|
Post by 90GTVert on Feb 26, 2010 8:32:46 GMT -5
Looks good. I've got a bit of practice and you can see I did the same thing once on the left side of my modded boost port pic. The main thing is to take your time, at least for me. I find that as soon as I try to rush things, I do something like that.
|
|
|
Post by 2strokd on Feb 26, 2010 11:28:45 GMT -5
Yep, your right. I was either pushing it, or not positioned right when i had my little runoff.
|
|
|
Post by 190mech on Mar 3, 2010 21:39:32 GMT -5
How is the stroker project coming?  
|
|
|
Post by 90GTVert on Mar 3, 2010 22:13:25 GMT -5
It's not. Machinist never showed up like he said he would or let me know anything. I'm gonna see if he's around the shop again yet or if I gotta call again and set something up. I thought I'd have my cases back around now when I started trying to get in touch over a week ago. 
|
|
|
Post by 90GTVert on Mar 5, 2010 22:30:40 GMT -5
I expanded my collection of files thanks to Harbor Freight. All of these files were about $20. 5 large files, 12 needle files, and 10 diamond needle files. 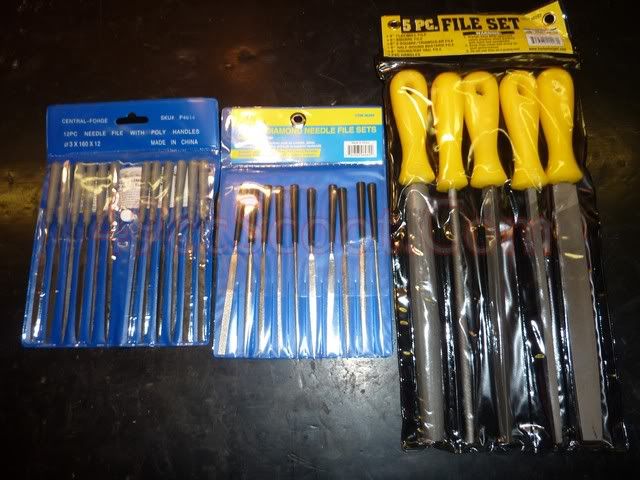 The needle files make getting into boost and transfer ports so much easier. 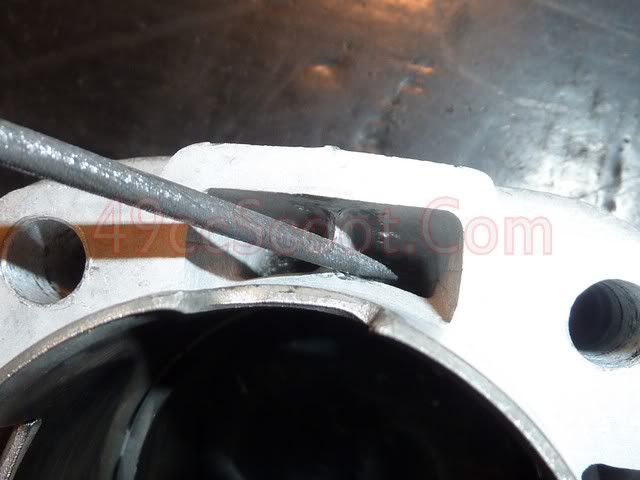 The diamond files are a little more fine, so having both makes a great kit. Start off with the standard steel files and finish with the diamond files. 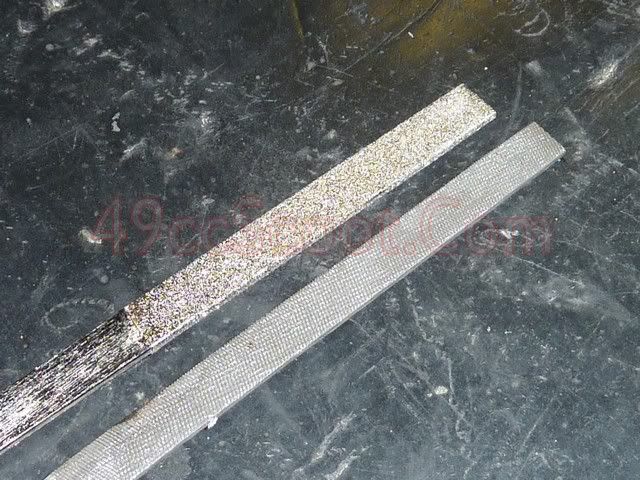 Here's the knife edging job on my Airsal as completed by the dremel and the files I had before. 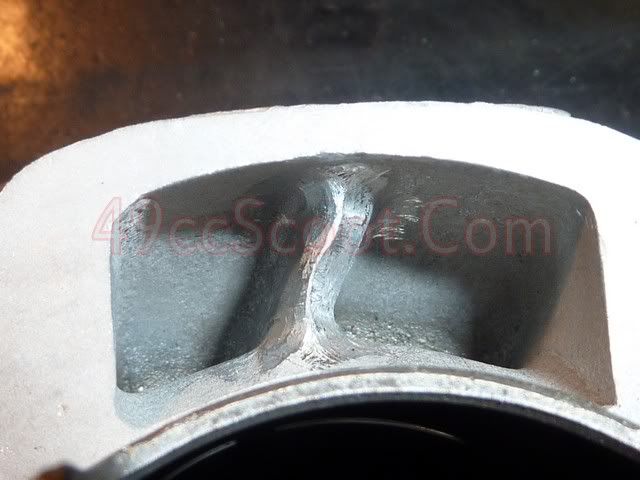 Here's the same port after a little work with precision files. 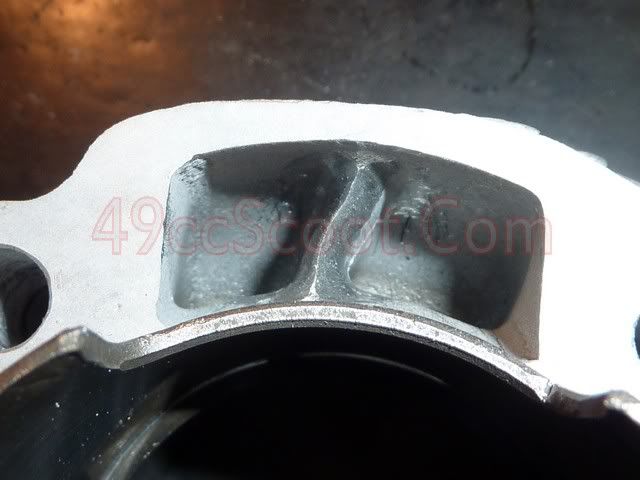 I highly recommend spending the money on at least one set of needle files if you are going to do any port work.
