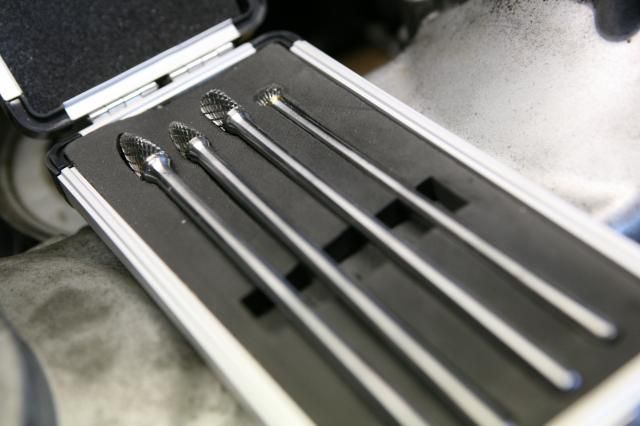 This is how I use the new long bits: 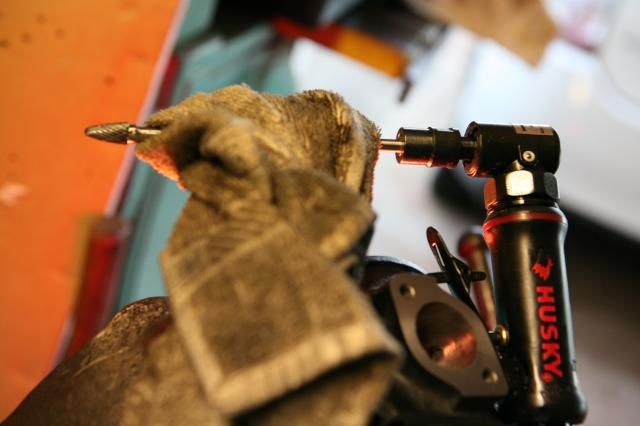 I suppose I could just put on thick leather gloves and grab the rotating shaft, but the towel is fine. I twist the towel so that it captures the shaft, then I have a two handed grip on the tool. My right hand has the pneumatic trigger; my left guides the tool. Works great. Here is what I'm doing to the aux exh ports: 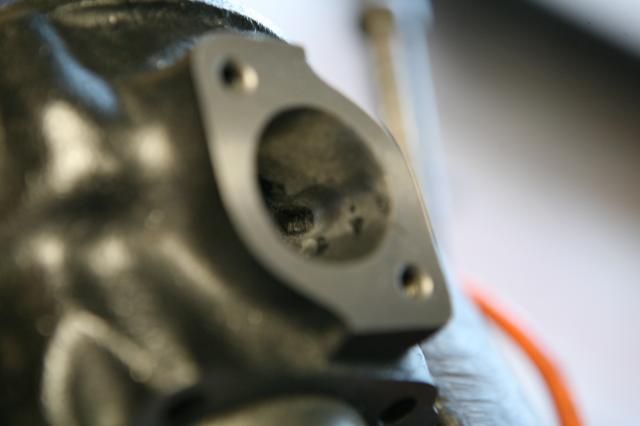 The subports were previously just little cast add ons to the main exh port. Now, I'm giving them their own real channel and a chance to flow some real gas, hopefully. As to the inside of the bearing, I picked up a stone with a 1/4" shank from Home Depot just now for $3.50... I was going to get a dremel stone, but they wanted like $9 for an itty bitty one that won't last me 1 minute. This big beefy one mounted in my rotozip: 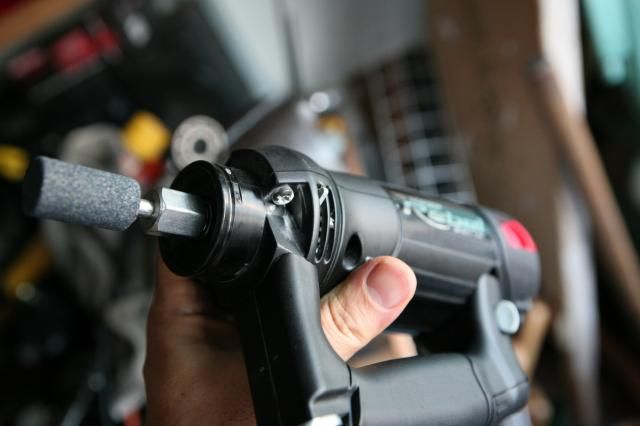 Welllllll, there, g'day mate. Now THIS is a grinder! After a minute or so with the bearing clamped in a vise and this stone sitting inside, it purrs right on the crank without play. Wonderful.
|
|
|
Post by 190mech on Aug 27, 2013 4:28:48 GMT -5
Gotta love them power tools!!
|
|
|
Post by moofus02 on Aug 27, 2013 8:33:11 GMT -5
Great thread. Thought ide share some on John,s badass 125 build. The idea was great and honestly i still believe if we had a better case cast to start with this could be done to last?.. Tell ya what, the thing ripped while it did run!!!! Here is a pass when it was starting to come apart. If it had stayed together and i would have finished the day John,s build would still hold the record for the fastest ET at TwistandGone. Sorry to steer off topic. Been away all weekend  First time I've watched a video of you at the track that thing rips Sent from my SPH-L720 using proboards
|
|
|
Post by 2strokd on Aug 27, 2013 10:44:40 GMT -5
Thanks man, not bad for an engine literally coming apart during that pass huh?. The next pass was for the trophy. Left the line hard! Got about 150ft out and it let go all the way! Good thing for that solid Peace Pipe! It was the only thing holding the complete top-end on! here are a few pics of the cracked cheap china casting. Everything else worked out well on this thing. I do believe we could have chiseled it into the very low 8,s anyhow. Maybe better?    Here is a time slip from that day.. Keep in mind (MPH really shows) it was coming apart and ran this lol  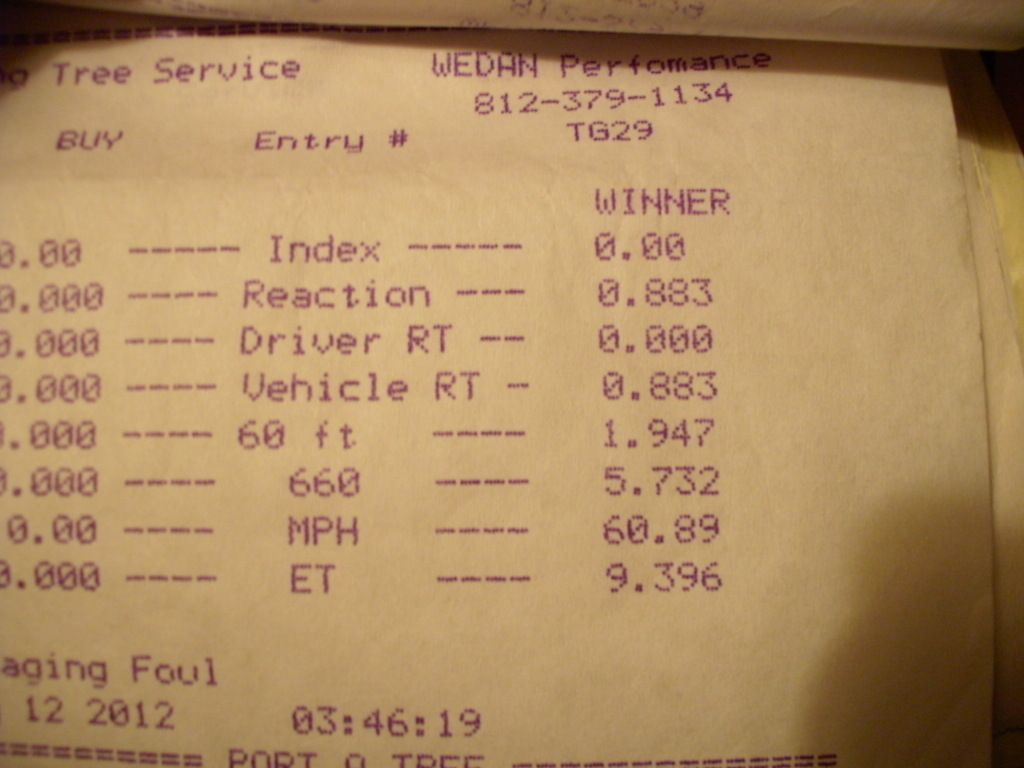
|
|
|
Post by moofus02 on Aug 27, 2013 13:21:51 GMT -5
Couple big blocks of billet aluminum and make your own cases lol. There is a guy up here sand dragging with a super charged 4.3l v6 on alcohol with large shots of nitrous. His entire engine is carved from a single chunk of billet alloy cause he kept breaking blocks. He has been using this motor for about 15 years. It is impressive
Sent from my SPH-L720 using proboards
|
|
|
Post by 190mech on Aug 27, 2013 14:12:57 GMT -5
Your sand drag buddy has something we aint got,,MONEY!!! 
|
|