|
|
|
Post by 2strokd on Mar 6, 2010 7:55:07 GMT -5
That looks REALLY nice Brent! Im getting a set for sure, those are worth the money for sure. Good post. Great work!
|
|
|
Post by 90GTVert on Mar 6, 2010 9:18:25 GMT -5
Thanks. I can't stress enough how much they help you do stuff like this. Now if I could just get some curved files or ball end precision files.
|
|
|
Post by 90GTVert on Mar 6, 2010 11:13:04 GMT -5
After all of this work trying to get nice knife-edges I read something that says it might be a bad idea. I'm not really sure, I have read conflicting statements from different sources. Apparently knife-edging is best in areas where the airflow on either side of the bridge or divider is equal. In that situation a knife edge will create the least amount of turbulence. If airflow is entering each side uneven the knife edge is said to create more turbulence than a rounded edge. To my understanding this is because the airflow "catches" on the edge if it tries to pass across is in any way other than straight on. A rounded edge would create a hump for air to pass over rather than a cliff. Hopefully my explanation makes some sort of sense. I would think that means knife edging would still be best for the exhaust bridge, but I'm not sure about the transfers with their curves. Any thoughts or input?
|
|
|
Post by stepthrutuner on Mar 6, 2010 13:52:35 GMT -5
After all of this work trying to get nice knife-edges I read something that says it might be a bad idea. I'm not really sure, I have read conflicting statements from different sources. Apparently knife-edging is best in areas where the airflow on either side of the bridge or divider is equal. In that situation a knife edge will create the least amount of turbulence. If airflow is entering each side uneven the knife edge is said to create more turbulence than a rounded edge. To my understanding this is because the airflow "catches" on the edge if it tries to pass across is in any way other than straight on. A rounded edge would create a hump for air to pass over rather than a cliff. Hopefully my explanation makes some sort of sense. I would think that means knife edging would still be best for the exhaust bridge, but I'm not sure about the transfers with their curves. Any thoughts or input? I seem to remember reading the same thing about the xfers.... probably on ScooterInvasion. On the ex. prt. bridge it is probably good.
|
|
|
Post by 90GTVert on Mar 6, 2010 14:31:04 GMT -5
I was reading it on an automotive forum about intake manifolds. I did some more searching and saw that Mac Dizzy, OverRev, and others do not recommend knife edges on the transfers. Oh well, live and learn.
|
|
|
Post by 190mech on Mar 6, 2010 21:38:33 GMT -5
Kinda like an aircraft wing,the airflow should smothly sepreate, not be 'cut' as this causes turbulance..Read in a motorcycle mag back in the 70's about heating a file and bending it,loses some hardness,but cuts aluminum well..Some of my best port tools are old bent files!
|
|
|
Post by 90GTVert on Mar 6, 2010 23:16:32 GMT -5
Good tip. ;D I guess I'll have to get another set of the regular steel files and start bending.
|
|
|
Post by 2strokd on Mar 7, 2010 7:30:31 GMT -5
Hey, good find! Its still not too late to 'dull our knives' lol. You did such a good job to! Call it 'more practice' i guess. Kinda makes me wonder if the length of the the bridges in the transfers would make a difference and how? Or if it would even be safe to remove much?
|
|
|
Post by 90GTVert on Mar 7, 2010 8:33:39 GMT -5
From HERE... "The bridge between transfer runners should not be overly short or the ports will flow at different rates. When the piston is at B.D.C. the bridge is at the level of the piston pin."I saw someone ask about removing transfer bridges when i was looking yesterday and they were advised not to. While searching for some info, I came across THIS... "Lubrication holes (2-cycle engines) If the cylinder has an exhaust bridge, the piston should contain lubrication holes on the skirt where it contacts the exhaust bridge. If the piston does not have the lubrication holes on the skirt, follow these steps to drill the lubrication holes. 1. Install the piston and wrist pin on the connecting rod using one circlip. 2. Slide the cylinder over the piston and align it to its normal position on the crankcase. 3. Slowly turn the engine over until the bottom ring groove is at the top of the exhaust bridge. 4. Reach through the exhaust port with a pencil, and mark a vertical line on the piston on both sides of the exhaust skirt. 5. Remove the cylinder and piston, and drill 2 holes (.060 - .090” diameter), .375” apart, starting .300” below the bottom ring, and between the pencil lines. (See illustration B) 6. Remove all burrs from the lubrication holes, and clean the piston thoroughly."
|
|
|
Post by 2strokd on Mar 7, 2010 9:14:34 GMT -5
THANKS!
|
|